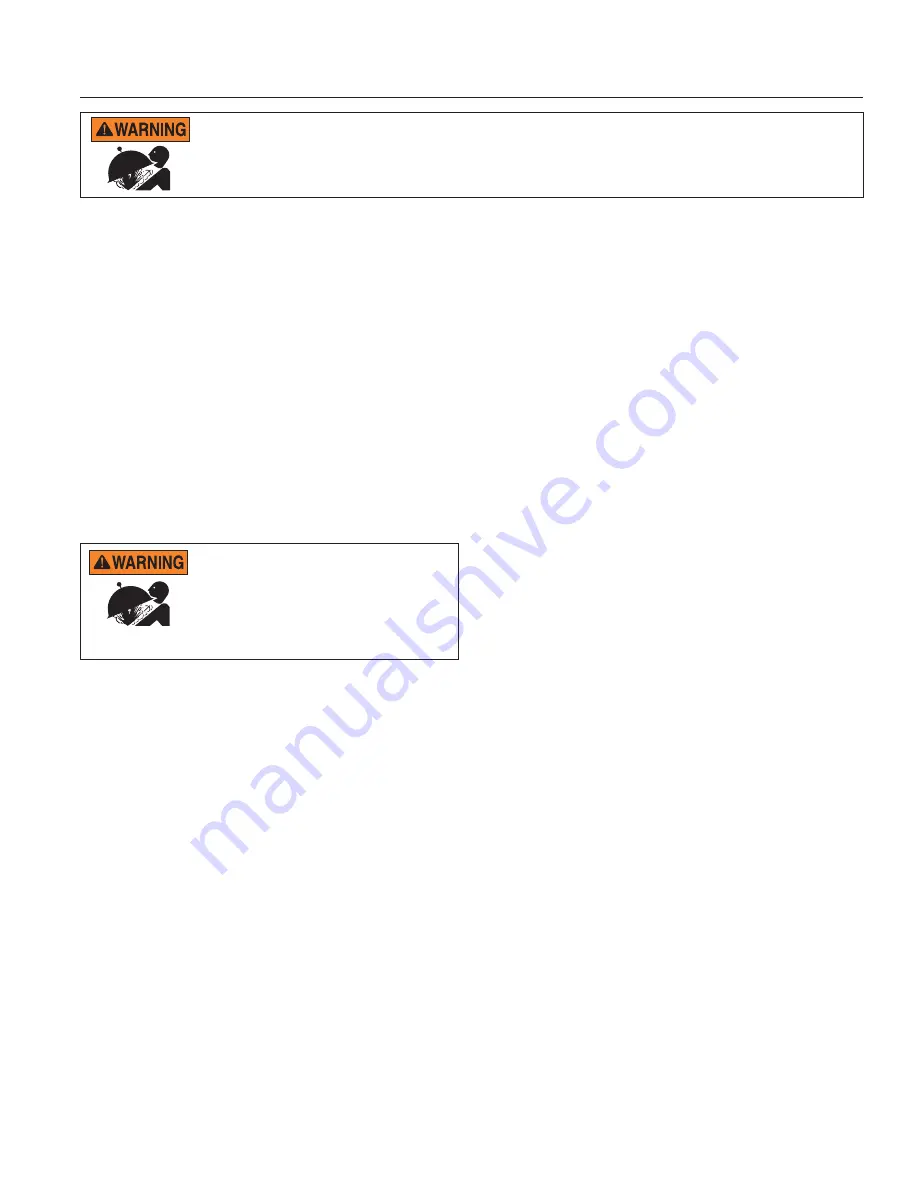
FULLFLO
XF
® 4000-SERIES Grid Style D.E. Filter Installation and User’s Guide
1
GENERAL INFORMATION
THIS SYSTEM OPERATES UNDER HIGH PRESSURE.
When any part of the circulating system (e.g., Clamp Ring, Pump, Filter, Valves, etc.) is serviced, air can enter the system
and become pressurized. Pressurized air can cause the lid to separate which can result in serious injury, death, or
property damage. To avoid this potential hazard, follow the instructions below.
Filter Overview
• Curved filter grid elements maximize filtration area;
internal design minimizes flow restrictions.
• FullFloXF
®
4000-Series D.E. Filter captures
microscopic impurities like dirt, algae, and some
forms of bacteria.
• Includes assembled 2” rotary backwash valve.
• Full 2” inlet/outlet for improved hydraulic efficiency.
• HiFlow™ Manual Air Relief Valve for rapid air release.
General Operation Information
Read and follow all instructions and warnings before
installing or servicing your filter. Proper installation
and operation can prevent unnecessary repairs and
maintenance.
1. This filter operates under pressure and operates in
a safe manner if clamped properly and without air in
the circulating system.
2. The maximum working pressure of this filter is 50
psi. Never subject this filter to pressure in excess
of this amount, even when conducting hydrostatic
pressure tests.
3. Ensure the maximum working pressure of the filter
system does not exceed the maximum working
pressure of any components within the system
during hydrostatic or external leak tests. Consult the
maximum pressure stated on each component of the
system.
4. The pressure gauge is the primary indicator of how
the filter is operating. Maintain your pressure gauge
in good working order (refer to
Maintaining the
Pressure Gauge
).
5. If filter operates without diatomaceous earth (D.E.)
for more than three (3) minutes, filter elements may
be damaged.
Your filter is a piece of machinery, do not tamper
with it, attempt to disassemble it or otherwise
adjust it unless you fully understand it's operation.
Serious injury or death can occur if the equipment
is improperly handled. Consult a pool service
professional for maintenance and service assistance.
Maintaining the Pressure Gauge
The pressure gauge is the primary indicator of how the
system operates. It is critical to keep the pressure gauge
in good condition.
Replace pressure gauge (P/N 190058) if any of the
requirements below are not met:
1. Pressure gauge at zero (0) when pressure is
relieved and system is turned off.
2. Pressure gauge reads correctly while system is in
operation.
3. The pressure gauge is readable and not damaged in
any way.
Pressure Tests
When performing hydrostatic pressure tests or when
testing for external leaks of the completed filtration and
plumbing system, ensure that the Maximum Pressure
that the filtration system will be subjected to
DOES NOT
EXCEED THE MAXIMUM WORKING PRESSURE OF
ANY OF THE COMPONENTS CONTAINED WITHIN
THE SYSTEM.
In most cases, the maximum pressure will be stated on
each component of the system. If doubt exists as to the
pressure to which the system will be subjected, install an
ASME approved automatic Pressure Relief or Pressure
Regulator in the circulation system set to the lowest
working pressure of all of the components in the system.