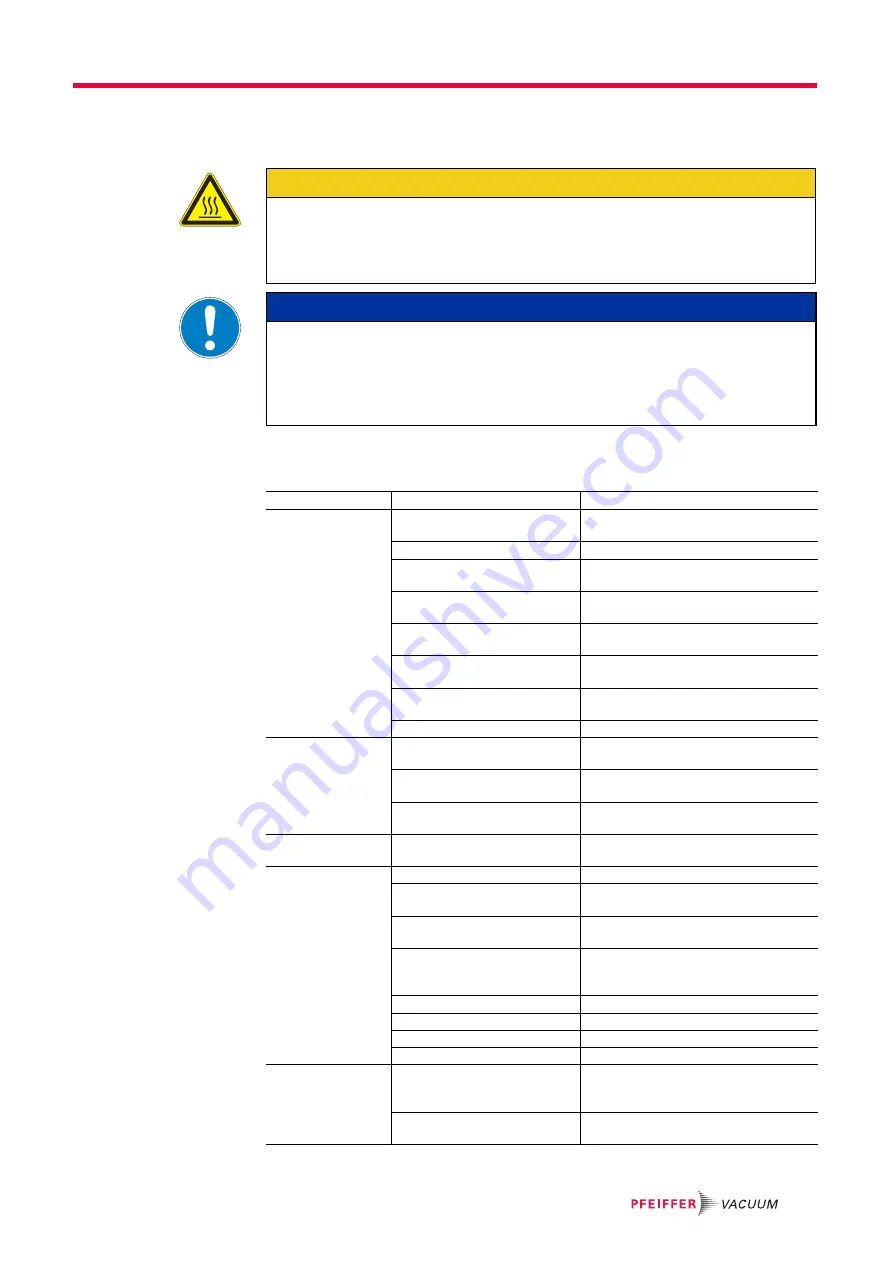
Malfunctions
37
9
Malfunctions
Please note the following instructions should the pump malfunction:
9.1
Rectifying malfunctions
CAUTION
Hot surface!
Danger of burns if hot parts are touched. The surface temperature of the pump may rise
above 105 °C in case of malfunction.
Carry out work on the pump only after it has cooled to a safe temperature.
NOTICE
Motor overload!
Depending on the malfunction (e.g. blocking during cold start), the motor may not be
sufficiently protected by the built-in thermal protection switch from damage through
overheating.
Implement an additional network safety device.
Problem
Possible causes
Remedy
Pump will not start up No mains voltage or voltage does
not correspond to the motor data
Check mains voltage and mains fuse protec-
tion; check motor switch
Ambient temperature too low
Warm up pump to > 12 °C
Suction chamber not flooded
Flood on suction side after switching off
pump
Thermal cut-off switch has re-
sponded
Detect and fix cause of overheating; allow
pump to cool off if necessary.
Defective motor cut-off switch
(building side)
Re-set or replace switch.
Dirty pump system
Clean pump; notify Pfeiffer Vacuum service
department, if necessary.
Damaged pump system
Clean and overhaul pump; notify Pfeiffer
Vacuum service department, if necessary.
Motor defective
Replace motor
Pump switches off af-
ter a while after being
started
Thermal protection switch of the
motor has responded
Detect and fix cause of overheating; allow
pump to cool off if necessary.
Mains fuse protection triggered
due to overload (e.g. cold start)
Warm up pump
Exhaust pressure too high
Check opening of exhaust line and exhaust
accessories
High increase in oper-
ating temperature
Fault in cooling water circuit
Check flow paths for dirt and lime deposits;
clean, if necessary.
Pump not achieving
the ultimate pressure
Leak in the system
Fix leak
Falsified measuring result
Check gauge, test ultimate pressure without
connected system.
Pump or connected accessories
dirty
Clean pump and check components for dirt.
Dirt in operating fluids
Operate pump for a longer period of time
with opened gas ballast valve or replace op-
erating fluids
Gas ballast valve is open
Close valve.
Silencer is open
Set/adjust the silencer
Operating fluids fill level too low
Fill up operating fluids
Pump is damaged
Contact Pfeiffer Vacuum Service.
Pumping speed of
pump too low
Intake line not well-dimensioned
Keep connections as short as possible and
see that cross-sections are sufficiently di-
mensioned
Exhaust pressure too high
Check opening of exhaust line and exhaust
accessories