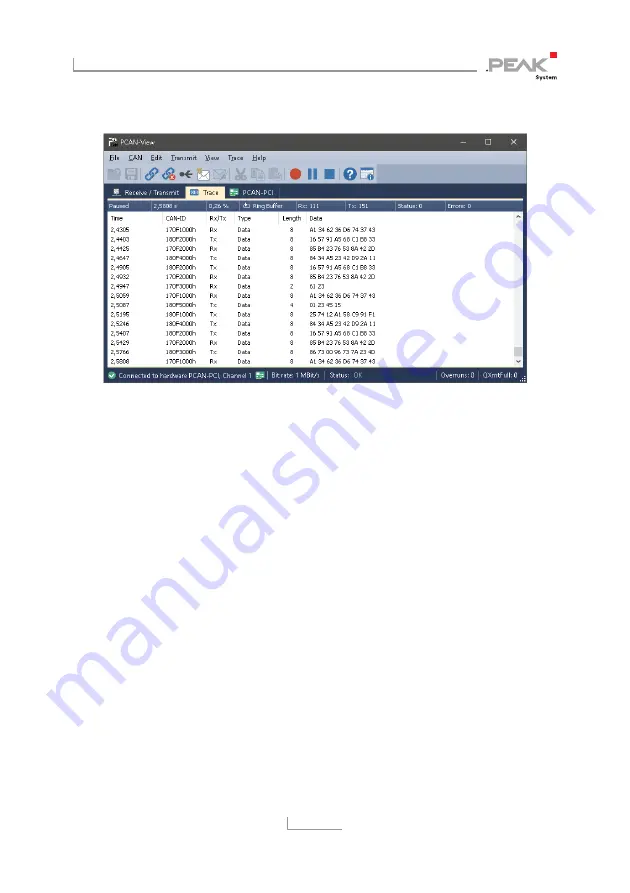
PCAN-PC/104 – User Manual
29
4.1.2
Trace Tab
Figure 16: Trace tab
On the
Trace
tab, the data tracer (data logger) of PCAN-View is used
for logging the communication on a CAN bus. During this process
the messages are cached in the working memory of the PC.
Afterwards they can be saved to a file.
The Tracer runs either in linear or in ring buffer mode. The linear
buffer mode stops the Tracer as soon as the buffer is full. The ring
buffer mode overwrites the oldest messages by new ones as soon
as the buffer is full.