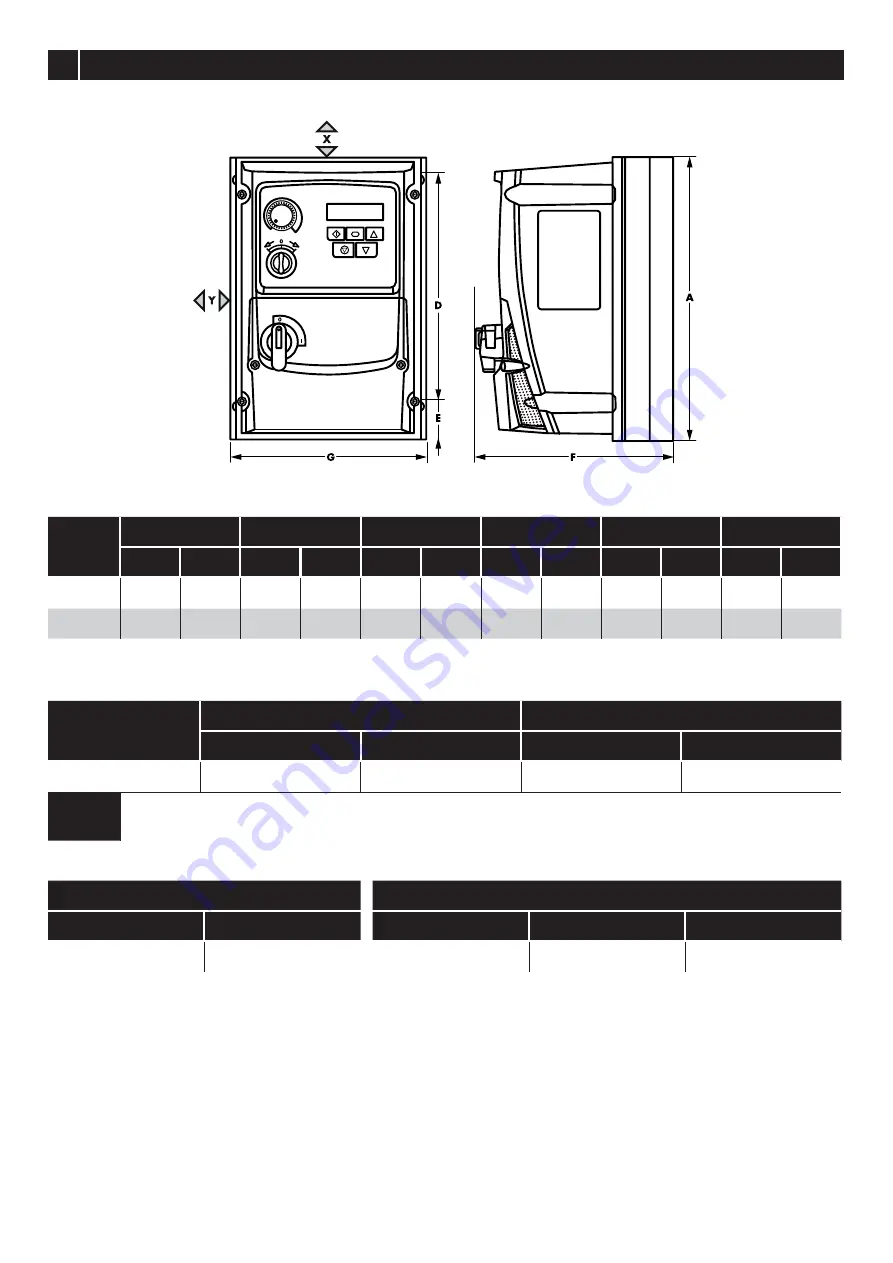
3 MOUNT
Mechanical Dimensions
Dimensions
Frame
Size
A
B
C
D
E
Weight
mm
in
mm
in
mm
in
mm
in
mm
in
kg
Ib
1
232
9,13
161
6,34
162
6,37
189
7,44
148,5
5,85
2,5
5,5
2
257
10,12
188
7,4
182
7,16
200
7,87
176
6,93
3,5
7,7
Mounting Clearance
Drive Size
X Above & Below
Y Either Side
mm
in
mm
in
All Frame Sizes
200
7.87
10
0.39
NOTE
Typical drive heat losses are approximately 3% of operating load conditions. Above are guidelines only
and the operating ambient temperature of the drive MUST be maintained at all times.
Mounting Bolts & Tightening Torques
Mounting Bolts
Tightening Torques
Frame Size
Frame Size
Control Terminals
Power Terminals
All Frame Sizes
4 x M4 (#8)
All Frame Sizes
0.8 Nm (7 lb-in)
1.5 Nm (13 lb-in)