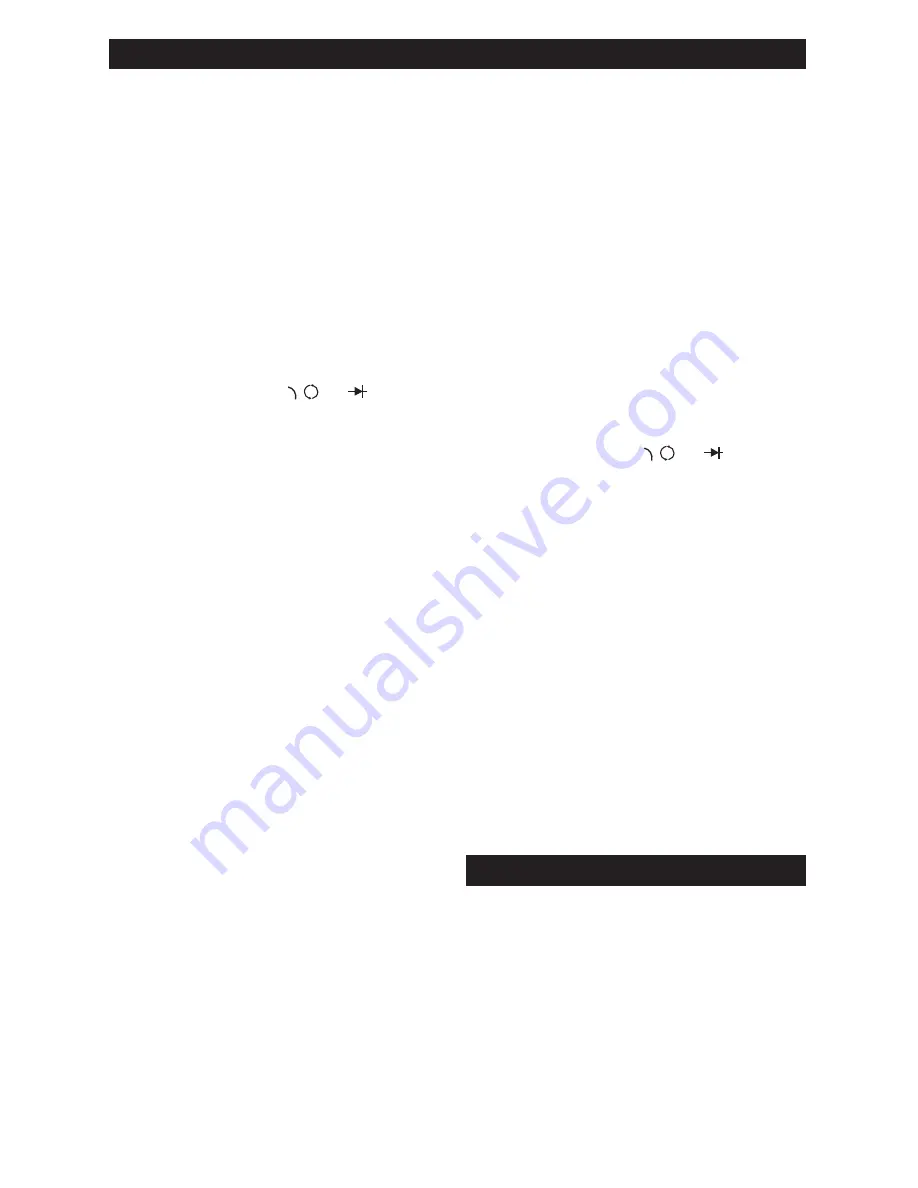
Primary side of the coil is >2.0Ω.
Secondary side of the coil range is on <6 or >35KΩ.
Coil Switching ON/OFF
The primary circuit is driven by closing a switch to
ground, which allows current to flow from the power
supply through the primary. This test checks if the
negative terminal of the primary ignition coil is
getting switched ON and OFF. The signal comes
from the ignition module, and the crankshaft
position sensors. The ON/OFF signal from the
ignition coil is where the Tach gets its RPM
information. If the test vehicle cranks but won’t fire,
this test and fuel delivery is a good place to start.
1. Insert BLACK test lead into COM test lead jack.
2. Insert RED test lead into test lead jack.
3. Add the alligator clips and connect the RED
clip to the negative side of the primary ignition coil.
Refer to your service manual for the primary ignition
coil location.
4. Connect the BLACK clip to a good body ground.
Vehicle with DIS (Distributorless Ignition System),
you’ll need to identify the Tachometer sign wire that
goes from the DIS module to the ECU. Refer to
your vehicle service manual for the location.
5. Connect the RED test probe to the TACH signal
wire, either back probe or pierce the wire.
6. Use the alligator clips and connect BLACK
clip to a good body ground.
7. Turn the meters range selector to the RPM
settings, choice the range that coincides with the
vehicles cylinder count. View the reading on the
display while engine is cranking. Use a helper to
turn the key, or use a remote starter switch, (part
number W80586). A common meter RPM reading
is >20 but <280. Refer to the service manual for
your vehicles cranking RPM range.
• A good Switching Coils RPM reading should have a
value consistent with manufacturer’s specifications.
• A bad Switching Coil will display 0 RPM’s meaning
the coil is not switched ON and OFF.
Possible items to check for would be bad or shorted
wiring, or bad camshaft/crankshaft sensors.
Ignition Wires
OEM type plug wires are usually have a carbon
fiber core that helps minimize RF noise (Radio
noise). The drawback to carbon fiber is it’s a higher
resistance wire. This resistance reduces the amount
of electrical charge that can be delivered to the
spark plug. A hot spark generated the proper bridge
on the plug electrode to burn a full cylinder of fuel.
Use the following steps to test the resistance of
ignition wires, flex the wire while testing for breaks
in the carbon fibers. This test can be used for DIS.
IGNITION SYSTEM TESTS CONT.
ƱⅤ
Ʌ
°
Test the Coil-On-Plug Insulators for breaks and
those systems that mount their ignition coils away
from the spark plugs.
1. Pull and test the ignition wires one at a time.
Avoid the confusion pulling all the wires without
marking where they go.
If possible use a spark plug boot puller, (part
number W80531) to remove the boot and wire. It’s
best to twist the boot a quarter turn both directions
prior to pulling to break the seal.
2. Once removed, look for cracks, burns, or bad ends.
NOTE: Early Chryslers used a plug wire that had
positive-locking terminal electrodes. To pull the
wires the distributor cap needs to be removed. The
release is on the underside of the Dodge Omni, and
the Plymouth Horizon distributor caps.
3. Insert BLACK test lead into COM test lead jack.
4. Insert RED test lead into test lead jack.
5. Add the alligator clip to the RED test probe only,
connect it to the distributor side of the plug wire.
6. Connect the BLACK test probe into the spark
plug boot at the other end of the wire. Be sure it
contacts the metal electrode connector.
7. Turn meters range selector to the 200KΩ range.
8. View the meter while holding and bending the
wire in several places. Over time with heat and
vibration the carbon fibers tend to loosen which
degrades the conduction.
Commonly the resistance levels range from 4KΩ to
40KΩ. The resistance value is directly affected by
the length of each plug wire, averaging 8KΩ to
10KΩ per foot. Refer to vehicle service manual for
your vehicles resistance range.
• A good Ignition Wire will have no change while
flexing and will meet manufacturer’s specification.
• A bad Ignition Wire reading will be erratic while the
wire is flexed, or the readings won’t be within
manufacturer’s specification.
C3 Meter Control Solenoid
Today’s emission requirements have forced auto
makers to move away from the carbureted fuel
delivery systems. Starting in the early 80s’ auto
makers began using electronically controlled
carburetors to lower vehicle emissions. As emission
requirements got tougher the introduction of
computer commanded fuel injection was introduced.
With the reduced emissions, and the benefit of
increased performance, fuel injection was the future
of fuel delivery. Early GM vehicles used the fuel
mixture control solenoid, these solenoids can be
tested with a digital multimeter that offers a Dwell
ƱⅤ
Ʌ
°
FUEL SYSTEM TESTS
13