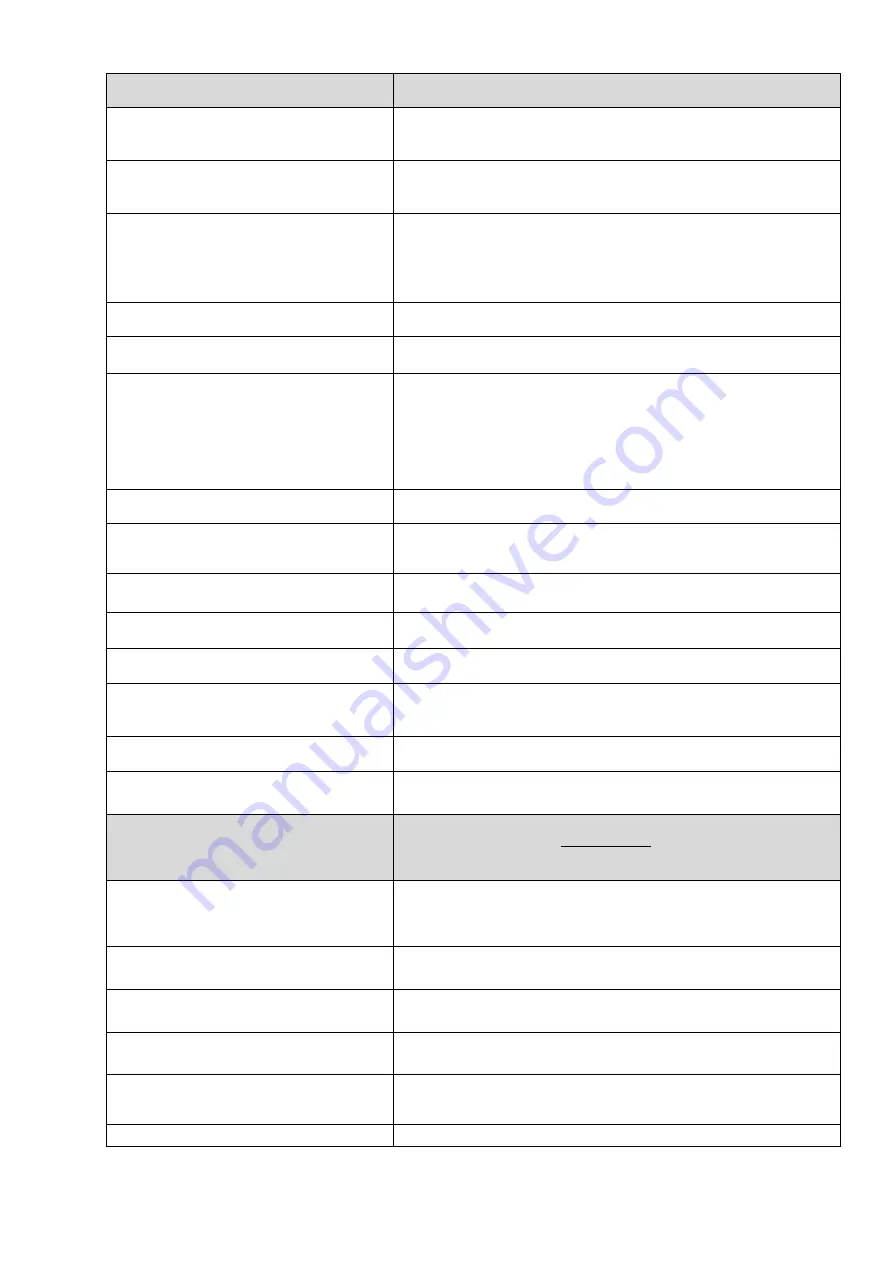
38
12
BOILER SERVICE SETTINGS
Burner Settings
Blow in output SUPERV.
Power of the fan in SUPERVISION mode - too high value may
cause boiler overheating or flash back to the feeder; too low
value - may result in fuel pouring.
Feeding Time SUPERVISION
Time of fuel feeding in SUPERVISION mode; Too high value
may cause boiler overheating or fuel pouring; too low - fuel
return to the feeder.
Airflow oper.extend. SUPERV
In SUPERVISION mode of boiler operation, once the fuel dose
has been supplied and the feeder stopped, the fan remains in
operation for a time set in "
Airflow oper.extend.
to fire-up the
fuel dose supplied. Value of this parameter may not be too high
because it may lead to boiler overheating
Fan in SUPERV.
Enable to start and stop the fan in SUPERVISION mode
Min. blow-in output
Min. blow-in output which may be set in the parameters related
with the fan power available in the User's menu.
Cycle order OPERATION
Setting this parameter at "Feeding-
break”
causes the
OPERATION mode will start from a feeding of fuel dose. Setting
this parameter
at ,”Break
-
Feeding” causes the OPERATION
mode will start from break in fuel feeding. This parameter is
helpful in case of frequent boiler change-over from
SUPERVISION to OPERATION mode, where fuel pouring or
furnace lowering may occur.
Fuzzy Logic
Fuzzy Logic settings are available only for boiler manufacturers
Min. preset boiler temperature
This parameter prevents the user to set too low value of boiler
preset temperature. Boiler operation at too low temperature
may cause its quick damage, corrosion, dirt, etc.
Max. preset boiler temperature
This parameter prevents the user to set too high value of boiler
preset temperature.
Reduction value
This parameter determines the temperature at which the boiler
will return from SUPERVISION to OPERATION mode
No fuel detection time
It is the time after which the regulator starts the procedure of
detecting lack of fuel.
No fuel Del T
Difference between preset boiler temperature and actual boiler
temperature, at which the boiler starts the procedure of
detecting lack of fuel.
Maximum feeder temperature
It is the temperature at which the protection against flashback
to fuel feeder activates.
Boiler cooling temp.
Temperature at which boiler cooling down described in sec.
17.2 occurs.
Return Protection4D
A list of settings for boiler return protection function performed
using 4-way valve with electric servo. This function is not active
if return sensor is disconnected or Mix1 support is OFF.
Activation of this function causes all mixers close.
OPERATION mode
This parameter switches ON and OFF the boiler return
protection function performed using mixing valve with electric
servo. Note: do not switch on this function if the valve is not
provided with electric servo!
Min. return temp
Boiler return temperature below the value at which electric
servo closes mixing valve.
Return temp. hyst
Electric servo returns to normal operation at the return
temperature ≥
min.return tempe Return temp. hyst.
Valve closing
It is % opening of mixing valve during active return protection
function. Note: the valve closes with accuracy of +/-1%.
Reserve boiler
The temperature of retort boiler at which reserve boiler (e.g.
gas fired boiler) will be OFF is set using this parameter. Details
- see sec. 11.11
Alarms
Details - see sec. 11.12
Summary of Contents for KSM 17
Page 1: ...Operation and maintenance manual for the KSM series boilers with feeders...
Page 26: ......
Page 31: ...REGULATOR INSTRUCTION MANUAL ecoMAX 910R1...
Page 41: ...USER MANUAL OF CONTROLLER INSTALLATION AND SERVICE SETTINGS ecoMAX 910R1...
Page 47: ...23...
Page 71: ...47...
Page 74: ......
Page 102: ......
Page 103: ......