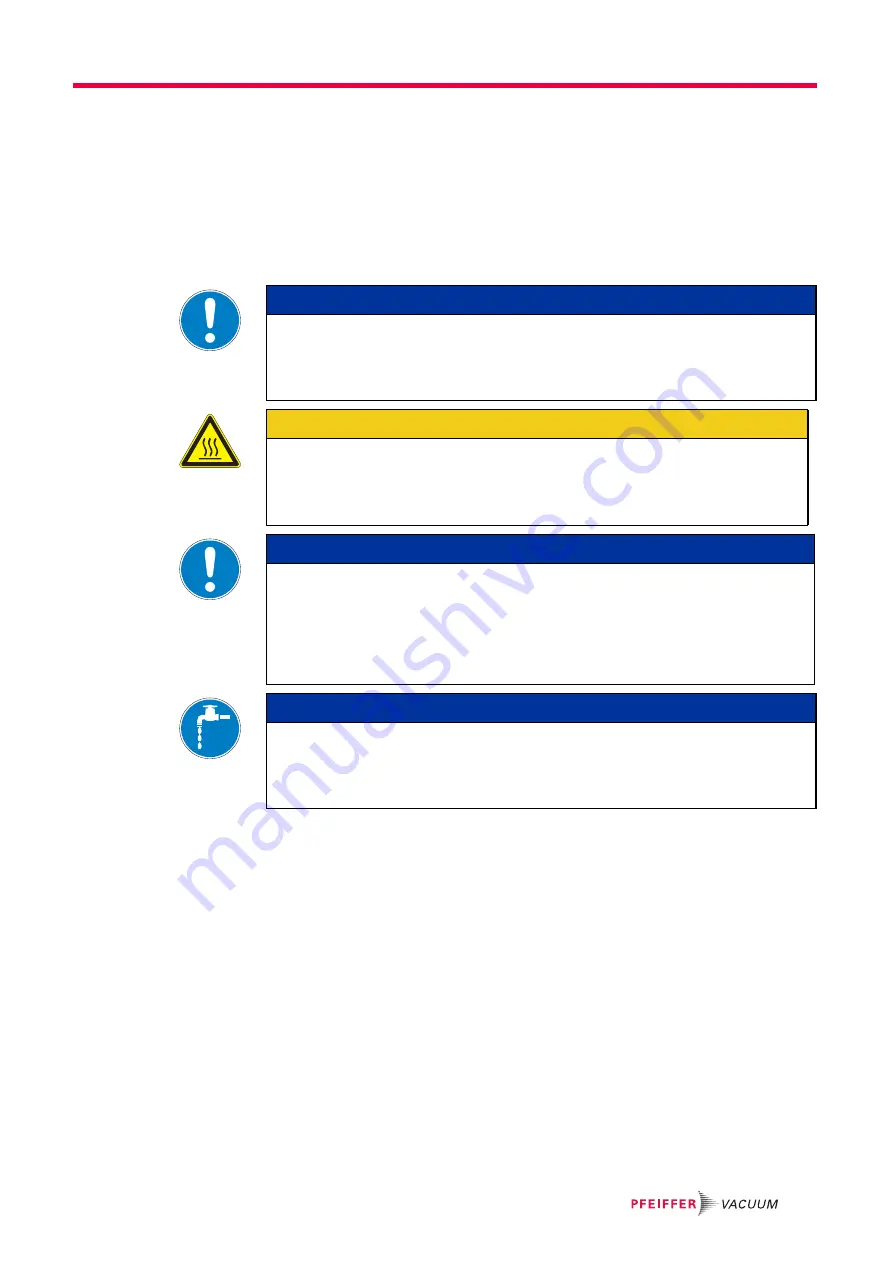
Operation
23
6.2
Switching on the pump
The pump can be switched on in any pressure range between atmospheric and
ultimate pressure.
The ideal operating condition of the pump is achieved during continuous operation. Cy-
clic operation is possible, but 10 cycles per hour should not be exceeded and the oper-
ating phase should always be longer than the downtime (non-operation time).
No special precautions are necessary when pumping dry gases. In order to attain the
lowest possible ultimate pressures, the gas ballast valve should be closed.
Switch on the pump with the vacuum flange closed and allow to warm up for 15 min-
utes.
Check operating fluid level only when the pump is warm and running; therefore
– close vacuum flange and gas ballast valve,
– correct filling level during operations: within the markings at the sight glass frame,
– check operating fluid daily in non-stop operation, otherwise whenever the pump is
switched on. Refilling is possible when the pump is in final vacuum operation.
Setting cooling water
The cooling water controller 41 is a continuously operating control valve that is controlled
by the temperature-dependent cooling agent. The thermal sensor is submerged in the
operating fluid and connected via a capillary tube to the bellows in the valve head. The
cooling water controller 41 is factory-set. If other temperatures are required, the pump
temperature can be changed by turning setting disk 1. The respective settings, as well
as the maximum temperature, must only be made after consulting with Pfeiffer Vacuum.
NOTICE
V-belts are used as an overload protection
Upon activation of the motor, brief slippage can occur; this is perceived as a whistling
sound.
This is not a sign of insufficient belt tension!
CAUTION
Hot surface!
Danger of burns if hot parts are touched. Depending on the operating and ambient con-
ditions, the surface temperature of the pump may rise above 70 °C.
In this case, use suitable finger guards.
NOTICE
Increased motor current draw (> rated current) !
With an intake pressure of about 300 h/Pa, the pump has the highest power require-
ment, which can increase even further under unfavorable operating conditions (e.g.
counter-pressure on exhaust side.
Limit the max. power consumption for 1.5 times the rated current for 2 minutes max.
(according to DIN EN 60034-1.
NOTICE
Pump damage caused by overheating!
Inadequate cooling may cause pump damage.
Vent the cooling chambers and ensure a water flow prior to commissioning or subse-
quently switching on the pump!