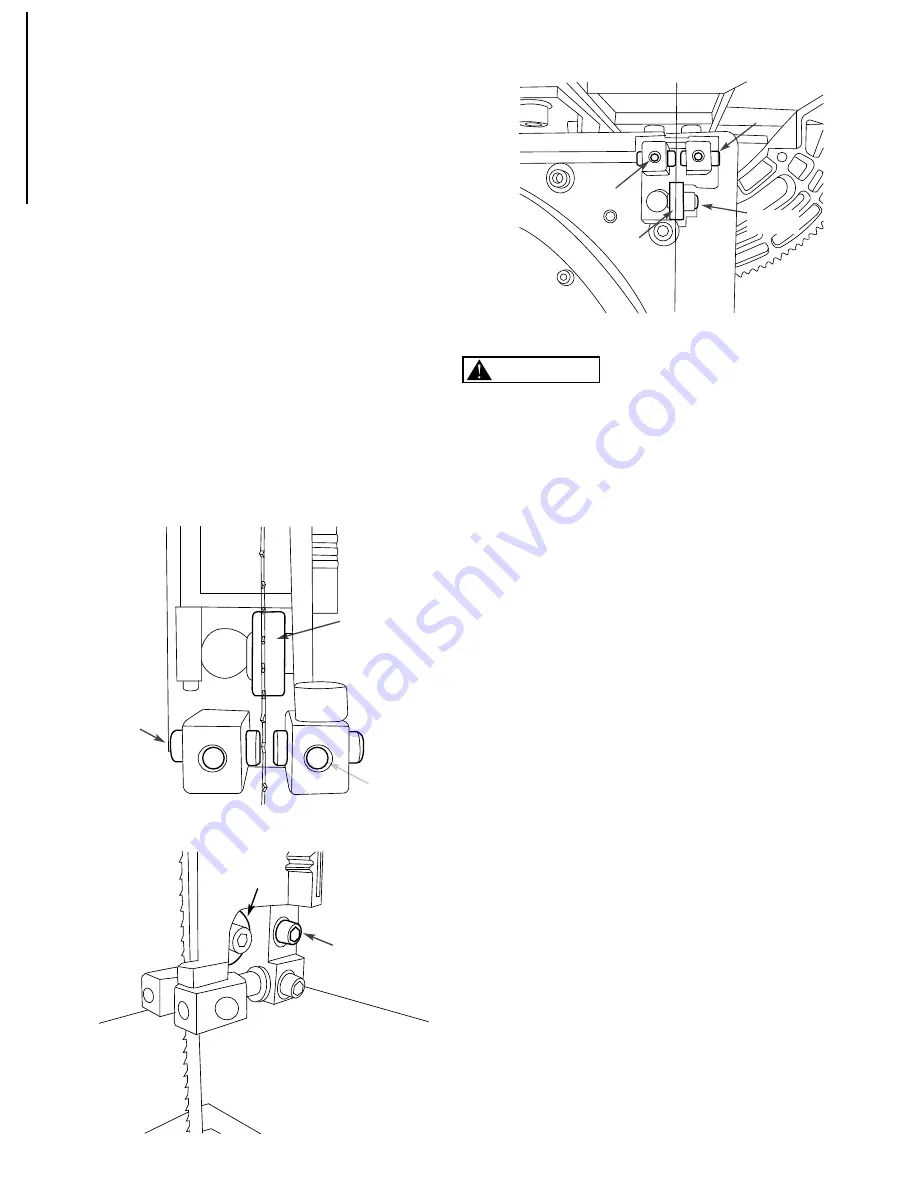
ADJUST BLADE GUIDES
Refer to Figure 9 to 11
•
Blade guides should not be in contact with the blade
when not in operation.
•
Adjust the blade guides after the blade tracking and
blade tension have been properly adjusted.
•
The blade guide supports the blade with bearings on the
real and guide pins on both sides. They all should be
adjusted to be 0.016” inches away from the blade. Use
feeler gauge for accurate measurement. For a quick
gauge, fold a dollar bill in half twice and place it between
the blade and the guide pins or the bearings. The
thickness of 4x dollar bill is approximately 0.016”.
•
To adjust the guide pin position, loosen the screw on
each guide pin block. Secure the screws after
adjustment. Do the same for upper and lower blade
guides.
•
Adjust the upper blade guide bearings position by
loosening the socket head bolt behind the bearings and
reposition the blade guide shaft. Tighten the bolt after
adjustment.
•
Adjust the lower blade guide bearings position by
loosening the socket head bolt behind the bearings and
reposition the blade guide bracket. Tighten the bolt after
adjustment.
MITER GAUGE
Do not use miter gauge and rip fence at the same time.
Operator could be injured or/and the workpiece could be
damaged because the blade might bind in the workpiece.
•
To adjust miter gauge, use a square with one
edge against the miter gauge face and the
other against the blade face.
•
Loosen the lock knob on the miter gauge and
adjust to the right position.
•
Tighten the lock knob and loosen the pointer
screw and adjust the pointer to 0° and tighten
the screw on the pointer.
BLADE WIDTH
• Blade width is the distance from tip of a tooth to back
of blade. The band saw blade width ranges from 1/8” to
1/2”. Curve cutting of 1/8” radius needs the blade width
of 1/8”. Use blade width of ¼” for cutting radius of 5/8”.
Use blade width of 3/8” for 1-1/4” cutting radius.
BLADE PITCH
• Pitch is the number of teeth per inch (TPI) or tooth size.
•
More teeth per inch will cut slower but produce
smoother cutting surface; while fewer teeth per inch will
cut rougher but faster.
•
For soft wood, the proper blade has between 6 to 8
teeth per inch.
•
For hard wood, use a blade with 8 to 12 teeth per inch.
•
Blade shocking occurs when pitch is too large and blade
tooth encounters too much material. This can trip teeth
from blade.
Figure 10
Figure 11
6
OPERATION
WARNING
Socket Head
Bolt
Bearing
Screw
Bearing
Guide Pin
Socket
Head Bolt
Figure 9
Bearing
Screw
Guide Pin
Summary of Contents for 240-3731
Page 11: ...9 BAND SAW PARTS ILLUSTRATION 9...
Page 15: ...Menard Inc Eau Claire WI 54703...