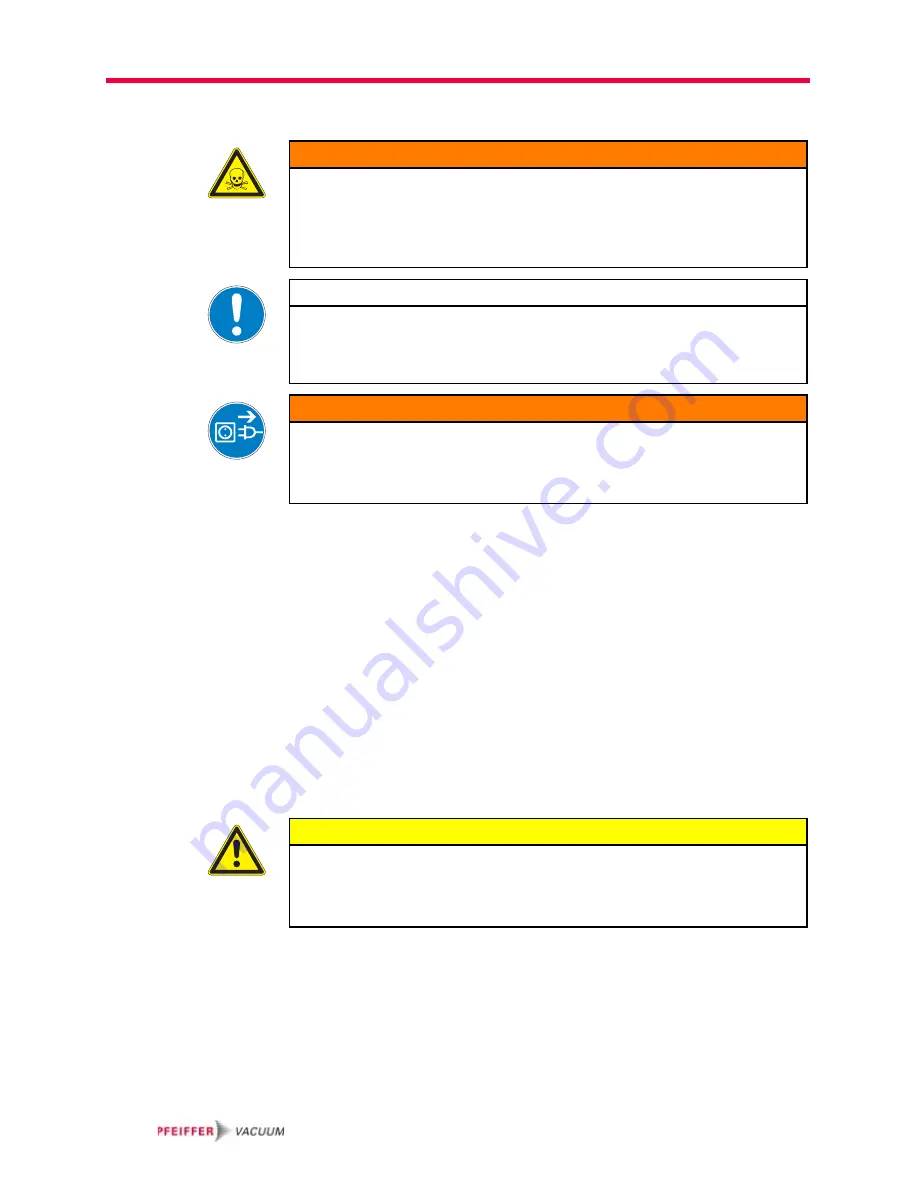
16
Maintenance / replacement
7
Maintenance / replacement
7.1
Maintenance intervals and responsibilities
• Clean the pumping station externally with a lint-free cloth and little industrial al-
cohol.
• Carry out the required maintenance on the components of the pumping station
in accordance with the instructions in the individual operating manuals.
• Clarify shorter change intervals for extreme loads or impure processes with
Pfeiffer Vacuum Service.
• For all other cleaning, maintenance or repair work, please contact your Pfeiffer
Vacuum service location.
7.2
Removal of components for their maintenance
In some cases, components may need to be dismantled from the pumping station
so that customers can carry out necessary maintenance work on them (they should
then be reassembled in reverse order).
Dismantling connec-
tions
Switch off the pumping station at the master switch.
Disconnect the mains plug.
Pull out the mains cable from the relay box.
Pull out the mains supply cable (x2) for components from the relay box.
Take off the connector from the electronic drive unit TC 110.
Detach the accessory control lines from the connector and remove them.
WARNING
Contamination of parts and operating fluid by pumped media is possible.
Poisoning hazard through contact with materials that damage health.
In the case of contamination, carry out appropriate safety precautions in order to pre-
vent danger to health through dangerous substances.
Decontaminate affected parts before carrying out maintenance work.
NOTE
Disclaimer of liability
Pfeiffer Vacuum accepts no liability for personal injury or material damage, losses or
operating malfunctions due to improperly performed maintenance. The liability and
warranty entitlement expires.
WARNING
Risk of electric shock
The pumping station is only free of voltages when the mains plug has been disconnec-
ted.
Switch off the master switch and disconnect the mains plug before all work.
CAUTION
Refer to the notes on Proper Use of the unit.
The pumping station must only be operated as a complete unit. Disassembly and ope-
ration of individual pumping station components is deemed to be improper use.
• In this case the declaration of conformity will become invalid.