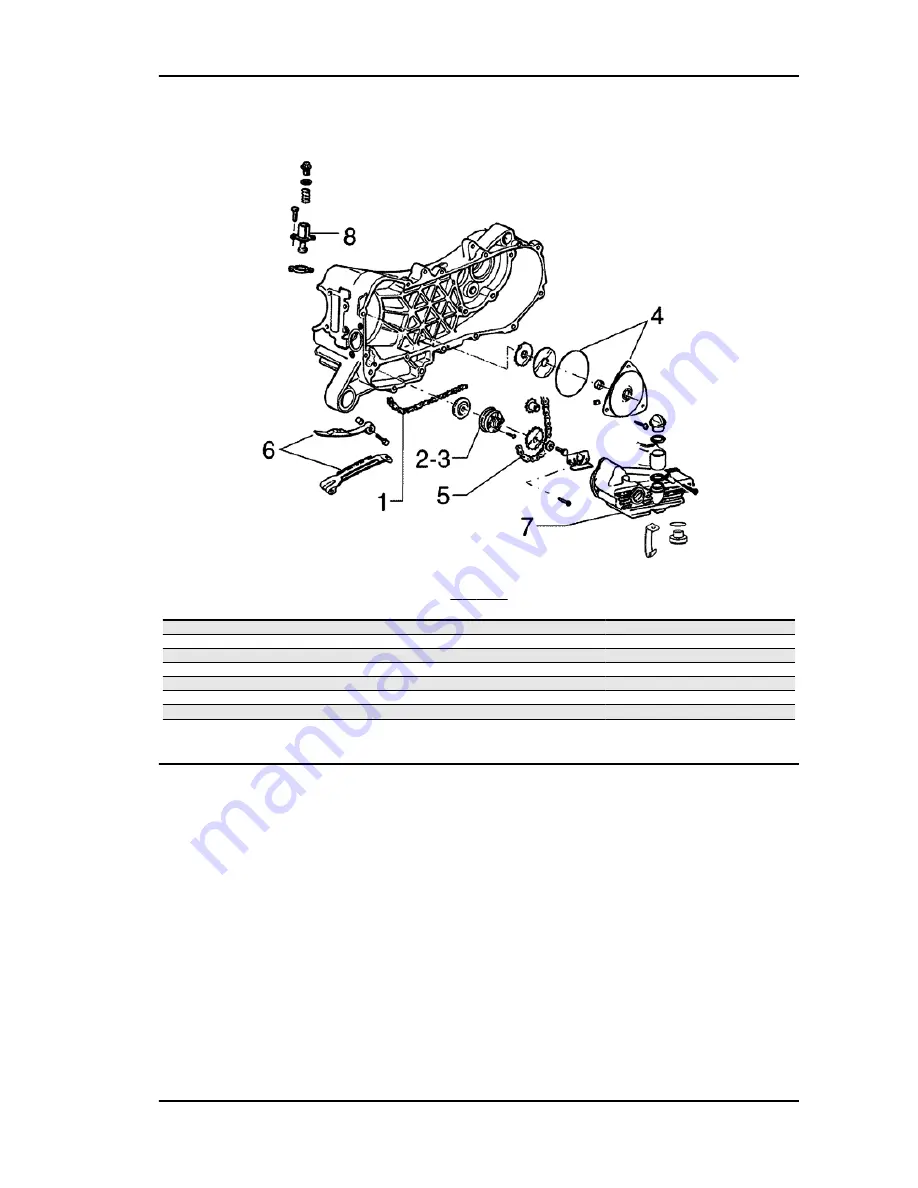
Oil pump
O
IL
PUMP
Code
Action
Duration
1
001051
Belt/Timing chain - Change
2
001112
Oil pump - change
3
001042
Oil pump - Service
4
001121
Chain cover oil seal - Replacement
5
001122
Oil pump chain - Replacement
6
001125
Chain guide pads - Replacement
7
001130
Oil sump - Replacement
8
001129
Chain tightener - Overhaul and re-
placement
MSS ZIP 100 4T
Time
TIME - 161
Summary of Contents for MSS ZIP 100 4T
Page 1: ...SERVICE STATION MANUAL 633734 633741 MSS ZIP 100 4T...
Page 4: ......
Page 6: ...INDEX OF TOPICS CHARACTERISTICS CHAR...
Page 17: ...INDEX OF TOPICS TOOLING TOOL...
Page 25: ...INDEX OF TOPICS MAINTENANCE MAIN...
Page 38: ...INDEX OF TOPICS TROUBLESHOOTING TROUBL...
Page 46: ...INDEX OF TOPICS ELECTRICAL SYSTEM ELE SYS...
Page 63: ...INDEX OF TOPICS ENGINE FROM VEHICLE ENG VE...
Page 65: ...INDEX OF TOPICS ENGINE ENG...
Page 95: ...MSS ZIP 100 4T Engine ENG 95...
Page 128: ...INDEX OF TOPICS SUSPENSIONS SUSP...
Page 136: ...INDEX OF TOPICS BRAKING SYSTEM BRAK SYS...
Page 145: ...INDEX OF TOPICS CHASSIS CHAS...
Page 149: ...INDEX OF TOPICS PRE DELIVERY PRE DE...
Page 153: ...INDEX OF TOPICS TIME TIME...