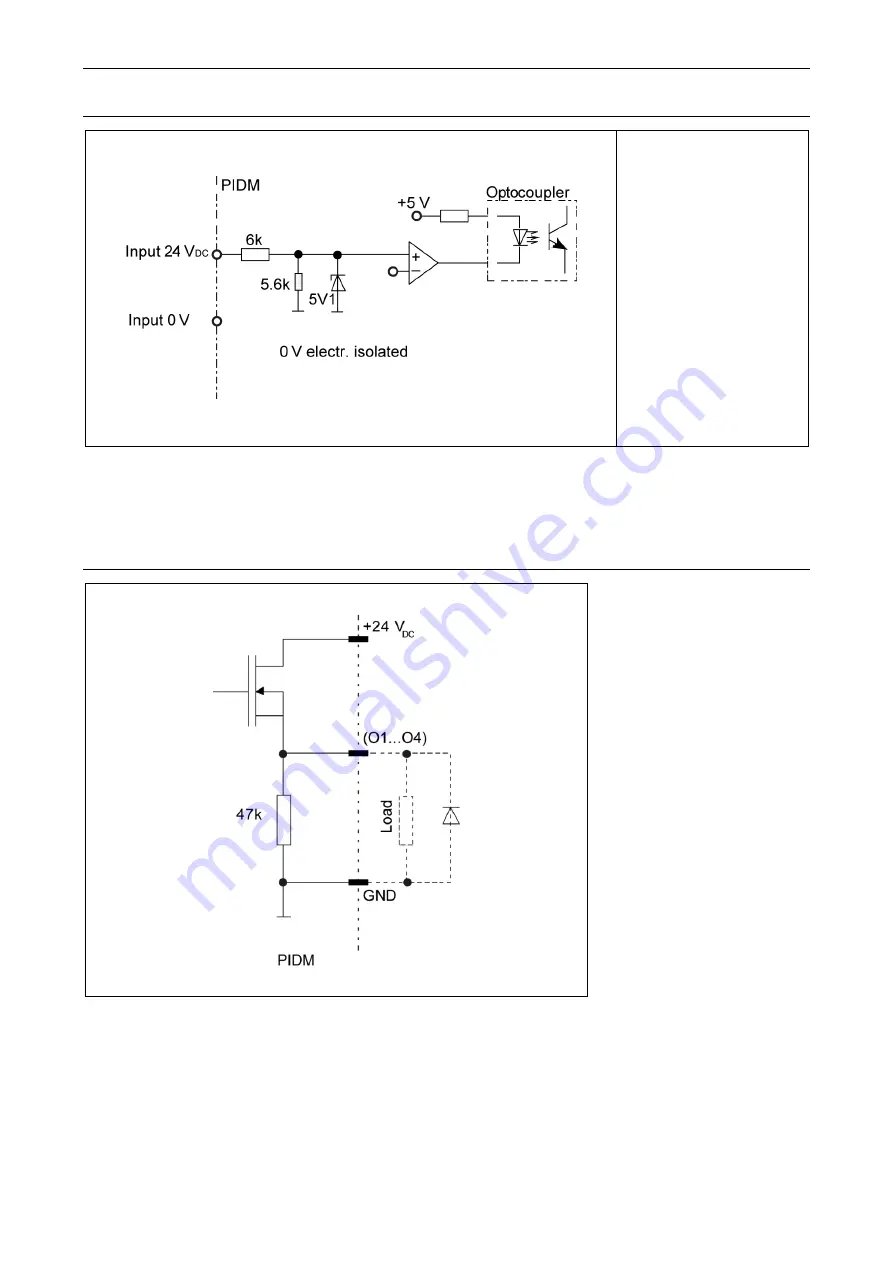
Manual PIDM01
MA 1311-A001 EN
18
5.2.3 Input Wiring
Switching threshold
2.4 V
Fig. 3: Input wiring
5.2.4 Output Wiring
Fig. 4: Output wiring
i
CAUTION
– Possible damage!
Damage of the module because of incorrect connection.
- Do not swap the 4-pin connector for the four inputs with the 4-pin
connector for the outputs.