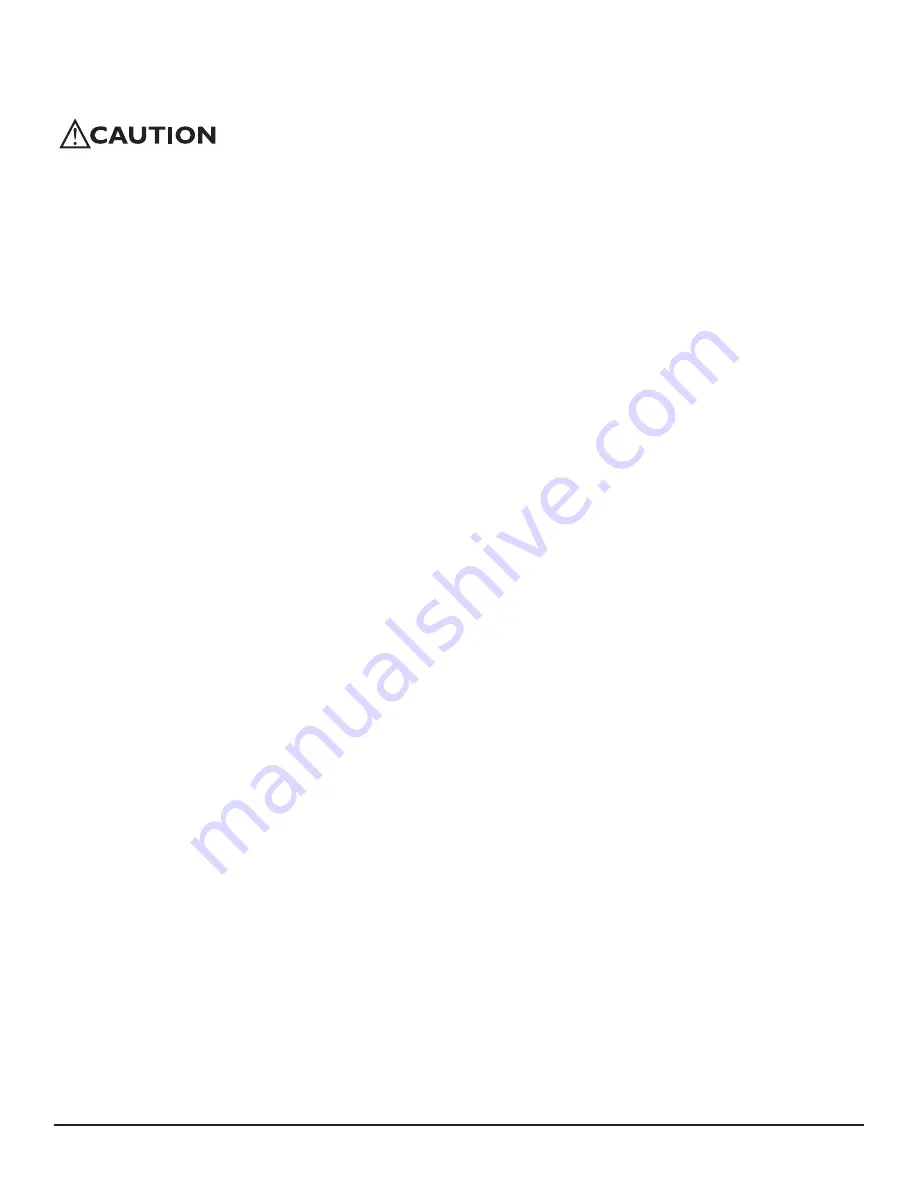
10
www.UsePhoenix.com • [email protected]
Toll-Free 1-800-533-7533
6. Maintenance
6.1 Service Instructions and Checks
“CAUTION: Label all wires prior to
disconnection when servicing controls. Wiring
errors can cause improper and dangerous
operation. Verify proper operation after burner
adjustment and servicing
A. To achieve and ensure clean combustion from the
burner, a “flue-gas analyzer” and “smoke spot tester”
must be used to verify clean combustion. Perform the
following checks while the burner is firing. Must be
performed by a trained service technician ONLY. These
checks should be performed, every time, when putting the
system into operation on a new project and a minimum of
once yearly.
a. Before starting the burner, determine that the
combustion head is set at 3.0 and the correct nozzle
is in place (Delavan 1.65-60ºB).
b. Fire the burner and ensure that the oil pressure is
at 180 PSI. Adjust if necessary.
c. Regulation of combustion air flow is made by
adjustment of the manual AIR ADJUSTMENT PLATE.
Initial suggested setting is (4.2).
d. Final position of the air adjustment plate must be
set based on instrument readings of not greater than
13.0% CO2 and a smoke spot reading of zero. Final
readings must be taken with all service-access doors
closed.
B. After placing this unit in operation, the ignition system
safety shutoff device must be tested. Must be performed
by a trained service technician ONLY. Refer to the Riello
manual, 40-F10 for burner component identification and
further instructions. This check should be performed, every
time, when putting the system into operation on a new
project or a minimum of once yearly.
a. Shut OFF the “burner circuit” power switch.
b. Remove the primary control box from the burner
and place a small piece of dark tape over the light-
sensing, cad-cell eye that senses the presence of
flame in the combustion chamber. Put the primary
control back in place.
c. Turn the power switch back ON and initiate burner
lighting procedure. After the short pre-purge cycle, the
burner should light but go out in 5 seconds and lock
out. If the burner does not lock out with the cad-cell
eye covered, the primary control should be replaced.
d. To put the unit back in standard operating mode,
turn OFF the burner circuit power switch, remove the
tape-cover from the burner’s primary control box,
re-insert the control and turn ON the “burner circuit”
power switch.
C. Examine the flue gas exhaust pipe and rain cap to be
sure they are solidly attached and free from any type of
obstruction. Clean if necessary.
a. This check should be performed, every time, when
putting the system into operation on a new project or a
minimum of once yearly.
D. After placing this unit in operation, the low water
safety shutoff device must be tested. Must be performed
by a trained service technician ONLY. The low water cutoff
switch is located in plain view at the same end of the
FireBird HD308 as the circulating pump and is identified
with a label.
a. Push the test switch on the outside of the control.
This will simulate a “low water” condition and open the
burner circuit to prevent burner initiation.
b. By pushing the reset switch, the control will
restore function to the burner circuit as long as there
is fluid touching the probe. The electronic probe is a
“self cleaning” type and should not require service.
c. This control should be tested every time, when
putting the system into operation on a new project or a
minimum of once yearly.
E. After placing this unit in operation, the high
temperature limit safety shutoff device must be tested.
Must be performed by a trained service technician ONLY.
The high temperature limit switch is located in plain view
at the same end of the FireBird HD308 as the circulating
pump and is identified with a label.
a. With the burner firing, set the digital operating
control to a temperature value that is at least 5ºF
higher than the setpoint of the high temperature limit
switch.
b. When the fluid temperature reaches the level of
the high limit setpoint, it should shut down the burner.
c. The high limit will need to be manually re-set, by
pushing the red re-set button to return to the operating
mode. Adjust the operator back down to the lower
setting.
d. This control should be tested every time, when
putting the system into operation on a new project or a
minimum of once yearly.
F. After placing this unit in operation, the high pressure
safety shutoff (blocked-flue) device must be tested. Must
be performed by a trained service technician ONLY. The
high pressure cutoff switch is located just below and to the
left of the burner and is identified with a label.