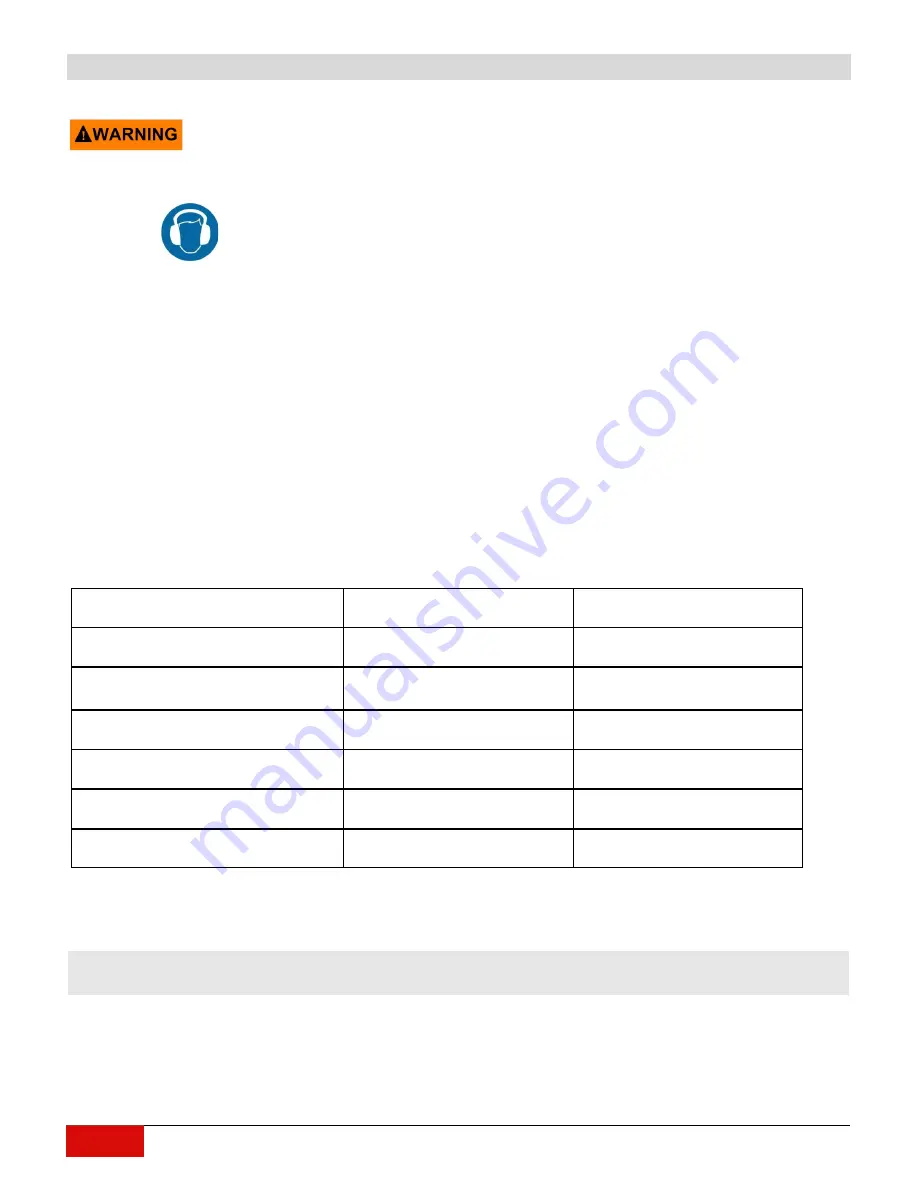
NOISE LEVEL & EMISSIONS
The typical A
-
weighted noise level determined according to
EN60745
:
Sound pressure level (LpA): 85 dB (A)
Sound power level (LWA): 98 dB (A)
WEAR EAR PROTECTION
Emissions during actual use of the machine can differ from the declared values depending on the ways that the
machine is used. Safety measures to protect the operator should be determined by actual conditions, taking into
account all aspects of the operating cycle (such as when the machine is switched off and when it is running idle).
Due to continuing product development, the specifications herein are subject to change without notice.
13
This section contains important safety information. Failure to comply could result in serious injury or loss
of hearing.
Hand vibration levels depend on the tool head distance to user and working conditions. Vibration levels in here
have been measured in lining removal work. Vibration has been determined according to ISO
-
5349 and EU
-
directive 2002/44/EG. In table above are shown safe daily exposure time for user.
Exposure Action Value (EAV) 2,5 m/s
2
Exposure Limit Value (ELV) 5,0 m/s
2
VIBRATION
Tooling
EAV
ELV
Smart Sweeper with drill head
1h 5 min
4 h 22 min
Smart Sweeper with Crasher head
2 h 47 min
11 h 8 min
10 h 46 min
Over 24 h
Premium Cyclone Chain
15 h 58 min
Over 24 h
Smart Crusher DN100
55 min
3 h 38 min
Smart Cutter
™
DN150
9 h 58 min
Over 24 h
14
Picote Solutions Oy Ltd www.picotesolutions.com
Values in the table have been measured in controlled environment in Picote Training facilities during pipe cleaning or liner
removal work. Liner material in tests was polyester which epoxy resin hardened and time
-
cured hard.