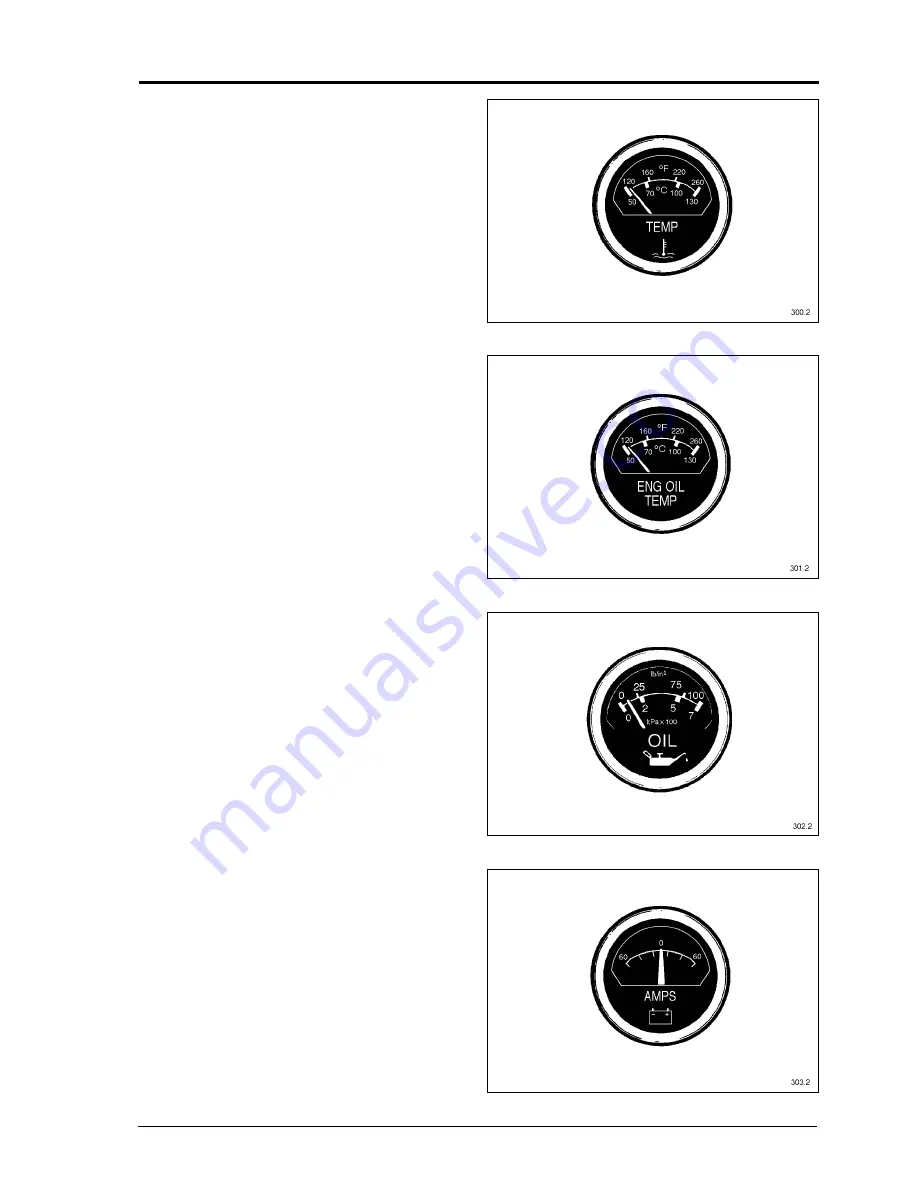
INSTRUMENT PANEL
4012/16 Gas, February 1998
23
Engine water temperature gauge
(Fahrenheit/Centigrade)
Fig. 6
The coolant temperature during normal
operation should be between 65°C - 85°C
(149°F - 185°F). If the temperature should
rise above 93°C (200°F) for a prolonged
period of time, stop the engine and investi-
gate the cause. The engine should, on the
other hand, not be run at too low a tempera-
ture for long periods either.
Engine oil temperature gauge
(Fahrenheit/
Centigrade)
Fig. 7
The lubricating oil temperature should be
between 80°C - 90°C (176°F - 194°F) when
the engine is hot. If the temperature should
rise above 115°C (240°F), stop the engine
immediately and investigate the cause.
Engine oil pressure gauge Fig. 8
(pounds per square inch/kiloPascal x 100)
The lubricating oil pressure should be
between 300 - 350 kPa (45 - 50 lb/in
2
) when
the engine is hot. If the pressure should
drop below 200 kPa (30 lb/in
2
) at higher
engine speeds than idling, stop the engine
immediately and investigate the cause.
Ammeter (Ampere) Fig. 9
The ammeter indicates at what charging
current the battery is being charged by the
alternator, or to what extent current is taken
from the battery without the battery being
recharged.
Fig. 6
Fig. 7
Fig. 8
Fig. 9
Summary of Contents for 4012TESI Series
Page 1: ...TSL4187E Issue 1 February 1998 User s Handbook Perkins 4012 and 4016 Gas 4012TESI 4016TESI...
Page 7: ...4012TESI MINNOX 4012TESI MINNOX...
Page 8: ...4016TESI MINNOX 4016TESI MINNOX...
Page 49: ...4012 4016 GAS ENGINES FAULT TRACING CHART 4012 16 Gas February 1998 45 Fig 34...
Page 57: ...1998 Perkins Engines Company Limited All Rights Reserved...