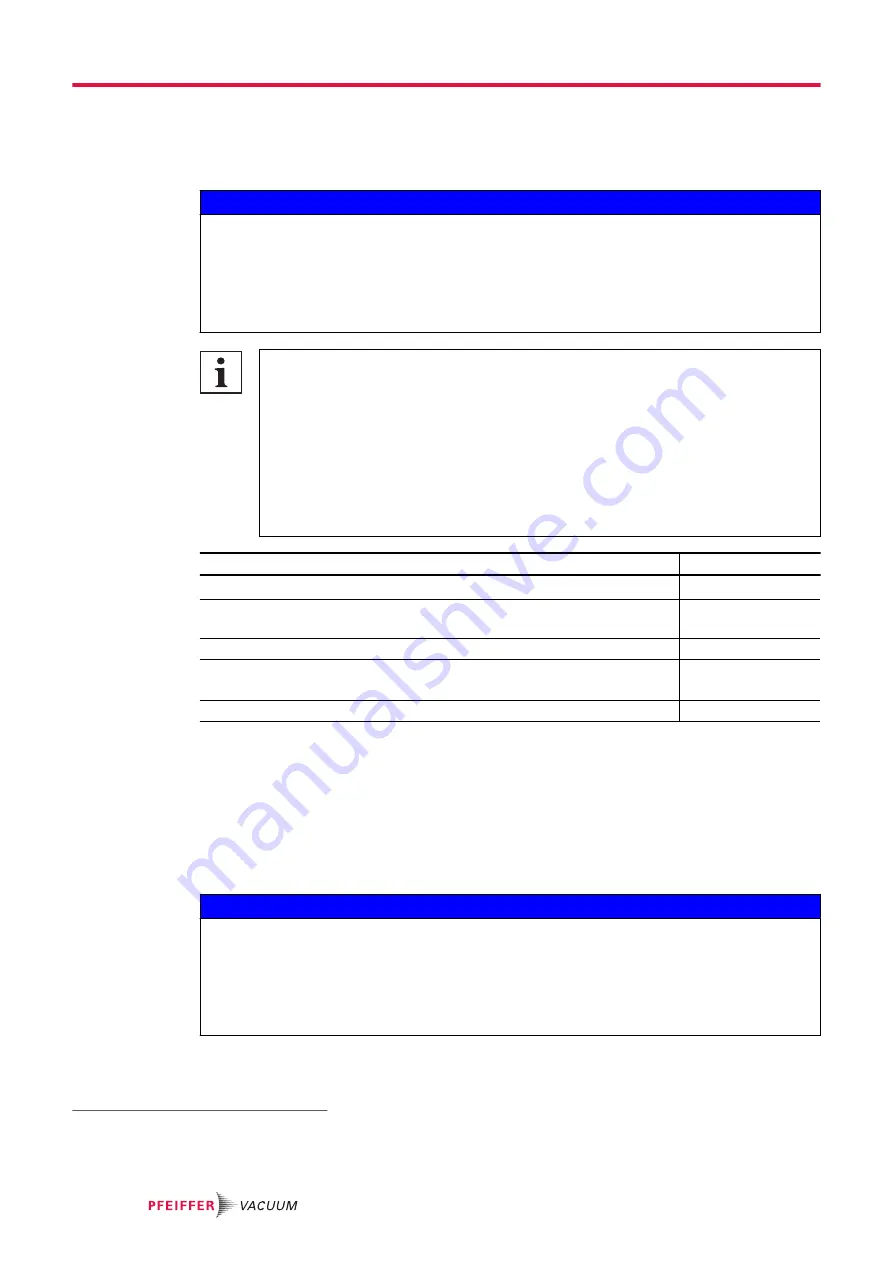
5.2 Connecting the high vacuum side
5.2.1 Requirements for the dimensioning of a counter flange
NOTICE
Risk of damage due to incorrect counter flange design
Unevenness on the operator-side counter flange results in stresses in the vacuum pump housing,
even when properly attached. This can produce leakage or negative changes in running characteris-
tics.
► Adhere to the shape tolerances for the counter flange.
► Observe the maximum flatness deviations over the entire surface.
Superstructural parts and fittings on the high vacuum connection
Installing superstructural parts and fittings to the high vacuum connection is the responsibil-
ity of the operating company. The loading capacity of the high vacuum flange is specific for
the turbopump used.
● The total weight of superstructural parts must not exceed the maximum axial values
specified.
● Make sure that all the torques generated if the rotor blocks suddenly, are absorbed by
the system on the operator side and the high vacuum connection.
● Only use the approved mounting kits of Pfeiffer Vacuum for the high vacuum connec-
tion of the turbopump.
Parameter
HiPace 80 Neo
Maximum torque occurring in the event of a burst
1)
620 Nm
Maximum permissible axial load on the high vacuum flange
2)
200 N
(equivalent to 20 kg)
Flatness
± 0.05 mm
Minimum tensile strength of the flange material in all operating states in rela-
tion to the engagement depth of the fixing screws
170 N/mm
2
at 2.5 x d
270 N/mm
2
at 1.5 x d
Maximum permissible rotor temperature
90
℃
Tbl. 6:
Requirements for the dimensioning of high vacuum connection supplied by the cus-
tomer
Important information for correct installation
► Only use the approved mounting kits of Pfeiffer Vacuum for the high vacuum connection of the
turbopump.
5.2.2 Consider earthquake protection
NOTICE
Vacuum pump damage caused by external vibrations
In the event of earthquakes or other external vibrations, there is the risk of the rotor coming into con-
tact with the safety bearings, or the housing wall touching the turbopump. This can produce mechani-
cal loads up to and including destruction of the turbopump.
► Make sure that all flange and safety connections absorb the resulting forces.
► Secure the vacuum chamber against displacement or tipping.
1)
The theoretically calculated torque in the event of a burst (rotor shaft breakage) according to ISO 27892 was
not reached in any experimental test.
2)
A one-sided load is not permitted.
Installation
22/58