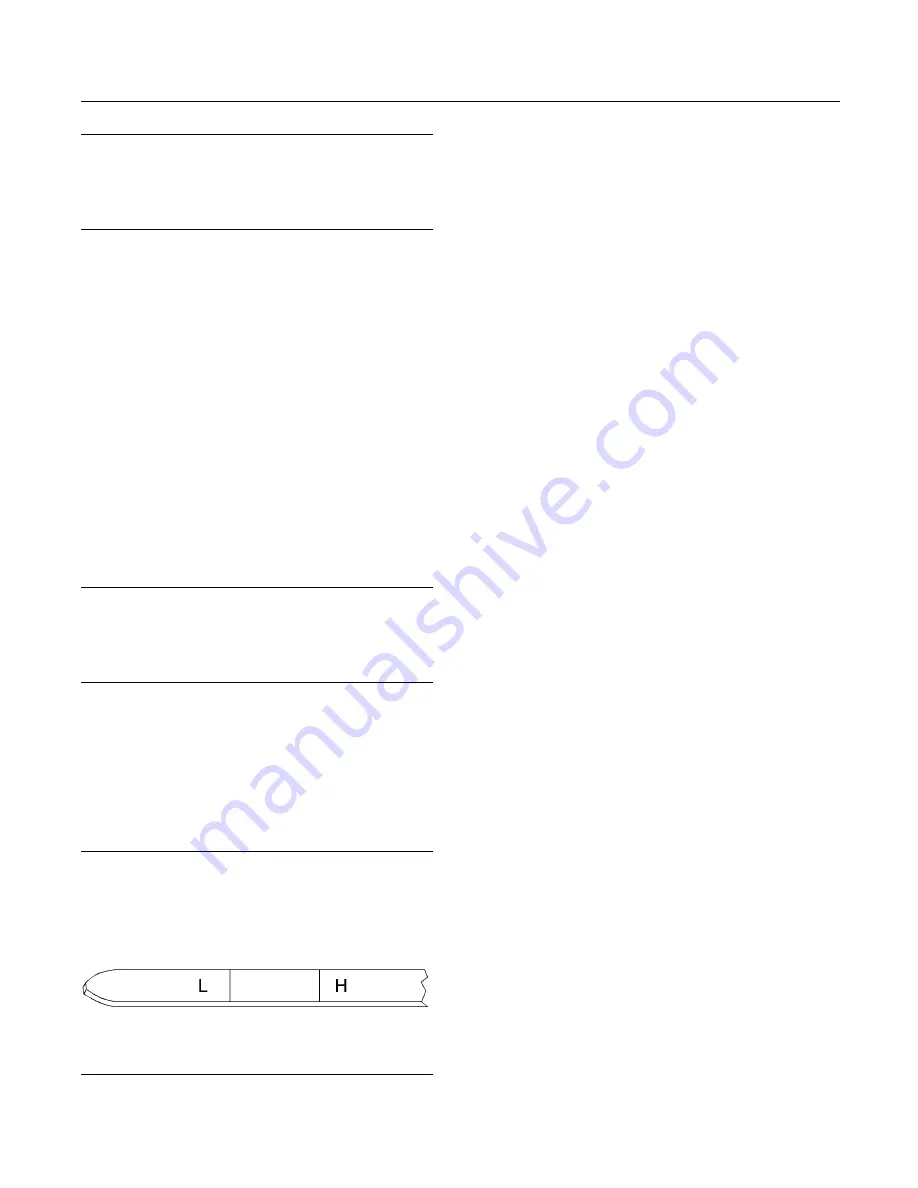
SEBU8605-01
99
Maintenance Section
Fan Clearance - Check
NOTICE
Do not
fi
ll the oil
fi
lters with oil before installing them.
This oil would not be
fi
ltered and could be contaminat-
ed. Contaminated oil can cause accelerated wear to
engine components.
6.
Apply clean engine oil to O ring seal (3) for the
new oil
fi
lter (4).
7.
Install the new oil
fi
lter. Spin on the oil
fi
lter (4)
until the O ring contacts the sealing surface (2).
Then rotate the oil
fi
lter ¾ of a full turn. Remove
the container and disposal of the waste oil in
accordance with local regulations.
Fill the Oil Pan
1.
Remove the oil
fi
ller cap. Refer to this
Operation and Maintenance Manual, “Fluid
Recommendations” for more information on
suitable oils. Fill the oil pan with the correct
amount of new engine lubricating oil. Refer
to this Operation and Maintenance Manual,
“Re
fi
ll Capacities” for more information on re
fi
ll
capacities.
NOTICE
If equipped with an auxiliary oil
fi
lter system or a re-
mote
fi
lter system, follow the OEM or the
fi
lter manu-
factures recommendations. Under
fi
lling or over
fi
lling
the crankcase with oil can cause engine damage.
2.
Start the engine and run the engine at “LOW
IDLE” for 2 minutes. Perform this procedure in
order to ensure that the lubrication system has
oil and that the oil
fi
lters are
fi
lled. Inspect the oil
fi
lter for oil leaks.
3.
Stop the engine and allow the oil to drain back to
the oil pan for a minimum of 10 minutes.
g02173847
Illustration 67
“L” Low
“H” High
4.
Remove the engine oil level gauge in order to
check the oil level. Maintain the oil level between
“L” and “H” marks on the engine oil level gauge.
Do not
fi
ll the crankcase above the “H” mark.
i04323342
Fan Clearance - Check
There are different types of cooling systems. Refer to
the OEM for information on clearance for the fan.
Ensure that the engine is stopped. Ensure that the
cooling system is full. The clearance between the
cover (1) and the fan (2) will require checking. The
gap (A) between the edge of the cover and the tip of
the fan blade must be checked in four equally spaced
positions.