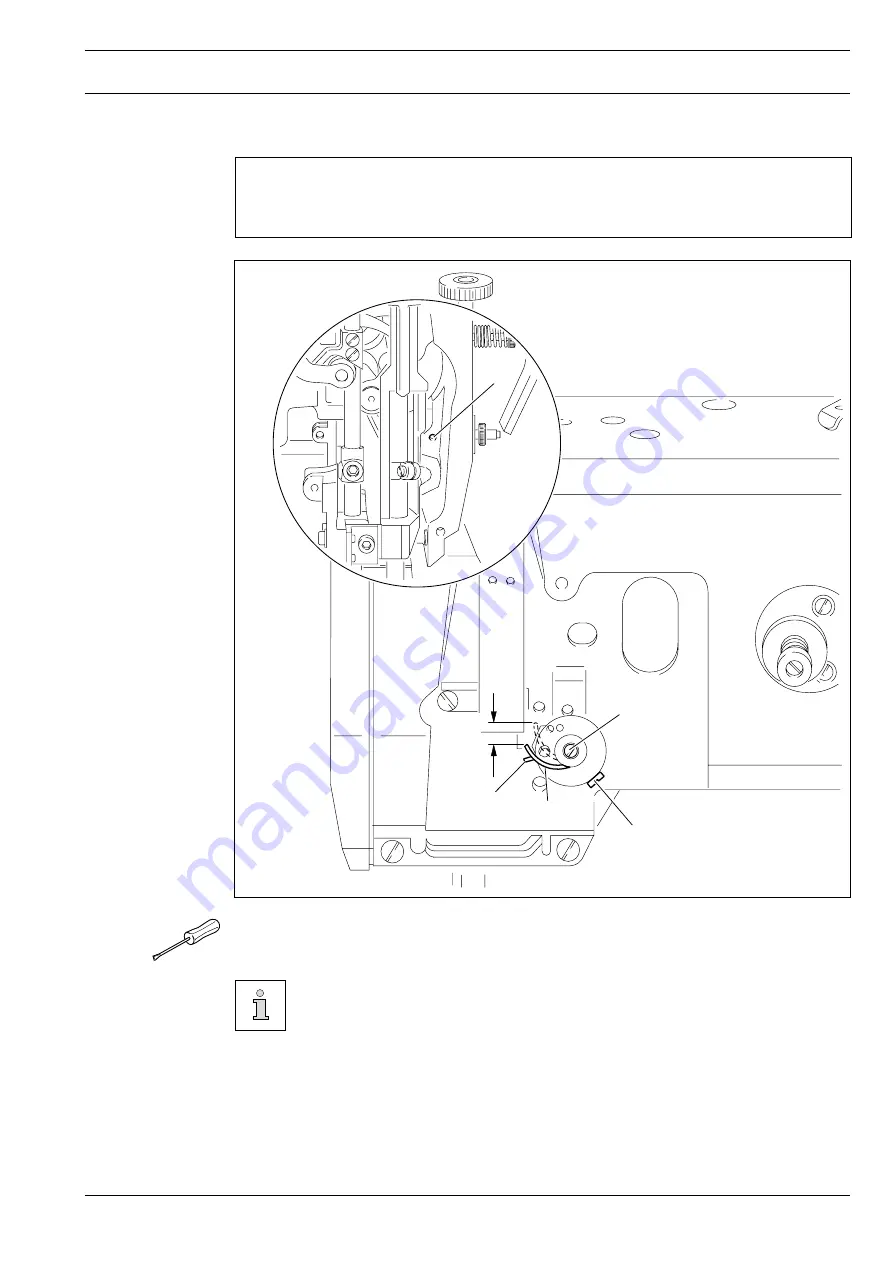
11 - 12
Adjustment
11
.04.10
Thread check spring
Requirement
The movement of thread check spring
5
must be finished when the needle point enters
the material (=
=
=
=
=
spring stroke of about 7 mm
).
Fig. 11 - 10
●
Adjust stop
1
(screw
2
) according to
Requirement
.
●
To adjust the pressure of the spring, turn screw
3
(screw
4
).
For technical reasons the length of the thread check spring stroke may vary
upwards or downwards a little.
1
2
3
7 mm
5
4