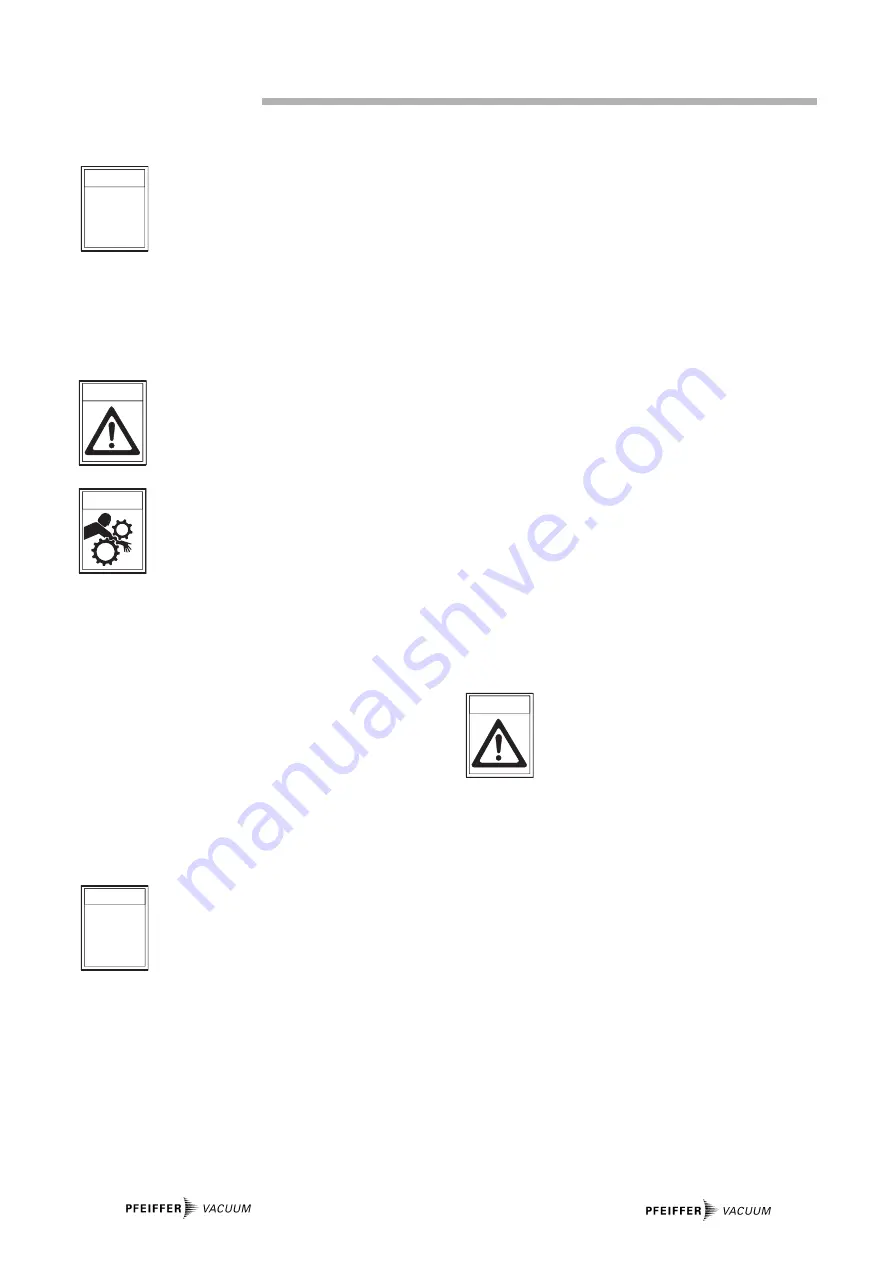
14
4.1. Before Switching On The Pump
Lubricant must be refilled in the exhaust side
bearing chamber already after 1000 operating
hours depending on the use of the pump. The
filling level is monitored and leads to switching
off the pump when falling below the minimum
mark.
➡
Check the lubricant level before starting the pump.
➡
Before switching on the pump check that all lines have
been correctly connected.
Shut-off valves in the exhaust line should be
activated so that they open either before or
simultaneously with the start of the pumps.
Pump rotors rotate at high speed. When the
high vacuum flange is open there is a
danger of injury and of damage to the pump
caused by objects falling into the pump.
Therefore never operate the pump with open
high vacuum flange!
➡
Open the cooling water supply and adjust the flow until at
least one green LED at the cooling water monitor lights up.
4.2. Switching The Pump ON
Details regarding the switching on of the pump and after a
malfunction has occurred are contained in Operating Instruc-
tions PU 0056 BN for the Electronic Drive Unit TCP2000.
➡
Switch on pump via the connecting terminal X4.14
➡
Bring pump to operating temperature before process start
(approx. 10 min) to prevent condensation.
When switching on for the first time or after a
change of lubricant, the contacts for monitoring
the lubricating pump can open as a result of
degassification. In such cases, as for other
malfunctions, the electronic drive unit switches
off the pump.
☞
PLEASE NOTE
WARNING
CAUTION
☞
HINWEIS
4. Operations
4.2.1 Motor Temperature Monitoring
An automatic temperature control controls the following
units:
Motor temperature
For motor temperature monitoring there are two limiting
values:
−
W
Waarrnniinngg::
A motor temperature > 75°C results in a lowering the motor
in order to avoid an overheating of the motor.
−
EErrrroorr::
A motor temperature > 85°C --> results in switching off the
pump and an error message (E.EF) is displayed at the
display and control unit at the TCP.
4.3. Gas Type Dependent Operations
Where high level gas loads and rotation speeds are involved,
the resulting friction subjects the rotor to the effect of great
heat. To avoid over-heating, a power rotation speed charac-
teristic line is implemented in the TCP 2000; this ensures that
where maximum gas loads are involved, the pump will ope-
rate at any rotation speed without the danger of damage
arising. The maximum power is dependent on the type of gas
and consider only nitrogen, respectively air and lighter gases.
Max. permissible gas loads:
−
Molecular mass < 40 (e.g. Argon)
≤
1000 sccm
−
Molecular mass > 40 in exceptional cases with gas ballast.
Pumping gases with molecular mass
≥
40 can
cause damage to the pump. Before pumping
such gas types please contact the
manufacturer.
WARNING
Summary of Contents for OnTool Booster 150
Page 22: ...22...