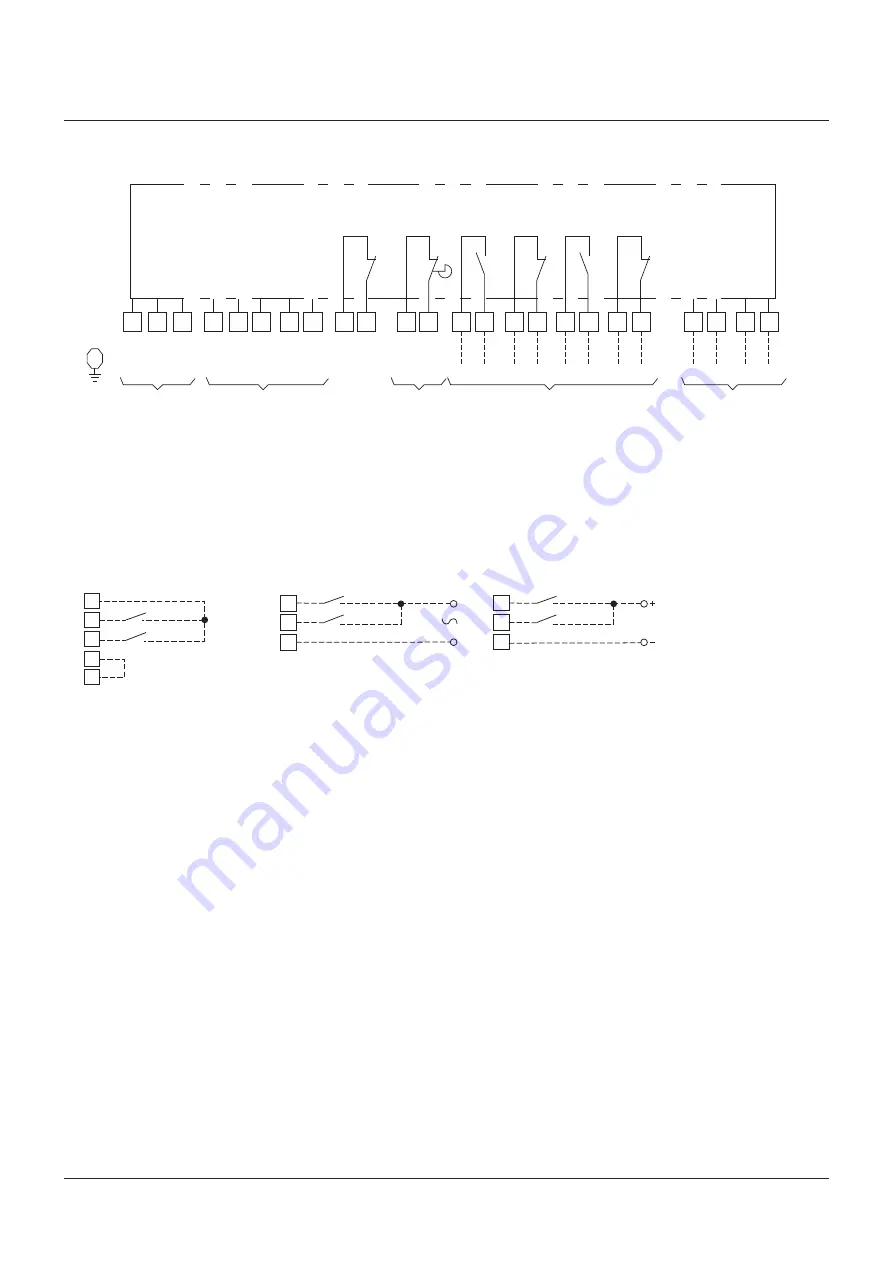
5
L1 L2 L3
35 36 32
33 34
20 21
CLC1
CLC2
OPC1
OPC2
22 23
24 25
26 27
28 29
30 31
1
2
3
4
34
35
36
32
35
36
32
35
36
32
33
35
OP
CL
OP
CL
OP
CL
5. OM3 WIRING dIAGRAM
(note 1)
remote commands
(note 2, 5)
Output contacts
(note 3, 4)
Internal supply 24 V dc
External supply 24/120 V ac
External supply 24/120 V dc
Local Interface
(optional module 3)
Ground
notes
1. Power connection L1 - L2 for V dc or V ac single phase motor supply: from 24 V to 240 V or from 100 V to 240 V
Power connection L1 - L2 - L3 for 3-phase motor supply from 208 V to 575 V (check on the actuator label the correct voltage to be applied)
2. remote commands options
3. contacts shown in intermediate position cLc1 - cLc2 end of travel signaling in CLOSING
contacts shown in intermediate position OPc1 - OPc2 end of travel signaling in OPENING
4. Output contact rating: 240 V ac / 5 a - 30 V dc / 5 a - 120 V dc / 0.5 a
5. control commend rating: 24 to 120 V ac or V dc
6. Blinker or local selector monitoring function (when OM3 is present) to be configured
Keystone
OM3 - EPI-2 LOcaL IntErfacE MOduLE
InstallatIon and MaIntenance InstructIons
(note 6)