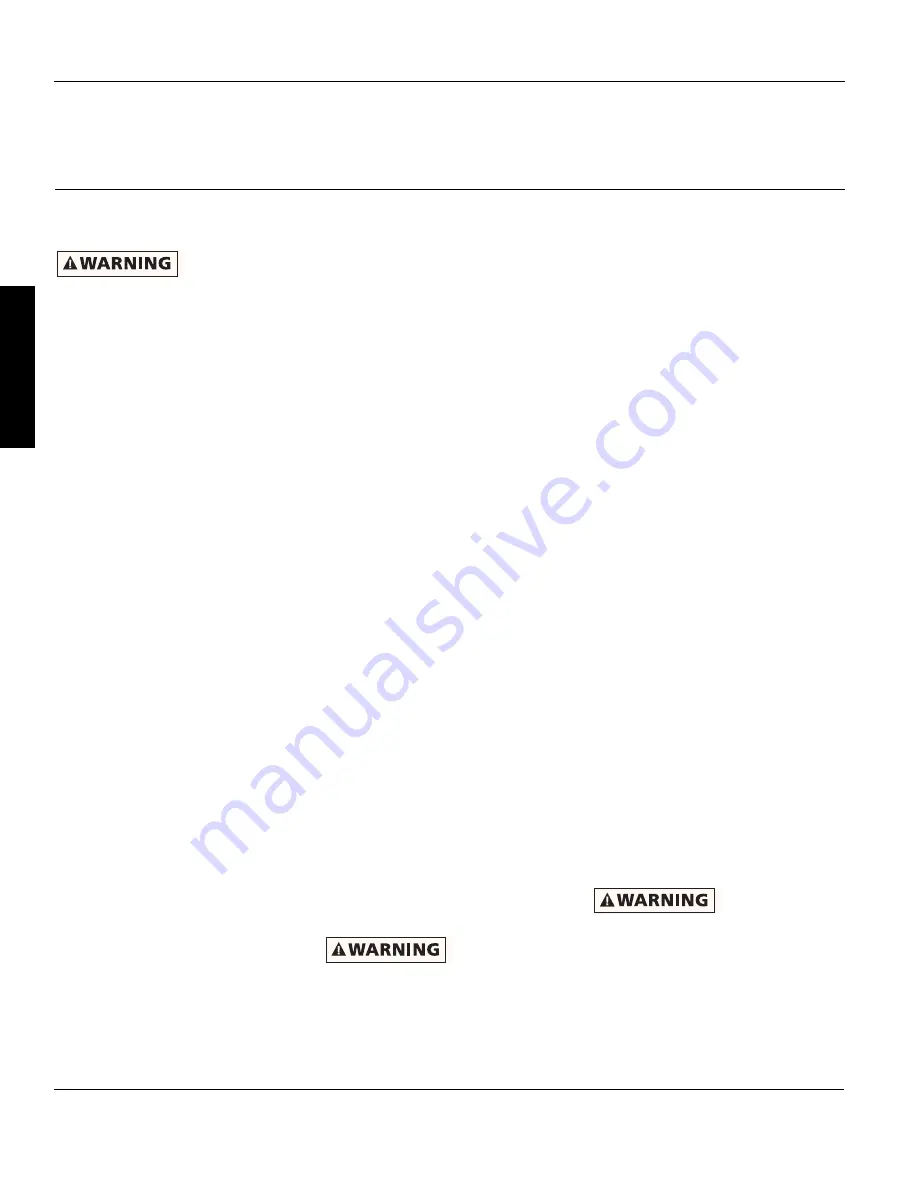
General Safety Information
(Continued)
Hazardous pressure.
Incorrectly installed
or tested equipment may fail, causing
severe injury or property damage. Read
and follow instructions in owner's manual
when installing and operating equipment.
Have a trained pool professional perform
all pressure tests.
1. Do not connect system to a high
pressure or city water system.
2. Use equipment only in a pool or spa
installation.
3. Trapped air in system can cause
explosion. BE SURE all air is out of
system before operating or testing
equipment.
Before pressure testing, make the
following safety checks:
Check all clamps, bolts, lids, and system
accessories before testing.
Release all air in system before testing.
Tighten trap lids to 30 ft. lbs.
(4.1 kg-m) torque for testing.
Water pressure for test must be less
than 25 psi (7.5 kg/cm
2
).
Water temperature for test must be less
than 100° F. (38° C).
Limit test to 24 hours. After test,
visually check system to be sure it is
ready for operation. Remove trap lid
and retighten hand tight only.
NOTE:
These parameters apply to
equipment in this OIPM only. For
other equipment, consult manufacturer.
Installation
Only qualified, licensed personnel
should install pump and wiring.
Pump installation must:
Be located away from corrosive or
flammable liquids.
Have enough ventilation to maintain air
temperature at less than the maximum
ambient temperature rating (Max.
Amb.) listed on the motor model plate.
If this pump is installed in an
enclosure/pump house, the enclosure
must have adequate ventilation and air
circulation to keep the temperature in
the enclosure at or below the motor’s
rated ambient temperature whenever
the pump is running.
Be solid - Level - Rigid - Vibration free
(To reduce vibration and pipe stress,
bolt pump to mount.)
Allow pump suction inlet height to be
as close to water level as possible. Pump
will not lift water more than 10' (3m).
Allow use of short, direct suction pipe
(To reduce friction losses).
Allow for gate valves in suction and
discharge piping.
Have adequate floor drainage to
prevent flooding.
Be protected from excess moisture.
Allow adequate access for servicing
pump and piping.
NOTE:
When connecting threaded pipe
directly to pump, use Teflon tape or
Plasto-Joint Stik
1
to seal connections. Do
not use pipe dope; pipe dope causes
cracking in some plastics and may
damage components in piping system.
When connecting pipe to pump with
union half, use Teflon tape or Plasto-
Joint Stik
1
between pipe and union
adapter. Union collar to pump should
be assembled dry and hand-tight.
NOTE:
Pump suction and discharge
connections have molded in thread
stops. DO NOT try to screw pipe in
beyond these stops.
Fire and burn
hazard. Modern
motors run at high temperatures. To
reduce the risk of fire, do not allow
leaves, debris, or foreign matter to collect
around the pump motor. To avoid burns
when handling the motor, let it cool for
20 minutes before trying to work on it.
TEFLON TAPING INSTRUCTIONS:
Use only new or clean PVC pipe fittings.
Wrap male pipe threads with one to
two layers of Teflon tape. Cover entire
threaded portion of pipe.
Do not
overtighten or tighten past
thread stop in pump port!
If leaks occur, remove pipe, clean off
old tape, rewrap with one to two
additional layers of tape, and remake
the connection.
NOTE:
Support all piping connected
with pump!
PIPING:
Use at least 1
1
⁄
2
" (38mm) pipe (use 2"
(51mm) pipe if possible). Increase size if
a long run is needed. When using 1
1
⁄
2
"
pipe, connect to pump with 1
1
⁄
2
to 2" (38
to 51mm) reducing adapter.
To avoid strains on the pump, support
both suction and discharge pipes
independently. Place these supports
near the pump.
To avoid a strain left by a gap at the last
connection, start all piping at the pump
and run pipe
away
from the pump.
To avoid airlocking, slope suction pipe
slightly upward toward the pump.
NOTE:
To prevent flooding when
removing pump for service, all flooded
suction systems
must
have gate valves
in suction and discharge pipes.
POOL PUMP SUCTION
REQUIREMENTS
Pump suction is
hazardous and can
trap and drown or disembowel bathers.
Do not use or operate swimming pools,
spas, or hot tubs if a suction outlet cover
is missing, broken, or loose.
Follow the guidelines below for a pump
installation which minimizes risk to
users of pools, spas, and hot tubs.
1
Lake Chemical Co., Chicago, Illinois
2
Teel Operating Instructions and Parts Manual
4RJ93, 4RJ94 and 4RJ95
Teel Pool Pump With Integral Trap
®
E
N
G
L
I
S
H