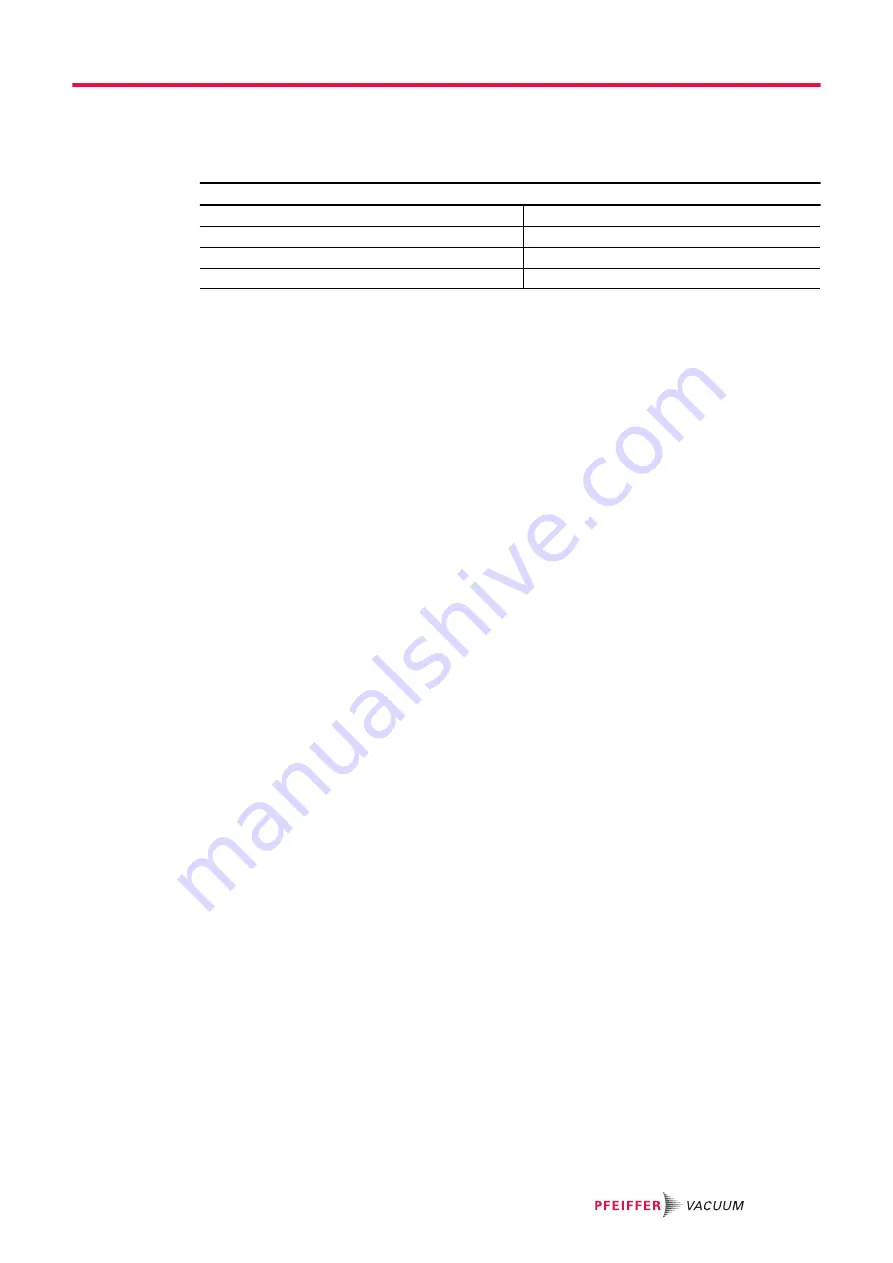
Procedure
► Connect the thermal circuit breaker such that an alarm is triggered and the vacuum pump shuts
down if the operating temperature exceeds 106 °C.
Temperature switch
Voltage supply [U]
6 – 30 VDC
Current consumption [I]
10 – 100 mA
Contact
Normally closed (NC)
Switch-point
T= 106 °C
Tbl. 12:
Technical data
Installation
37/70