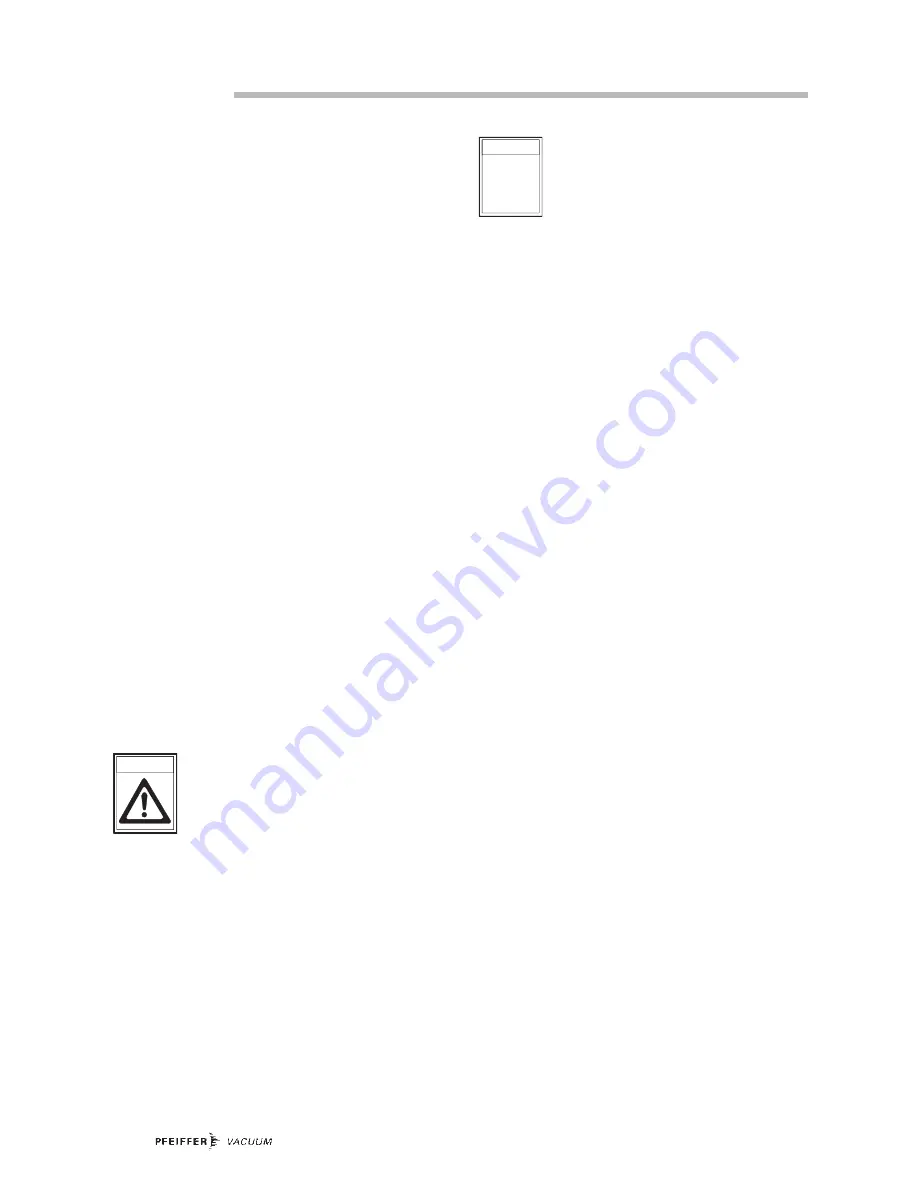
10
7. Service
Repair orders are carried out according to our
general conditions of sale and supply.
➡
If repairs are necessary, please send the unit together
with a short damage description to your nearest Pfeiffer
Vacuum Service Center.
☞
PLEASE NOTE
Do Make Use Of Our Service Facilities
In the event that repairs are necessary to your pumping
station, a number of options are available to you to ensure
any system down time is kept to a minimum:
– Have the pump repaired on the spot by our Pfeiffer
Vacuum Service Engineers;
– Return the individual components to the manufacturer for
repairs;
– Replace individual components with a new value
exchange units.
Local Pfeiffer Vacuum representatives can provide full
details.
Before Returning:
➡
Dismantle all accessories.
➡
Attach a clearly visible notice: “Free of contamination” (to
the unit being returned, the delivery note and accompany-
ing paperwork).
Harmful substances" are substances and preparations as
defined in current legislation. Pfeiffer Vacuum will carry out
the decontamination and invoice this work to you if you have
not attached this note. This also applies where the operator
does not have the facilities to carry out the decontamination
work. Units which are contaminated microbiologically, explo-
sively or radioactively cannot be accepted as a matter of
principle.
Fill Out The Contamination Declaration
➡
In every case the "Contamination Declaration" must be
completed diligently and truthfully.
➡
A copy of the completed declaration must accompany the
unit; any additional copies must be sent to your local
Pfeiffer Vacuum Service Center.
Please get in touch with your local Pfeiffer Vacuum represen-
tatives if there are any questions regarding contamination.
Decontaminate units before returning or
possible disposal. Do not return any units which
are microbiologically, explosively or radio-
actively contaminated.
Returning Contaminated Units
If contaminated units have to be returned for
maintenance/repair, the following instructions concerning
shipping must be followed without fail:
➡
Neutralise the pump by flushing with nitrogen or dry air.
➡
Seal all openings to the air.
➡
Seal pump or unit in suitable protective foil.
➡
Ship units only in appropriate transport containers.
WARNING