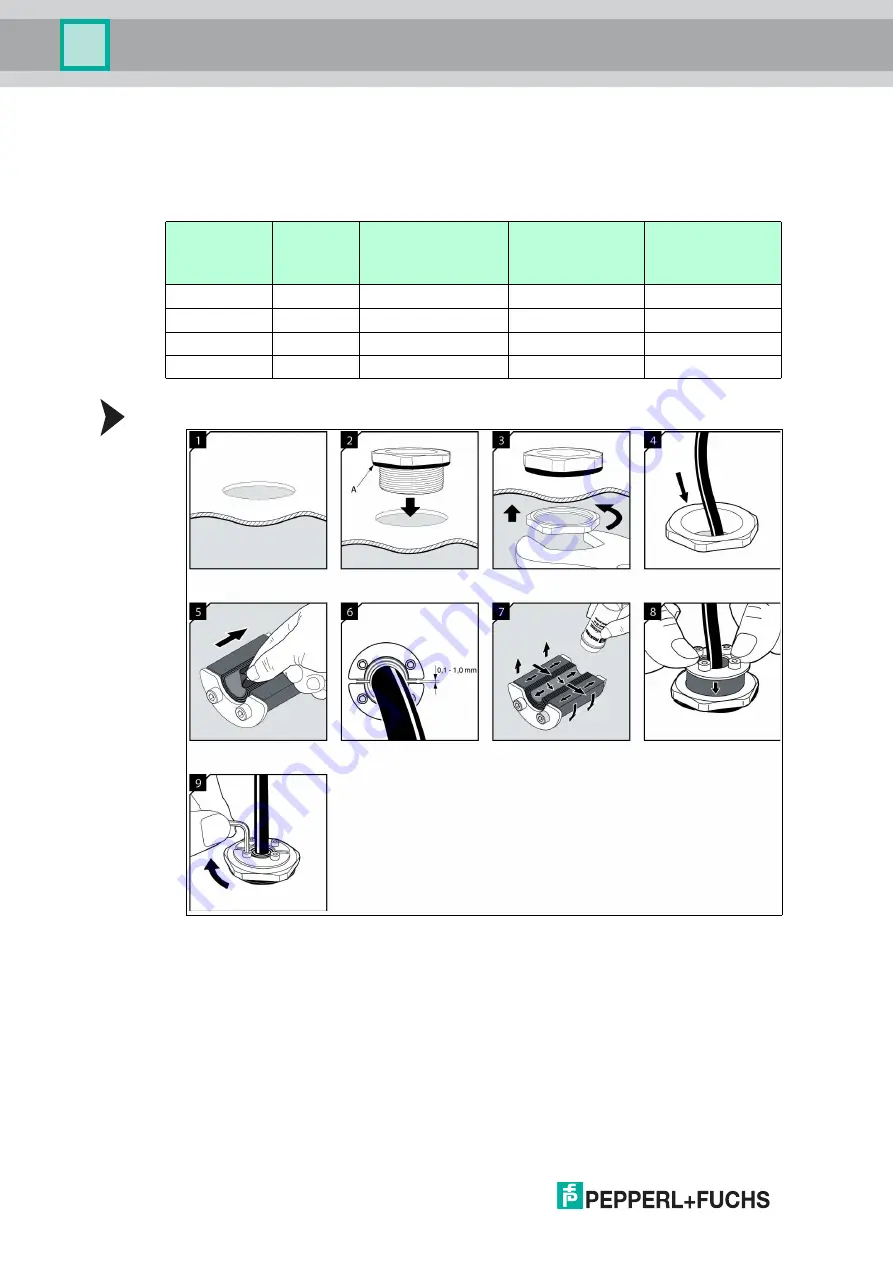
2
0
1
8
-1
2
58
Installation
3.14.3
Cable gland for prefabricated cables to Ethernet gateways
This section describes how to seal a cable gland at a switch cabinet for a prefabricated cable in
a Zone 1 explosion-hazardous area.
Product Data
Fitting the seal for pre-fabricated cables
Figure 3.27
Fitting the seal
1. Make a hole for the screw sleeve in accordance with the "product data" table above.
2. Ensure that the rubber seal (A) is correctly attached to the screw sleeve. Insert the screw
sleeve through the thru–hole.
3. Feed the union nut onto the screw sleeve from inside the enclosure and tighten the union
nut to the specified torque according to the table above.
4. Run the cable through the screw sleeve.
5. Adjust the seal to the cable. Pull the layers off the halves until you achieve the gap shown in
step 6 (0.1 - 1 mm). Ensure that the halves do not differ from each other by more than one
layer.
Type
Torque
lock nut
[Nm]
Width across flats
[mm]
Opening Ø
[mm]
Cable area
[mm]
C RS T 25
20
36
33
0+3.6 - 12
C RS T 31
25
46
41
0+4.0 - 17
C RS T 43
30
60
52
0+4.0 - 23
C RS T 50
35
70
64
0+8.0 - 30