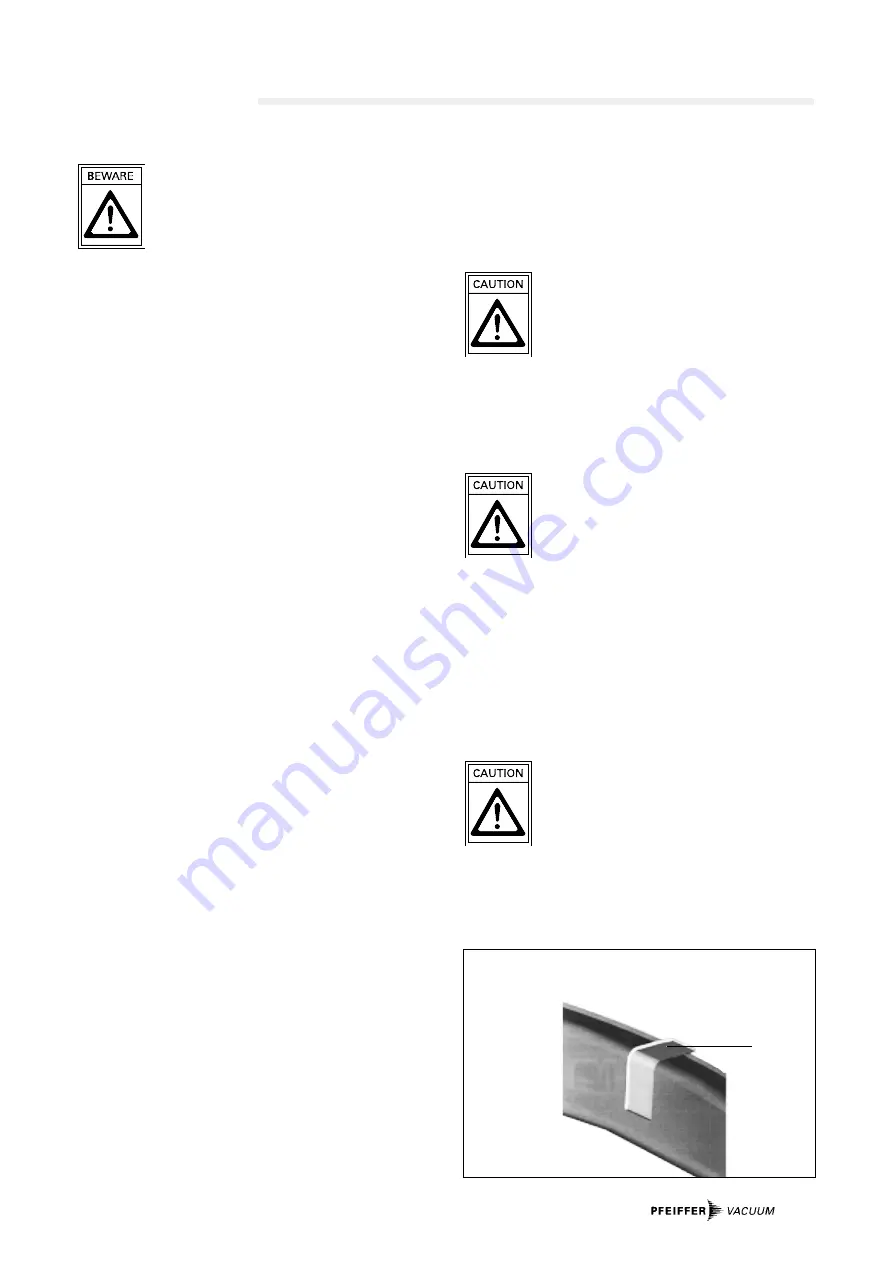
5
3. Installation
3.1. Preparations For Installation
Do not carry out any unauthorised conversions
or alterations to the turbopump.
– The maximum permissible rotor temperature of the pump is
120 °C. If the vacuum chamber or parts in the vacuum
chamber are heated, the values stated in the technical
data relating to the level of heat which may be radiated
into the pump must not be exeeded. If necessary, suitable
shielding must be fitted in the vacuum chamber before the
turbopump (constructional suggestions available on
request).
– Only remove the blank flange from the high and for-vacu-
um side immediately before connection.
– The turbopumps must
not
be transported when filled with
lubricant.
– Where magnetic fields of > 13.4 mT are involved suitable
shielding must be provided (available on request).
– If the pump is baked out, the body of the pump must be
insulated to prevent burns from accidental contact.
– Both the TPH and TPU 2201 must be anchored to the
surface.
– In the event of a sudden standstill of the rotor, torques of
up to 8960 Nm can arise and these must be taken up by the
turbopump and frame. Pumps must be anchored as
follows:
– ISO flange with 6 bracket screws,
or
– CF flange with the complete set of M8 screws,
or
– underside of the pump with 6 screws M6,
screws quality 8.8.
3.2. Installing The Pump,
Connecting The High Vacuum Side
Important
The utmost cleanliness must be observed when fitting all high
vacuum parts. Unclean components prolong the pumping
time.
Use a splinter shield
The use of a splinter shield in the high vacuum flange protec-
ts the turbopump against foreign bodies coming from the
vacuum chamber but does reduce the volume flow rate of the
pump by approximately 15%. For fitting splinter shields please
refer to “Fitting the splinter shield”.
The high vacuum side can be flanged onto the vacuum cham-
ber either directly or via a bellows or a vibration compensator
(see ”Accessories”).
Connecting via bellows
If the high vacuum side is to be flanged via a bellows, the tur-
bopump must be secured for example via the holes on the
underside of the turbopump (please see dimensions). The
fastening must be able to withstand the torque referred to in
Section 3.1.
Connecting Via A Vibration Compensator
The maximum permissible temperature at the
vibration compensator is 100 °C.
Where a vibration compensator is in use, a freely suspended
turbopump can be flanged onto the vacuum chamber.
Additional protective casing must be provided to take up the
energy of the rotor in the event of a malfunction (please
discuss this question with the manufacturer).
The maximum loading capacity of the high vacu-
um flange is 3000 N (equivalent to 300 kg).
This does not apply to pumps with flanges on the
side or below.
Asymmetric loading on the high vacuum flange
must be avoided.
If a vacuum chamber is fitted to the high vacuum flange with-
out support, it must be ensured that no torque is transmitted
to the flange (asymetrical weight of the vacuum chamber).
Even with side and under flanges, pumps can be flanged to
the vacuum chamber with a freely suspended horizontal rotor
shaft. It is a pre-condition that the vacuum chamber be firmly
anchored.
No forces from the piping system must be
allowed to act on the pump where turbopumps
are anchored.
Suspend or support all pipes to the pump.
Fitting The Splinter Shield
➡
Insert the splinter shield in the ISO-K flange in condition on
delivery.
Inserting the splinter shield in ISO-K flage
A
Strap (Condition on delivery)
A
Summary of Contents for TPH 2201
Page 11: ...11 3 12 Connections Diagram 1 1...
Page 12: ...12 Connection Diagram For 3 phase Backing Pump...
Page 23: ...23 Spare parts...