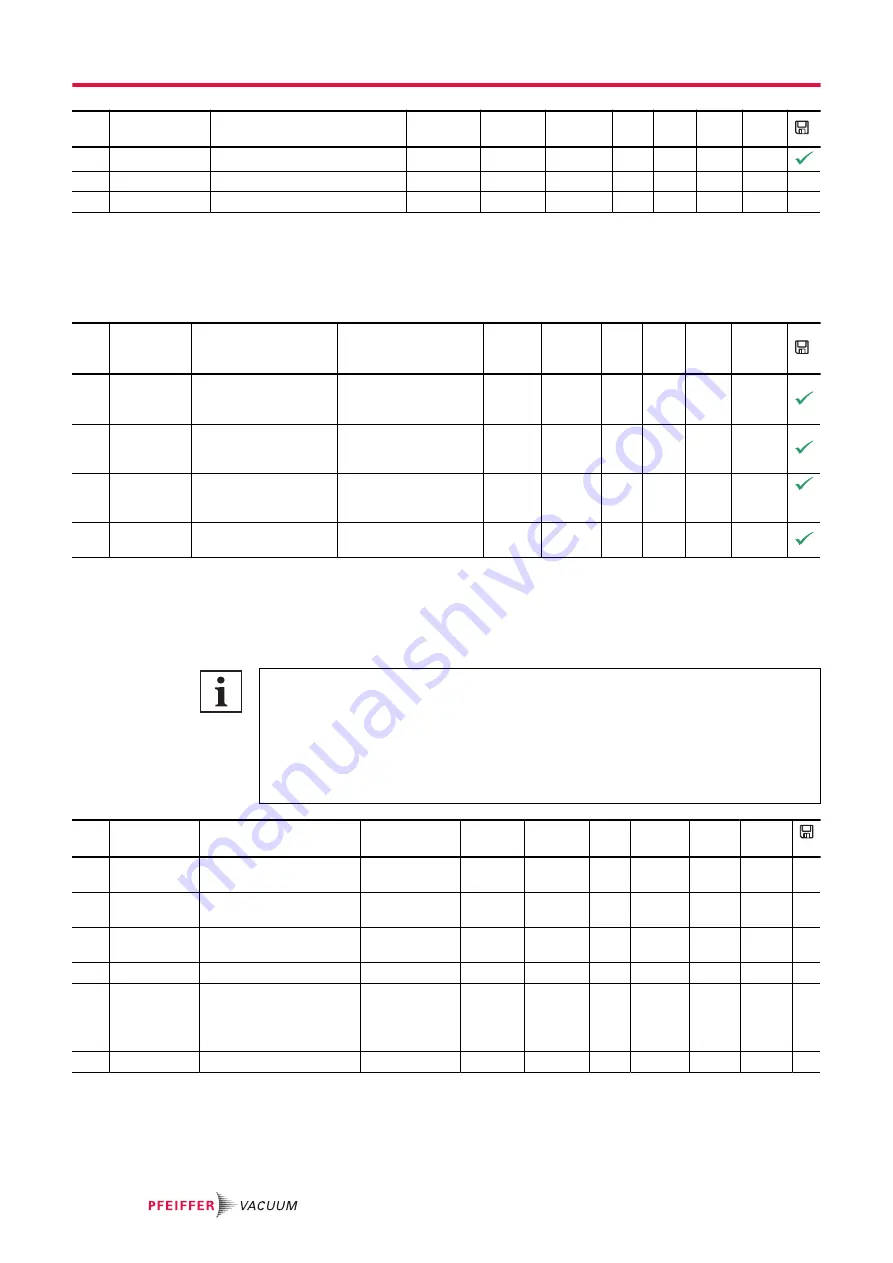
#
Display
Designations
Func-
tions
Data
type
Access
type
Unit min. max. de-
fault
364 ErrHist5
Error code history, item 5
4
R
398 ActualSpd
Actual speed (rpm)
1
R
rpm
399 NominalSpd
Nominal rotation speed (rpm)
1
R
rpm
Tbl. 10:
Parameter set | Status requests
7.4 Reference value inputs
#
Display
Designations
Functions
Data
type
Ac-
cess
type
Unit min. max. de-
fault
706 DefaultSpd Specification in nor-
mal operation
Rotation speed as a
% of the nominal
speed
2
RW
%
25
100
100
707 SpdSVal
Setpoint in speed-
control operation
Set rotation speed as
% of nominal rotation
speed
2
RW
%
25
100
75
717 StdbySVal
Specification in
stand-by operation
Rotation speed as a
% of the nominal
speed
2
RW
%
25
100
30
797 RS485Adr
RS-485 Interface ad-
dress
1
RW
1
255
1
Tbl. 11:
Parameter set | Reference value inputs
7.5 Additional parameter for the DCU
Additional parameter in the control panel
The basic parameter set is set in the electronic drive unit ex-factory. For controlling con-
nected external components (e.g. vacuum measuring instruments), additional parameters
(extended parameter set) are available in the corresponding Pfeiffer Vacuum display and
control panels.
● Refer to the corresponding operating instructions of the respective components.
● Select the extended parameter set with parameter
[P:794]
= 1.
#
Display
Description
Functions
Data
type
Access
type
Unit min.
max.
de-
fault
340 Pressure
Actual pressure value
(ActiveLine)
7
R
hPa
1·10
-10
1·10
3
350 Ctr Name
Display and control
panel: type
4
R
351 Ctr Software Display and control
panel: software version
4
R
738 Gauge type
Type of pressure gauge
4
RW
794 Param set
Parameter set
0 = Basic pa-
rameter set
1 = Extended
parameter set
7
RW
0
1
0
795 Servicelin
Insert service line
7
RW
795
Tbl. 12:
Parameter for DCU functions
Parameter set
38/66
Summary of Contents for HILOBE 1004
Page 1: ...OPERATING INSTRUCTIONS EN Translation of the Original HILOBE 1004 1304 2104 Roots pump...
Page 65: ...65 66...
Page 66: ...Notizen Notes...
Page 67: ......