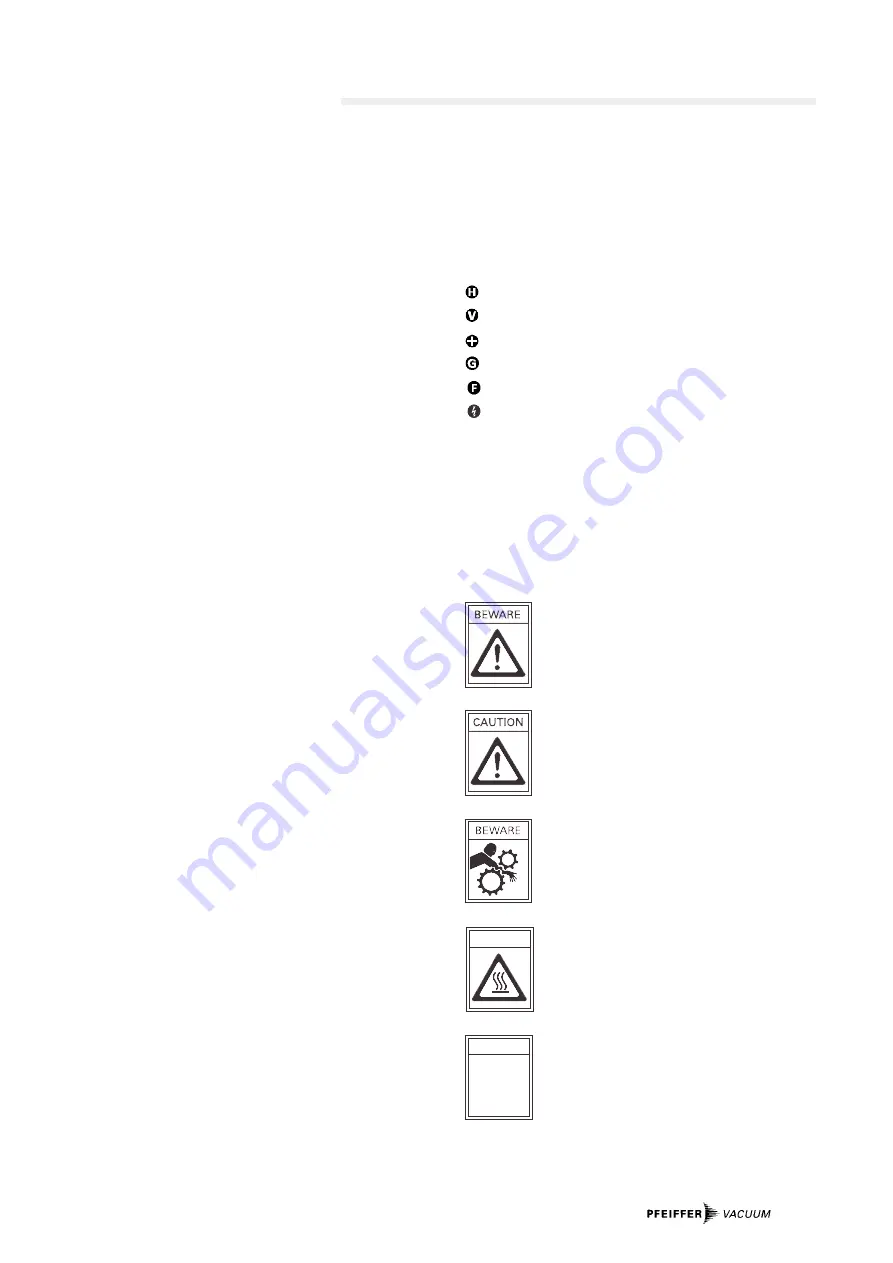
3
1. Safety Instructions
☞
Read and follow all instructions in this manual.
☞
Inform yourself regarding:
– Hazards which can be caused by the pumping station;
– Hazards which can be caused by your system;
– Hazards which can be caused by the medium being
pumped.
☞
Avoid exposing any part of the body to vacuum.
☞
Observe the safety and accident prevention regulations.
☞
Regularly check that all accident prevention measures are
being complied with.
☞
Do not operate the turbo pumping station with open high
vacuum flange.
☞
Use at least 4 bracket screws to connect the high vacuum
flange (ISO flange).
☞
Do not disconnect the plug between the TC 600 and
accessory components during operations.
☞
During operations temperatures of up to 65 °C can arise in
the lower part of the turbopump. Take care to avoid burns!
☞
Keep leads and cables well away from hot surfaces
(>70 °C).
☞
The unit has been accredited protection class IP 30. When
the unit is operated in environments which require other
protection classes, the necessary measures must be
taken.
☞
Do not carry out any unauthorised conversions or
alterations to the turbo pumping station.
☞
When returning individual components please observe the
shipping instructions (refer to the operating instructions
for the pumping station components).
Modifications reserved.
1.1. For Your Orientation
In the text
➡
Working instruction: here, you have to do something.
Symbols used
The following symbols are used throughout in illustrations.
High vacuum flange
Fore-vacuum flange
Air cooling
Sealing gas connection
Venting connection
Electric connection
Abbreviations used
DCU = Display and Operating unit
TC = Electronic drive unit, turbopump
TPS = Power unit
1.2. Pictogram Definitions
Danger of personal injury.
Danger of damage to the pumping station or to
the system.
Danger of injury from rotating parts.
Danger of burns from touching hot parts.
Attention to particulary important information
on the product, handling the product or to a
particular part of the documentation.
☞
PLEASE NOTE
BEWARE