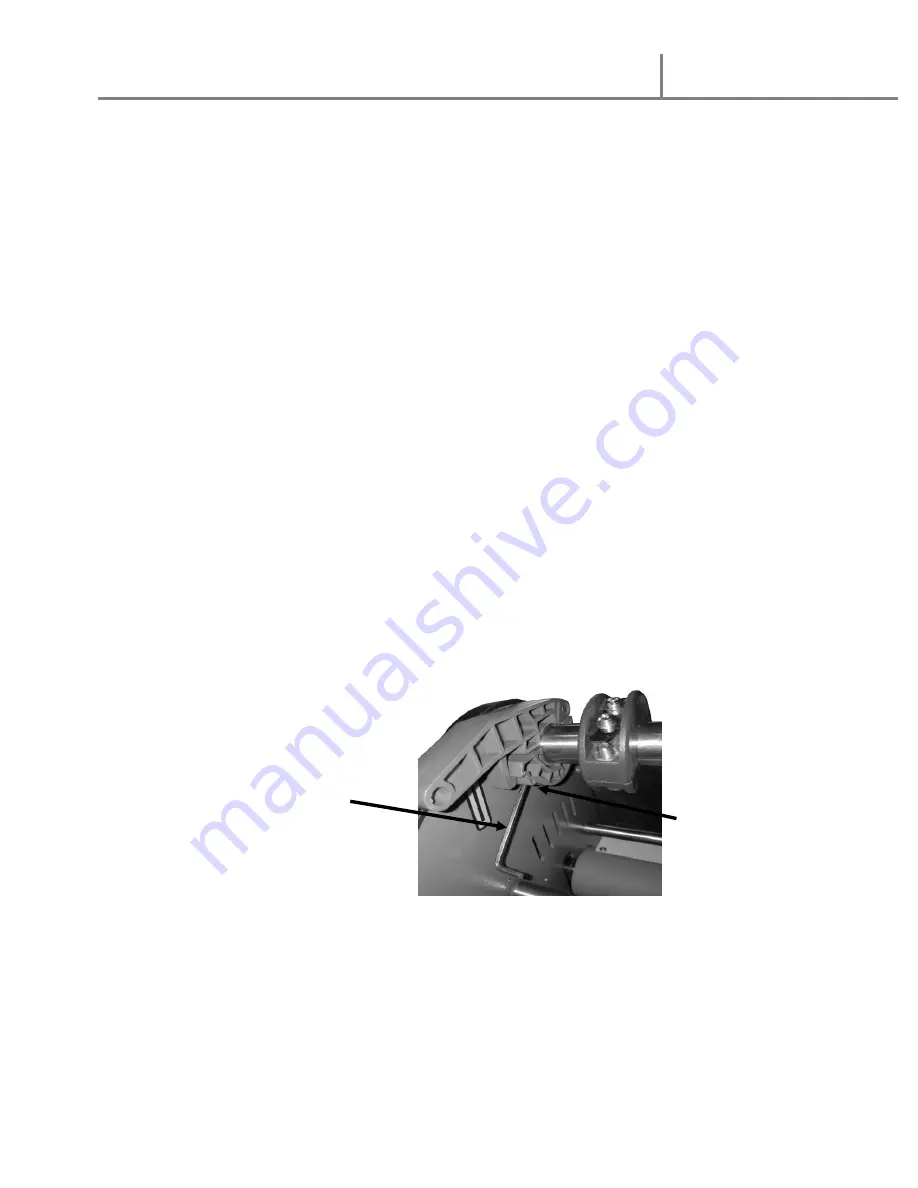
Phoenix 2700 DH
July 2018
20
7.
Return the feed table into position and lock the safety interlock
8.
Return the safety shield into position and lock safety interlock
9.
Use the motor switch on the control panel to advance the film web
through the front rollers and between the rear pull rollers, until the
threading card can be cut from the web at the rear of the machine.
Note: The film should be smooth and taught to the surface of the heat roller.
If the film is not tight enough, adjust the brake tension on both sides of
both top and bottom film rolls.
21. Adjusting Brake Tension
1.
To remove wrinkles in the film web, tighten the brake adjustment on each film
supply shaft using the supplied Allen wrench.
a.
Clockwise to increase brake tension.
b.
Counterclockwise to loosen brake tension.
Note: Do not over tighten the brake tension. Apply only enough tension to
the film web to smooth out wrinkleless before they enter the laminating nip
point and appear on the printed material.
Allen wrench
Adjustment screw
hole