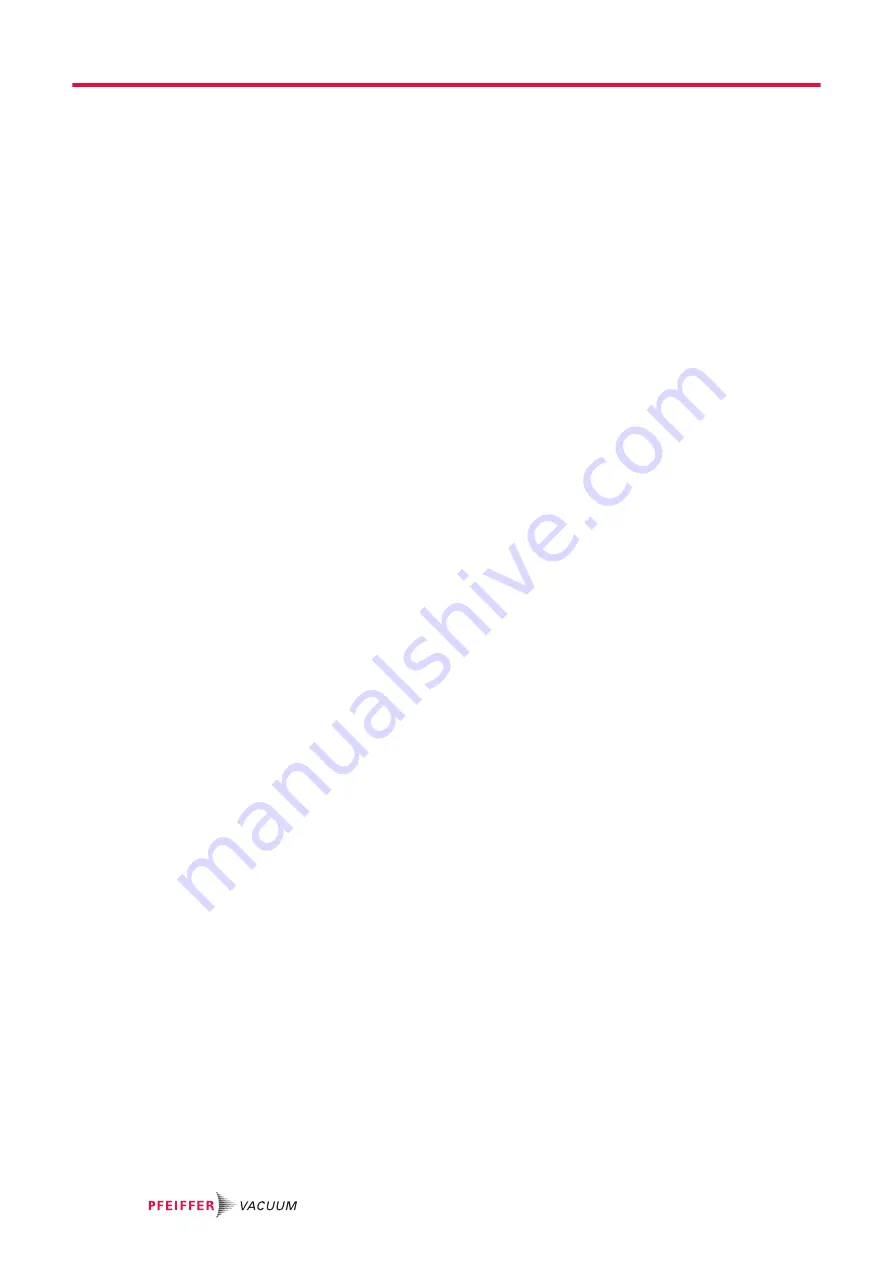
6.6.1 Condition monitoring of the vacuum pump
6.6.2 Monitoring the bearing condition
6.6.3 Monitoring the motor condition
6.7
Switching off and venting the vacuum pump
7
7.1
7.2
Checklist for inspection and maintenance
7.3
7.4
7.5
8
8.1
Shutting down for longer periods
8.2
8.3
9
10
Service solutions from Pfeiffer Vacuum
11
11.1 Ordering spare parts packs
12
12.2 Ordering accessories
13
13.1 General
13.2 Technical data
13.3 Dimensions
Table of contents
4/60