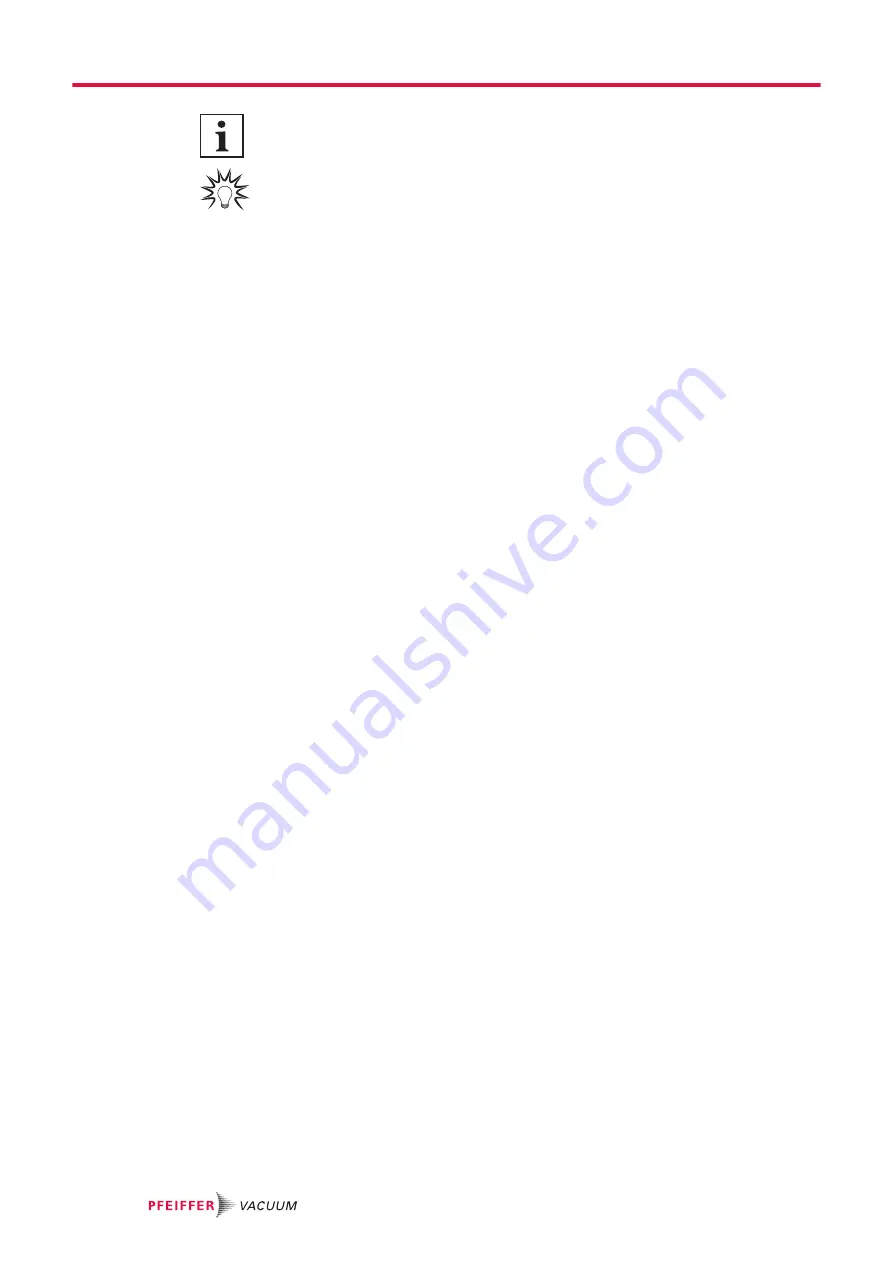
Note
Tip
1.3.3 Abbreviations
Exh.
Exhaust
IN
Inlet flange
OME
Oil Mist Eliminator
1.3.4 Trademark proof
● Axarel
®
is a trademark of DuPont de Nemours and Company, Wilmington, Delaware, USA..
● CareClean
®
is a trademark of Castrol Ltd.
● PremaClean
®
is a trademark of Lenntech BV
● Naphtesol
®
is a trademark of Nippon Oil Corporation
About this manual
6/22