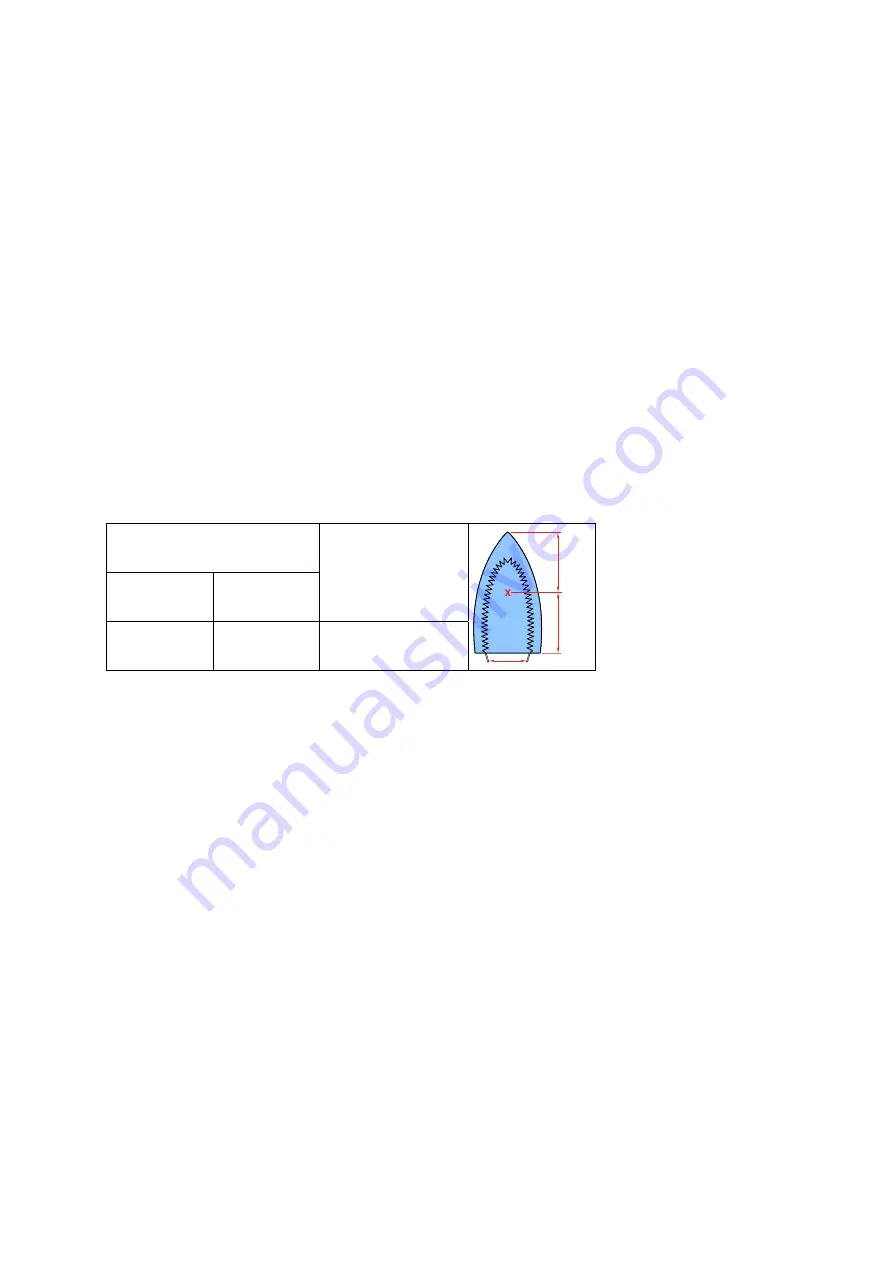
GC8635
13-13
• Due to the high wattage of the iron, only the specified cord set must be used.
• Should damage be observed on the
HOSE-CORD ASSY 14
or
CORDSET 40
, they must be replaced.
Continued usage is not allowed.
• When replacing the
MICROSWITCH ASSY 4
, please dress the 2 attached wires such that they are free of tension.
Pulling force on the wires may affect the steam triggering.
• To avoid damage to the sealing & components of the
BOILER ASSY 33
,
NEVER
clean the boiler assy with vinegar,
descaling agent or other corrosive chemicals.
• When replacing
ELECTROVALVE 28
or
PUMP ASSY 39
, please be reminded to apply loctite at the joints for good
sealing.
• After the product has been repaired, it should function properly and has to meet the safety requirements & legal regulations
as laid down & officially established at this moment.
• The following tests are common checks that are conducted on a repaired product before it is returned to the consumer.
1. Soleplate temperature
Check that soleplate temperature is within IEC requirement.
Measure the temperature of the soleplate after the iron has reached steady state i.e connected to the mains for at least
15 minutes. The table below shows the temperature requirement.
Soleplate temperature (Deg C)
Materials, for example
Test-
point
==
Minimum
Maximum
120
143
All fabric types
2. Leakage current
Check that leakage current is within IEC requirement.
Measure leakage current between LIVE/NEUTRAL & EARTH.
IEC requirement is that at 230 V supply, the EARTH leakage current must be less than 0.75 mA.
3. Water leakage / Functionality
Check that there is no water leakage from any part of the product during operation.
Check that the functionality of the product (product dependent) eg. steaming, variable steam, SOS, ASO etc is working
properly.
4. Loose part
Check that there are no loose parts eg. extra screw in the product that can cause short-circuit or product malfunction.
REPAIR INSTRUCTIONS