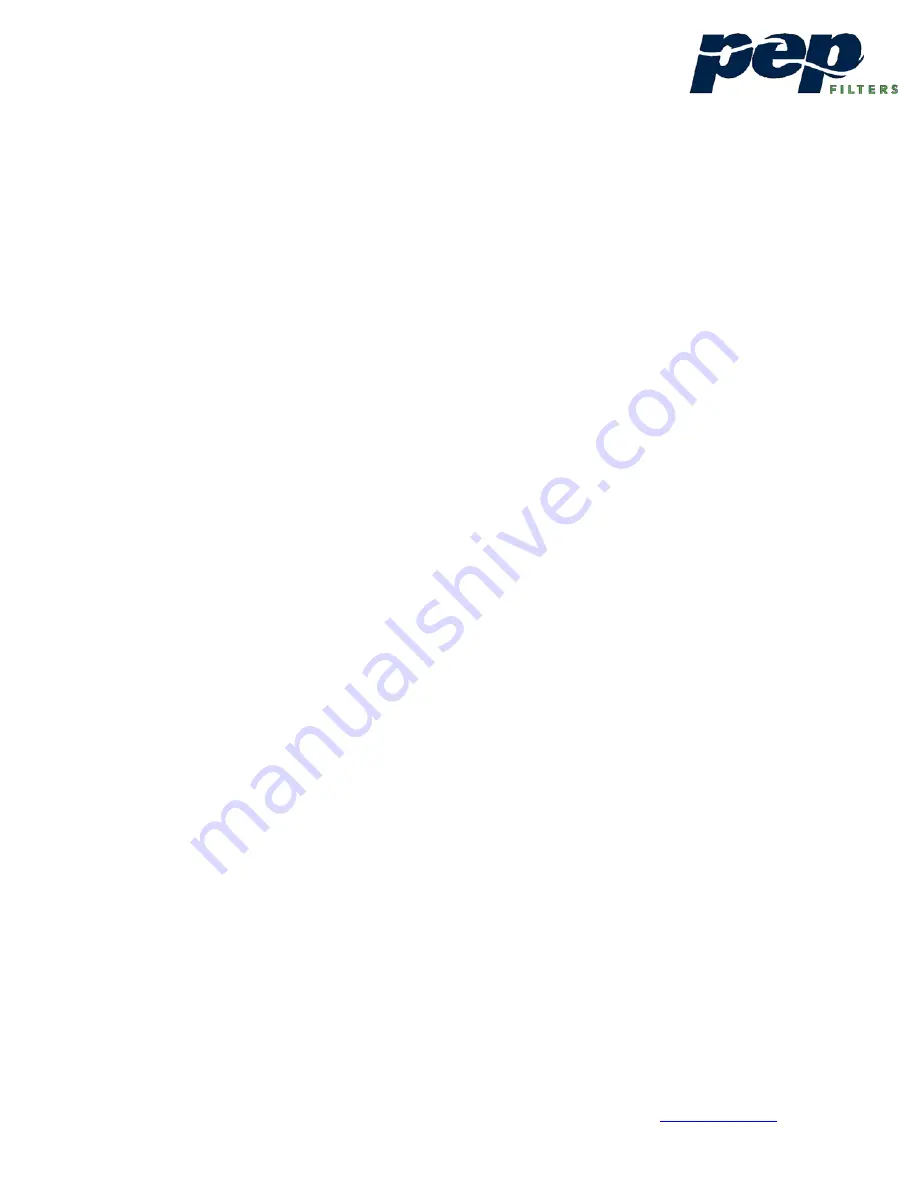
CL Series Filter System
Operating & Maintenance Manual
PEP Filters
•
322 Rolling Hill Road
•
Mooresville, NC 28117
•
800-243-4583
•
www.pepfilters.com
7 of 17
Rev. 030702
Operation And Maintenance
Initial And Seasonal Start-Up
Before initial start-up or after a shut down period, the CL filter should be thoroughly
inspected and cleaned.
Caution
: Perform the first five of the following recommendations with power off.
Refer to the Safety Precautions on Page 8, regarding the safeguarding of
maintenance personnel from biological contaminants, prior to initial and seasonal
start-up.
1. On PEP CL filters, loosen the bolts around the pump pre-strainer tank lid.
Remove the lid, inspect the O-ring seal and lubricate. Clean debris from the
pump pre-strainer basket. Prime the pump suction line by filling the strainer
basket housing. Replace the basket, lid and bolts.
2. Turn the pump and motor shaft by hand to ensure free rotation (if possible).
3. On manual systems only, rotate the valves manually by moving the valve
linkage up and down to ensure free operation. Make sure the valves and
linkage are in the correct position before start-up.
4. On PEP filters, loosen the access bolts on access port lid, remove lid and
lubricate the bolts as necessary.
5. Inspect the over drain assembly and media pack. If the media pack is
contaminated, remove the foreign material or replace the media, and replace
the access port.
6. Open manual air relief valve on top of the filter tank. Start the pump motor
briefly and check the arrow on the pump volute for proper rotation. Turn the
pump motor off. Do
not
operate the pump for an extended period of time
with the pump rotating backwards. Have a qualified electrician change leads
to correct rotation.
7. With the air relief valve open on top of filter tank, check the shut-off valves in
the filter inlet and outlet water lines to verify they are open. Make sure the
pump is primed. Start the pump and allow the filter vessel to fill. Wait for all
air in vessel to be released before closing the manual air relief valve.
8. Check the voltage and current of all leads on the pump motor. The current
amp draw should not exceed the pump motor nameplate rating.
9. Check the unit for any unusual noise or vibration and contact your local PEP
Representative if noise or vibration occurs.
10. Check the unit for any air or water leaks. Leaks must be repaired. Failure to