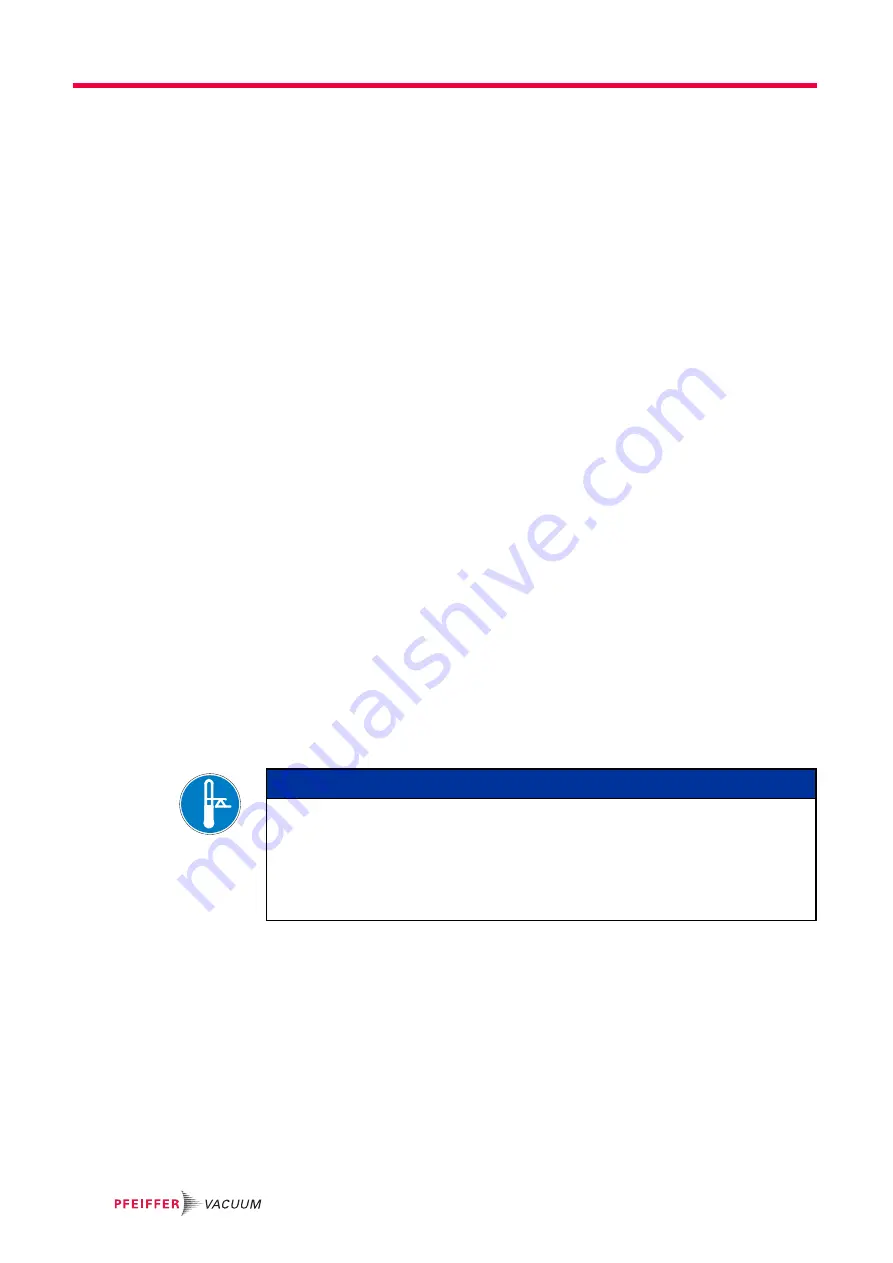
18
Operation
6
Operation
6.1 Recommendations for the operator
●
The service personnel must be advised in regular training courses on the necessity
for wearing the personal protective equipment. Working without protective equipment
can lead to serious and also lasting health damages.
●
The operator advises in recurring training courses the operating, maintenance, and
service personnel in the correct behaviors while handling the pumping station. He ex-
plains that damages to persons and systems can occur, if the pumping station is not
operated correctly. To this in particular belong also information concerning the residual
risks.
●
Before maintenance and repairs the pumping station is shut down. The main switch,
provided by the operator, is switched off by the operational, technically responsible su-
pervisor and secured against restarting with a lock. The key is taken off and carried.
●
After completion of the work and before restarting, the responsible supervisor makes
sure, that this is possible without endangerment of persons or equipment. Before
switching on a well-timed and clear warning must be given to all involved persons.
6.2 Before switching on
The instructions also apply for each time the pumping station is restarted after shutting
down for storage, maintenance or inspection.
Check operating fluid and lubricant levels of the pumps and refill if necessary.
Check sealing oil chamber on Roots pump (oiler).
Check that all lines are properly connected.
Check process-specific and pump-specific media supplies.
Verify direction of rotation of pumps as described in the operating manuals for the in-
dividual components.
Operate shut-off units in the exhaust line in such a way that they open before or at the
same time as starting the pump.
6.3 Switching on the pumping station
The pumping station can be switched on using a common switch contact for the backing
pump and the Roots pump or with separate switches in accordance to the process re-
quirements.
For pumping stations with a control cabinet, the switch-on sequence is specified by the
controller. Switch on the master switch on the control cabinet.
Switch on pumping station.
When water cooling is used: Open cooling water supply and check the flow.
Open shut-off valve in the intake line and switch the pump over to the process.
When sealing gas is used: Open the sealing gas supply and check the flow.
NOTICE
Danger of corrosion from condensation in the pumps!
The operating fluid / lubricant can become contaminated by mist during evacuation, de-
grading the properties of the oil.
Bring pumping station to operating temperature before process start.
After completion of the process, let the pumping station continue to run for about 30
minutes with the intake line closed and the gas ballast valve open.