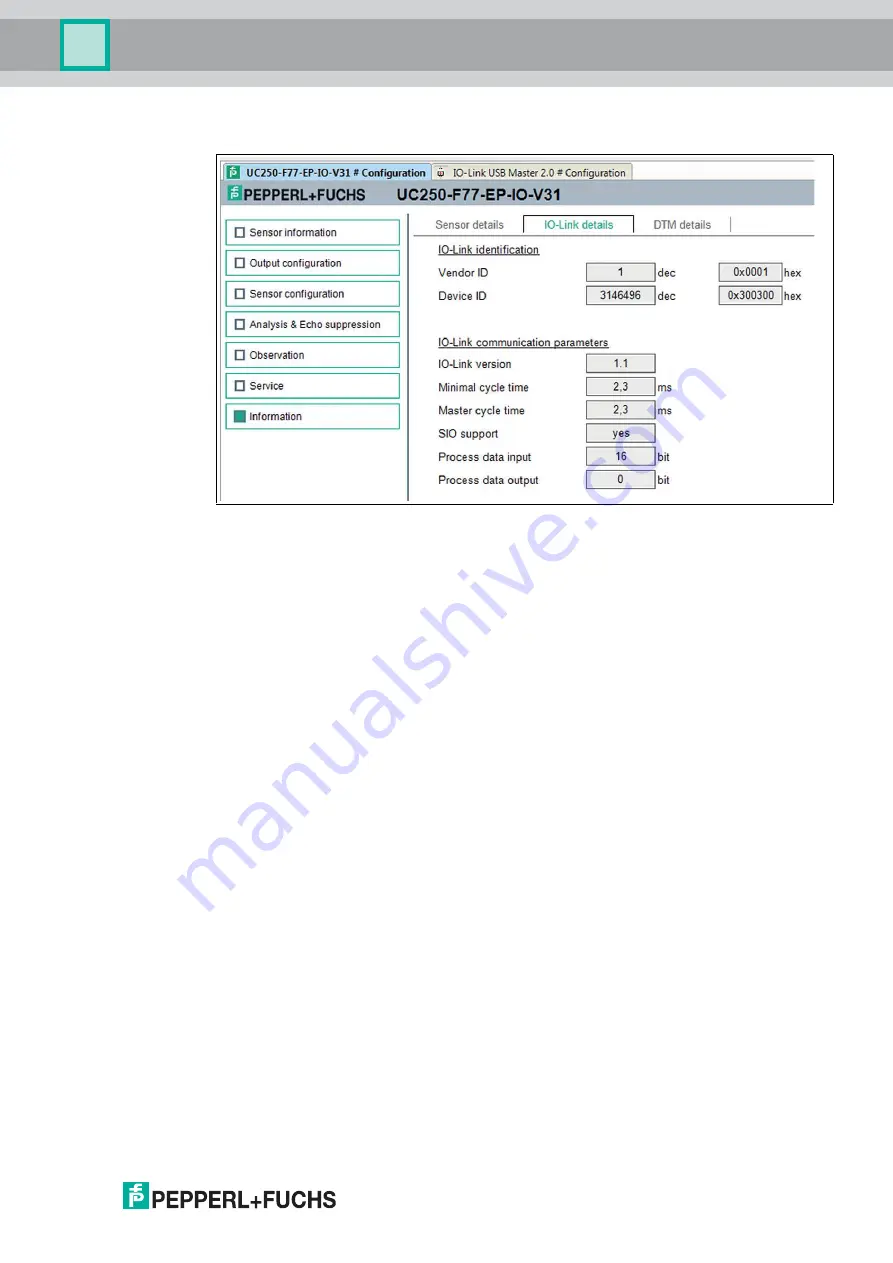
Configuration and Analysis with DTM via IO-Link
2
0
1
7
-0
6
43
7.8
Information Menu Option
Figure 7.18
The
Information
menu option consists of 3 tabs
■
Sensor Details:
information about hardware and software version
■
IO-Link Details:
information about the device ID, vendor ID and information about the IO-
Link communication parameters
■
DTM Details:
Information about the DTM version