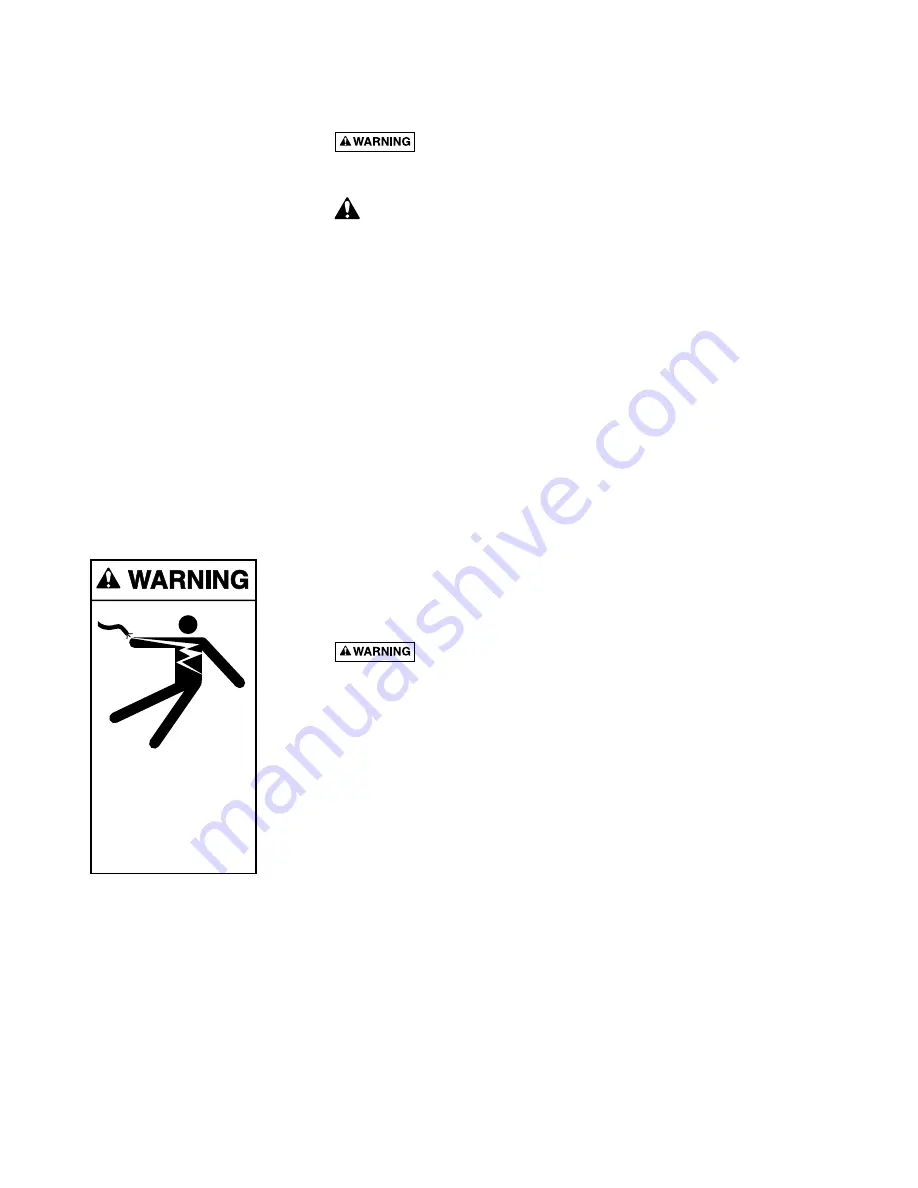
9
Storage/Winterizing:
Explosion hazard. Purging the system with compressed air can
cause components to explode, with risk of severe injury or
death to anyone nearby. Use only a low pressure (below 5 PSI), high vol-
ume blower when air purging the pump, filter, or piping.
To prevent damage to components from fumes, store spa chemi-
cals away from pump and spa. If possible, store chemicals in
another room.
NOTICE:
Allowing pump to freeze will damage pump and void warranty!
NOTICE: Do not
use anti-freeze solutions (except propylene glycol) in your
pool/spa system. Propylene glycol is non-toxic and will not damage plastic
system components; other anti-freezes are highly toxic and may damage
plastic components in the system. Propylene glycol is widely used as
antifreeze in recreational vehicles.
Drain all water from pump and piping when expecting freezing temperatures
or when storing pump for a long time (see instructions below).
Keep motor dry and covered during storage.
To avoid condensation/corrosion problems,
do not
cover or wrap pump with
plastic.
For outdoor/unprotected installations:
1. Pump down water level below all inlets to pool.
2. Enclose entire system in a weatherproof enclosure.
3. To avoid condensation/corrosion damage, allow ventilation;
do not
wrap system in plastic.
4. Use a 40% propylene glycol/60% water solution to protect pump to -
50°F.
5. Follow pool manufacturer’s directions for storage of pool.
Draining Pump:
To avoid dangerous or fatal electrical shock hazard, turn
OFF power to motor before draining pump.
1. Close all valves on suction and return piping.
2. Remove drain plug in bottom of volute.
3. Drain all piping and storage tanks exposed to freezing temperatures.
4. Be sure no airlocks are holding water in the system.
5. To prevent pump from freezing, remove trap cover and drain the tank
body through the drain plug (Key No. 14, Page 12). Use a lid wrench to
remove trap covers that have been overtightened or have taken a set
and cannot be removed by hand. Clean pump thoroughly. Replace trap
cover.
6. Before restarting, replace all plugs and make sure all pipe connections
are tightly sealed.
Startup For Winterized Equipment:
1. Remove any temporary weather protection placed around system for
shutdown.
2. Follow filter manufacturer’s instructions for reactivation of the filter.
3. Inspect all electrical wiring for damage or deterioration over the shut-
down period. Have a qualified serviceman repair wiring as needed.
4. Inspect and tighten all watertight connections.
5. Open all valves in suction and return piping.
6. Remove any winterizing plugs in piping system.
7. Drain all antifreeze from system.
8. Close all drain valves and replace all drain plugs in piping system.
9. Prime pump according to instructions on Page 8.
10. Refill pool to proper water level.
Hazardous voltage.
Can shock, burn,
or cause death.
Disconnect power
before working
on pump or motor.