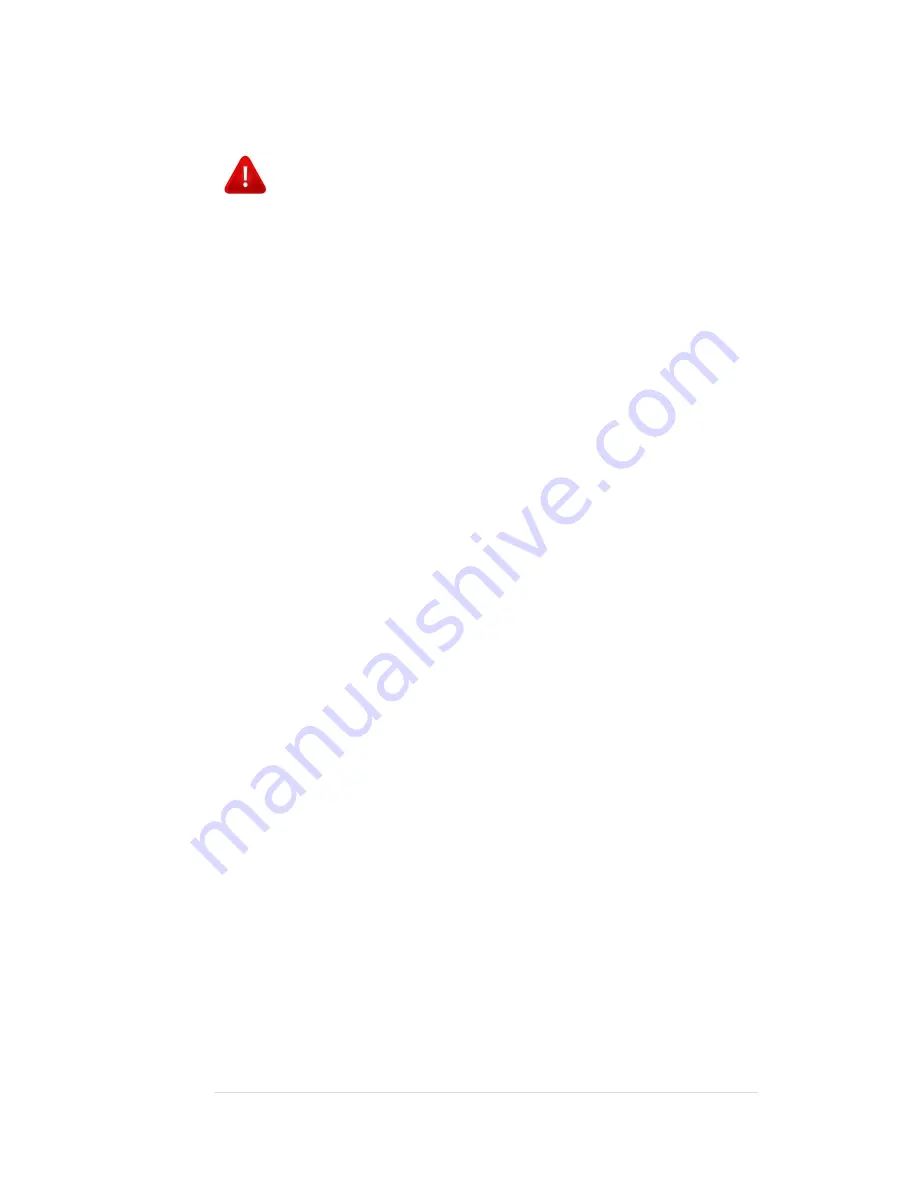
23 |
P a g e
Winterizing the machine
Caution:
Do not store the machine where it will be subject to freezing
temperatures, otherwise severe damage will occur. If it must be stored where
the temperature is below 32° F/0° C, winterize the machine as follows:
1.
Prepare 10 gallons of 50/50 antifreeze and water.
2.
Remove the nozzle from the wand, and lay out the hose and wand flat
on the floor.
3.
Drain the float tank, and refill it with the antifreeze solution.
4.
Hold open the trigger gun while keeping the float tank full of the
antifreeze solution.
5.
Turn the Pump switch on. When antifreeze solution appears at the end
of the gun, release the trigger once or twice, and then turn the Pump
switch off.
6.
When preparing to operate the machine the next time, have an
antifreeze container handy. Reconnect the water supply. Turn the Pump
switch on, and direct the flow of antifreeze into the container, taking
care not to dilute it when water starts flowing through. Antifreeze left
undiluted can be reused.
Summary of Contents for SprayWand P-500
Page 2: ......
Page 37: ...35 P a g e Figure 23 Pump exploded view ...