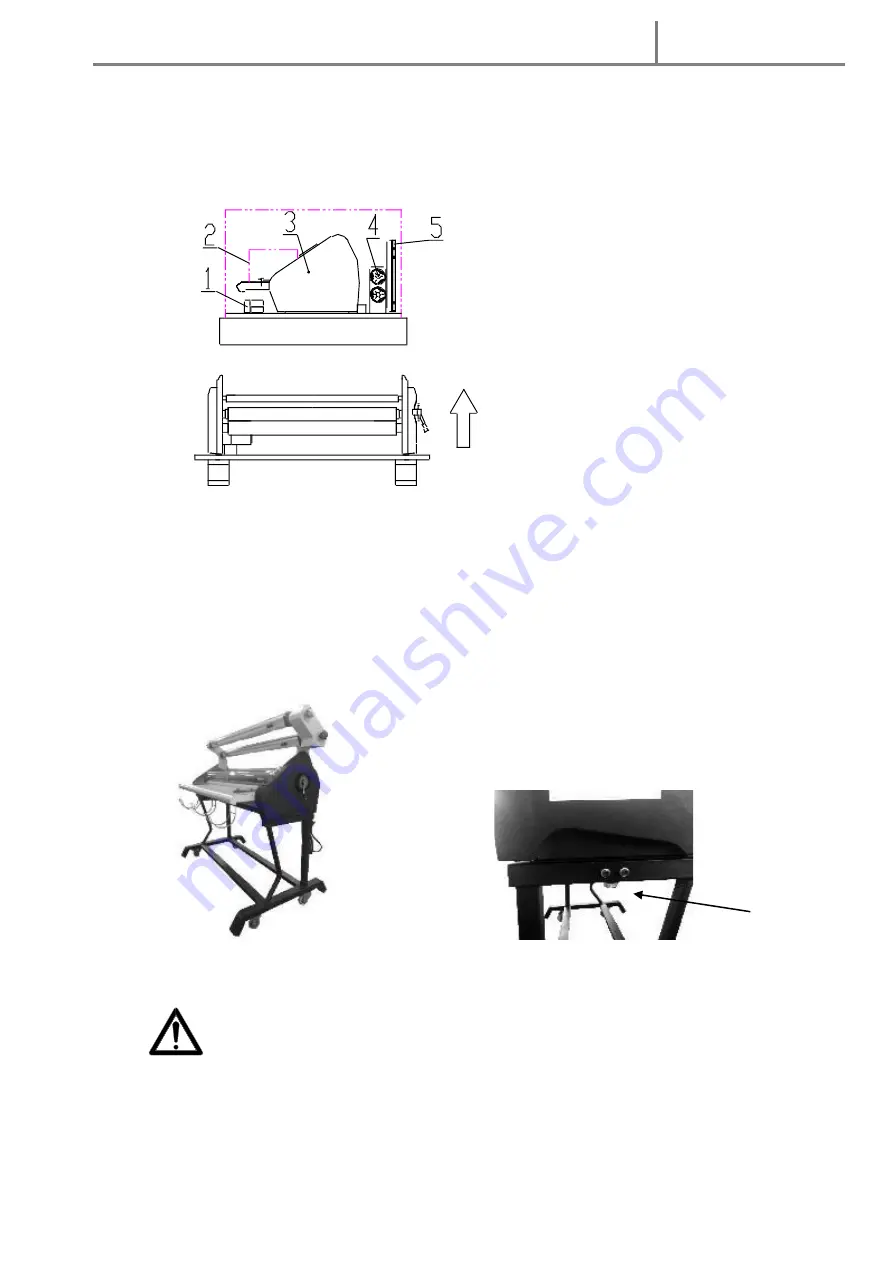
Phoenix 440-ML
January 2020
9
8c. Remove the machine from base
1.
Remove accessory boxes, shafts, and other components around the machine
2.
Pull back plastic dust cover around the machine
8d. Bolt Machine to the Stand
1.
Position the assembled stand close to the base and orient it to the machine. Stand
locking wheels are to the front of the machine.
2.
Lift the machine and set it on the stand
3.
Secure the machine to the stand using securing bolts in the accessory box.
Heavy! Handle with care!!
Warning: when moving the machine, lift by the machine side frames. Do not use
roller gap adjustment handle for lifting!
Locking bolt
1.
Stand cross members
2.
Rewind housing boxed
3.
Machine
4.
Unwind/rewind shafts
5.
Rear platform assembly