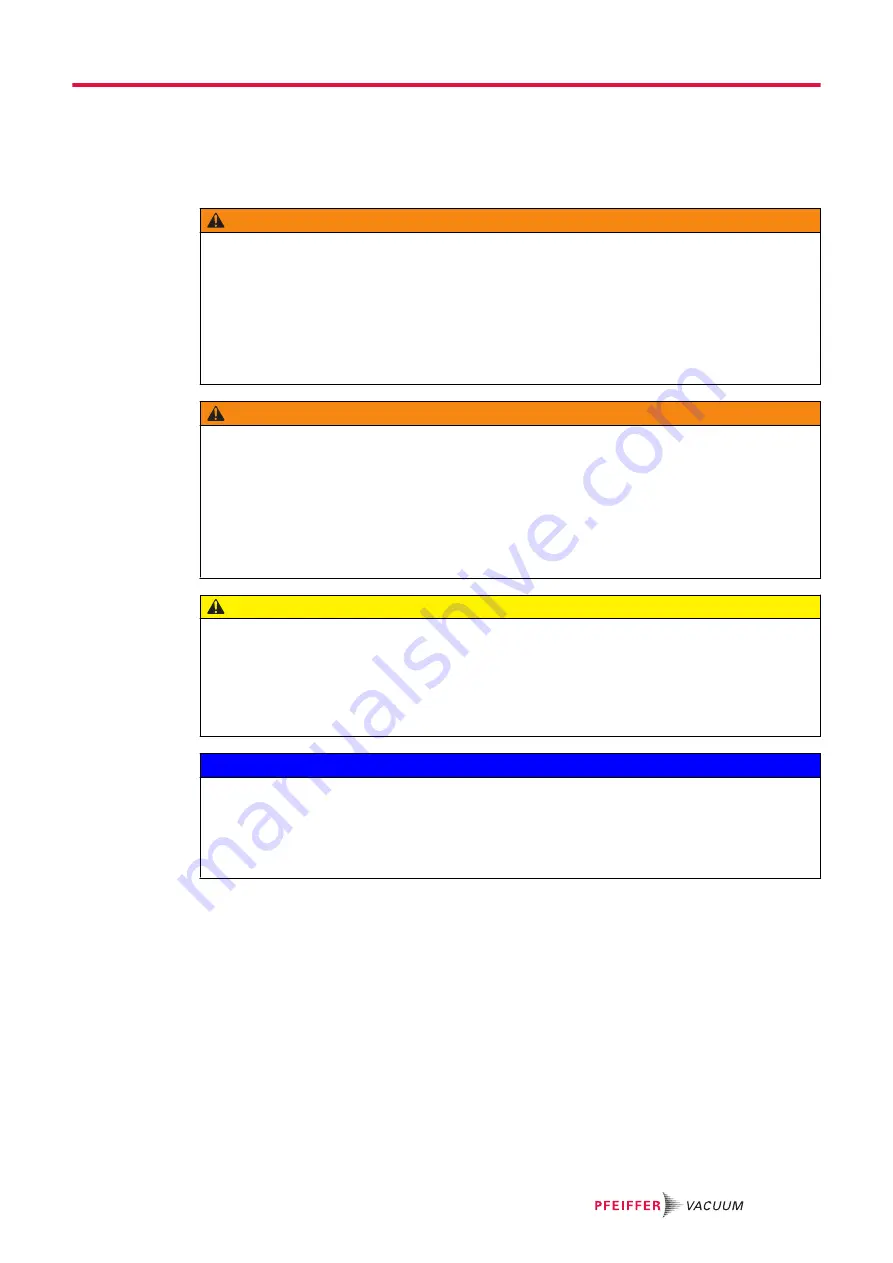
8 Maintenance
8.1 Maintenance instructions
WARNING
Health hazard through poisoning from toxic contaminated components or devices
Toxic process media result in contamination of devices or parts of them. During maintenance work,
there is a risk to health from contact with these poisonous substances. Illegal disposal of toxic sub-
stances causes environmental damage.
► Take suitable safety precautions and prevent health hazards or environmental pollution by toxic
process media.
► Decontaminate affected parts before carrying out maintenance work.
► Wear protective equipment.
WARNING
Tilting danger! Serious injury due to tilting of the product
There is a danger of the vacuum pump not attached tipping over due to changes in the center of
gravity or incorrect loading. Serious injuries due to trapping or crushing of limbs, e.g. feet, are the re-
sult.
► Do not use the vacuum pump as a climbing aid.
► Do not exert any force on the product.
► Ensure that the product has a safe centre of gravity, when mounting components.
► Wear protective equipment , e.g. protective shoes
CAUTION
Danger of injury from moving parts
After a power failure or a standstill as a result of overheating, the motor restarts automatically. There
is a risk of injury to fingers and hands if they enter the operating range of rotating parts.
► Safely disconnect motor from the mains.
► Secure the motor against reactivation.
► Dismantle the vacuum pump for inspection, away from the system if necessary.
NOTICE
Danger of property damage from improper maintenance
Unprofessional work on the vacuum pump will lead to damage for which Pfeiffer Vacuum accepts no
liability.
► We recommend taking advantage of our service training offering.
► When ordering spare parts, specify the information on the nameplate.
The following section describes the tasks for cleaning and maintaining the vacuum pump. More ad-
vanced works are described in the service instructions.
Prerequisites
● Vacuum pump switched off
● Vacuum pump vented to atmospheric pressure
● Vacuum pump cooled
Preparing maintenance
► Safely disconnect the drive motor from the mains.
► Secure the motor against switching back on.
► For maintenance work, only dismantle the vacuum pump to the extend needed.
► Dispose of used operating fluid according to applicable regulations in each case.
► When using synthetic operating fluid, please observe the associated application instructions.
► Only clean the pump parts using industrial alcohol, isopropanol or similar media.
Maintenance
33/52