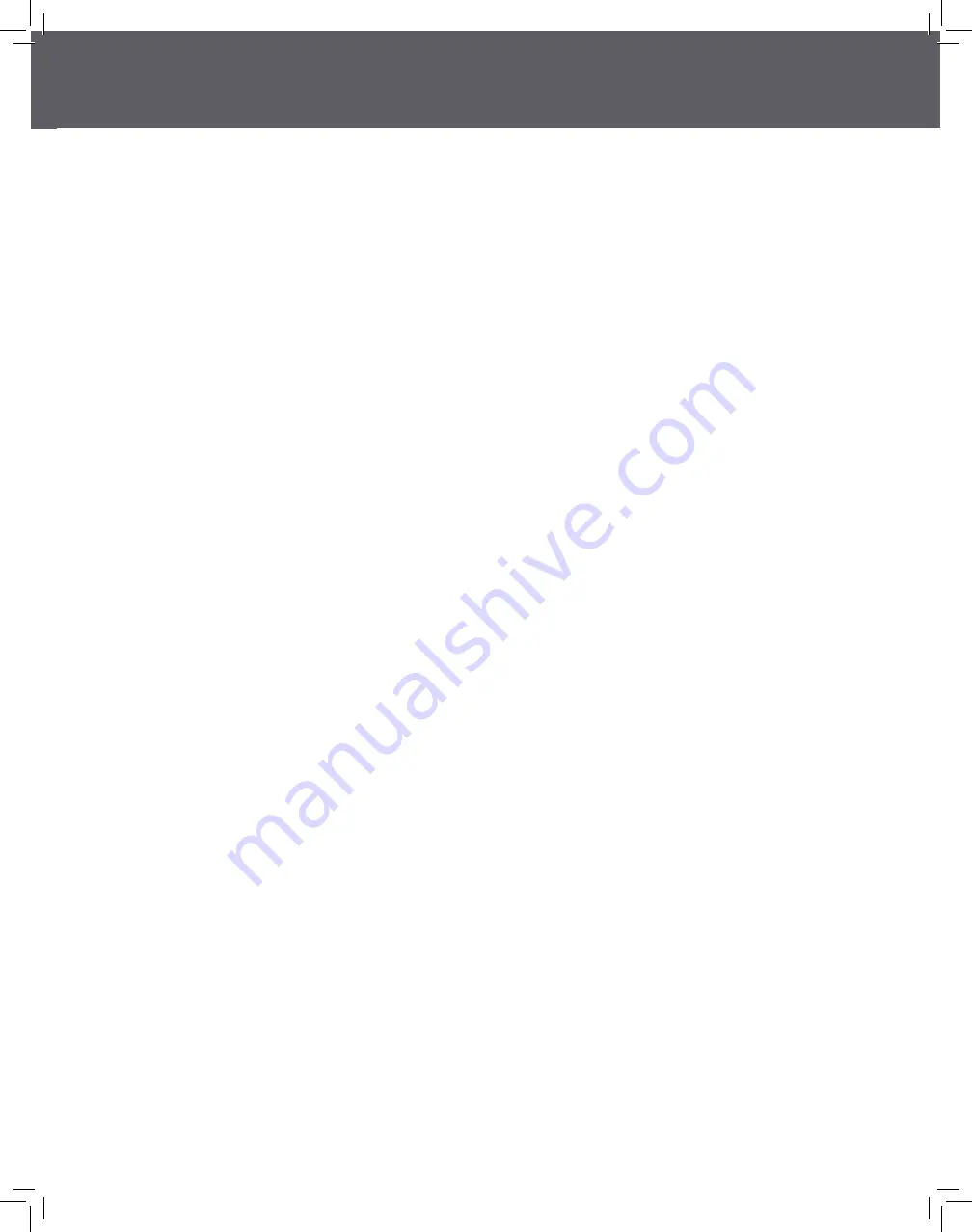
SAFETY PRECAUTIONS
11. Repair to intrinsically safe components
Do not apply any permanent inductive or capacitance loads to the circuit without ensuring that this
will not exceed the permissible voltage and current permitted for the equipment in use. Intrinsically
safe components are the only types that can be worked on while live in the presence of a flammable
atmosphere. The test apparatus should be at the correct rating. Replace components only with parts
specified by the manufacturer. Other parts may result in the ignition of refrigerant in the atmosphere
from a leak.
12. Cabling
Check that cabling will not be subject to wear, corrosion, excessive pressure, vibration, sharp edges or
any other adverse environmental effects. The check shall also take into account the effects of aging or
continual vibration from sources such as compressors or fans.
13. Detection of flammable refrigerants
Under no circumstances should potential sources of ignition be used in the searching for or detection
of refrigerant leaks. A halide torch (or any other detector using a naked flame) should not be used.
14. Leak detection methods
The following leak detection methods are deemed acceptable for systems containing flammable
refrigerants. Electronic leak detectors should be used to detect flammable refrigerants, but the
sensitivity may not be adequate or may need re-calibration. (Detection equipment should be calibrated
in a refrigerant-free area.) Ensure that the detector is not a potential source of ignition and is suitable
for the refrigerant used. Leak detection fluids are suitable for use with most refrigerants but the use of
detergents containing chlorine should be avoided as the chlorine may react with the refrigerant and
corrode the copper pipework. If a leak is suspected, all naked flames should be removed/ extinguished.
If a leakage of refrigerant is found which requires brazing, all of the refrigerant should be recovered
from the system, or isolated (by means of shut off valves) in a part of the system remote from the leak.
Oxygen-free nitrogen (OFN) should then be purged through the system both before and during the
brazing process.
15. Removal and evacuation
When breaking into the refrigerant circuit to make repairs or for any other purpose conventional
procedures should be used. However, it is important that best practice is followed since flammability
is a consideration. The following procedure should be adhered to: Remove refrigerant; Purge the
circuit with inert gas; Evacuate; Purge again with inert gas; Open the circuit by cutting or brazing.
The refrigerant charge should be recovered into the correct recovery cylinders. The system should
be flushed with OFN to render the unit safe. This process may need to be repeated several times.
Compressed air or oxygen should not be used for this task. Flushing should be achieved by breaking
the vacuum in the system with OFN and continuing to fill until the working pressure is achieved, then
venting to atmosphere, and finally pulling down to a vacuum. This process should be repeated until
no refrigerant is within the system. When the final OFN charge is used, the system should be vented
down to atmospheric pressure to enable work to take place. This operation is absolutely vital if brazing
operations on the pipework are to take place. Ensure that the outlet for the vacuum pump is not close
to any ignition sources and there is ventilation available.
CONTINUED
9