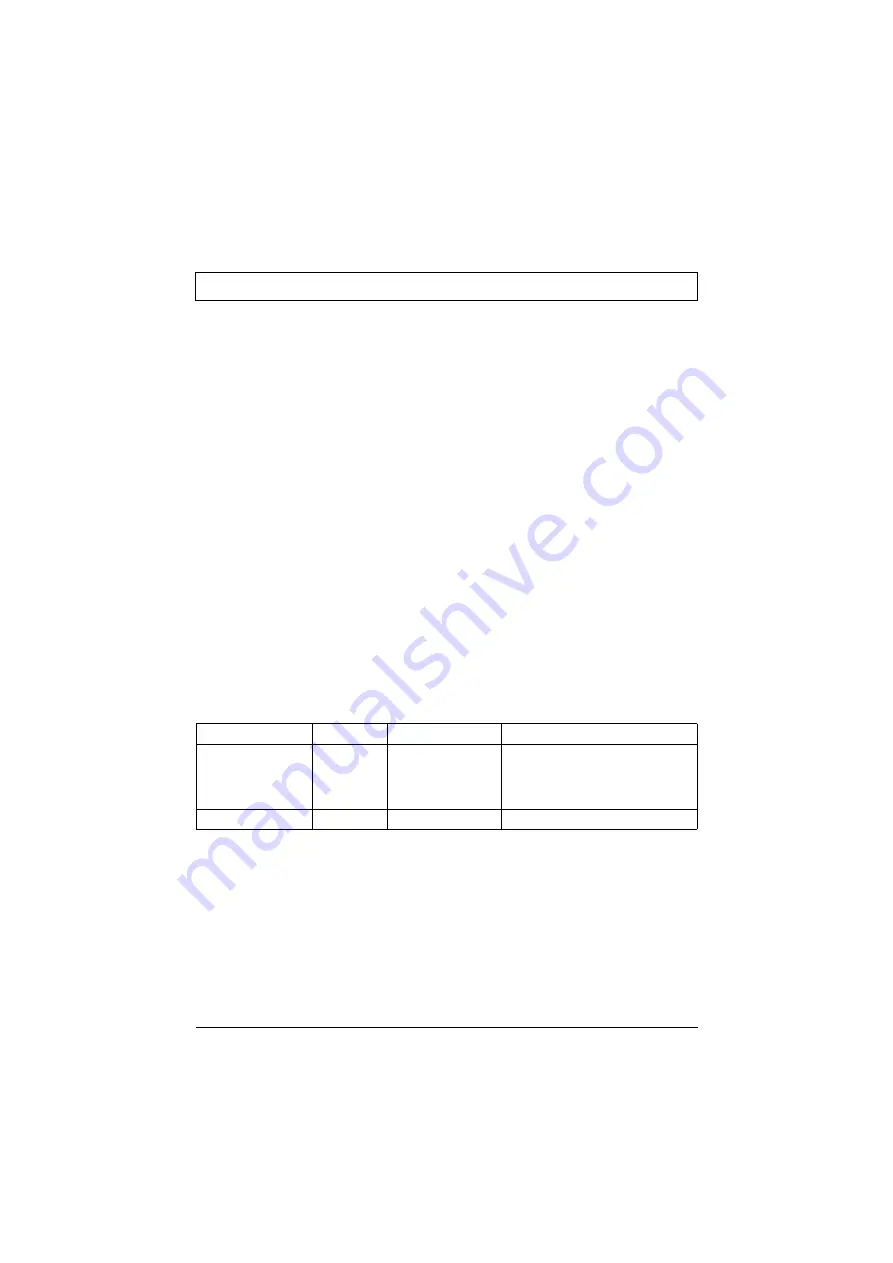
16
VBMS ....
Fusing according to allocation type „1“:
As pre-fuses, we recommend to use line protection fuses (utilization category gL) or automatic
circuit breakers with tripping characteristic B, C, D or K.
Taking into account the maximum braking currents that occur (normally the rated device current),
we recommend fuses according to table 2, column 3.
Note:
Wiring cross-sectional area according to DIN VDE 0100-430,
DIN EN 57100-430.
Fusing according to allocation type „2“:
The power semiconductors are to be protected by fuses of the utilization category gR (semicon-
ductor fuses, high-speed fuses). However, since these fuses do not ensure line protection, it is
necessary to use additionally line protection fuses (utilization category gL).
As for the dimensioning of the line protection fuse (gL), please refer to table 2, column 3.
To protect the semiconductors it is necessary to select gR-fuses featuring cutoff-I²t-values of the
ranges indicated in table 2, column 4. In this connection, the fuse rating of the selected fuse
should not be smaller than the braking current to be expected (rated device current).
Note 1:
On the basis of the recommended I²t-value, braking current, and possibly the
c.d.f., the fuse supplier is able to select a suitable type. Due to the great
variety of producers, sizes, and types, PETER electronic does not
recommend any particular fuses.
Note 2:
If the fuse or cutoff-I²t-value is selected too small, it may happen that the
semiconductor fuse reacts during braking.
Table 2
Column 1
Column 2
Column 3
Column 4
max. Braking
current / Rated
device current
Device type
Fuse value
in the case of
allocation type 1
Recommended range for
cutoff-I²t-value of semiconductor
protection fuses in the case of
allocation type „2“
20A
VBMS
16A
300… 650 A²s
Summary of Contents for 2C000.23020
Page 19: ...18 VBMS 14 Dimensional drawings All dimensions in mm 100 120 73...
Page 21: ...20 VBMS...
Page 22: ......