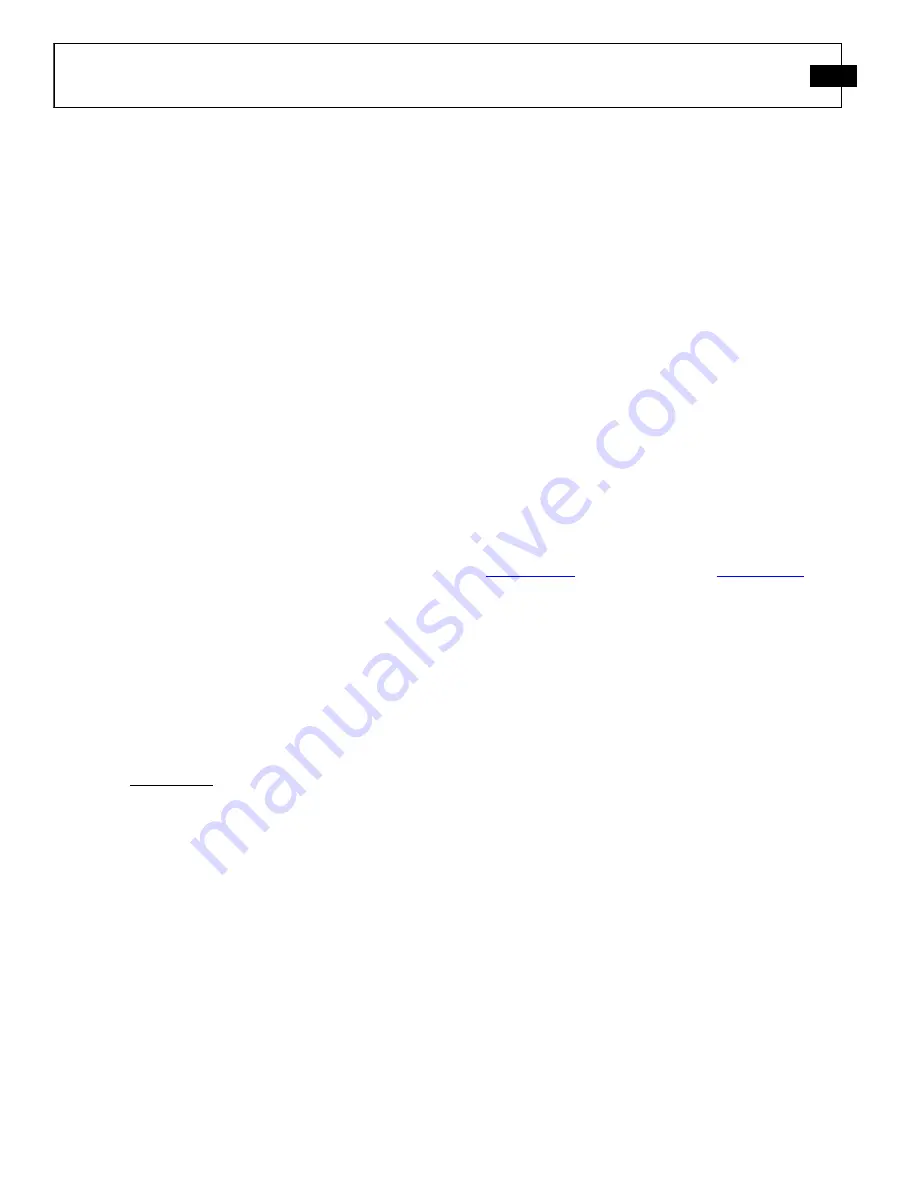
Manual Number: 32650
Manual Revision: D
ECR Number: 42629
3710 series DC Accelerometer Operating Guide
3
If the sensor is extended, in the case of an integral cable
sensor, or a cable length other than 10 ft is used, in the
case of sensor with an integral connector, the offset volt-
age will change. To determine the accelerometer’s offset,
rotate the unit 90° so that the sensor is on its side with the
sensing axis perpendicular to Earth’s gravity and record
the DC output. This value is the new “zero-g offset volt-
age.”
To insure that ground loops are not induced, the shield
should only be terminated at one end. Typically, the
shield of the cable is tied to the sensor housing. If the sen-
sor is mounted with an isolation pad (or other form of
electrical isolation) from the test structure, then the shield
should be tied to signal ground at the instrumentation end.
Otherwise, leave the cable shield floating or not connect-
ed at the instrumentation end.
8.0
Sensor Verification
If the sensor has been handled in a rough manner or before
using a sensor for a critical measurement application, it is a
good idea to verify that the sensor’s sensitivity is still within
specification. An accurate static calibration of the 3710 series
can be performed using the Earth’s Gravitational Field as a
reference. The sensor can simply be “flipped” (rotated 180°)
in the Earth’s Gravity to obtain the scaling factor (sensitivity)
and DC offset. First, place the accelerometer in a +1g orienta-
tion so that the base is resting on the table and the model num-
ber is facing up. The sensing axis will be parallel with the
Earth’s gravity with the sensor experi1g acceleration.
Record the DC output by using a DVM. Then rotate the sensor
180° so that the sensor is inverted (the top of the sensor is rest-
ing on the table) and the sensor is experiencing –1g accelera-
tion. Record the DC output. To calculate the sensitivity of the
accelerometer, refer to equation 8.1.
Sensitivity = (+1g) – (-1g)
Eq 8.1
2
9.0
Sensor Calibration
Due to ISO 9001, ISO Guide 25, or other contractual require-
ments, it may become necessary to send the accelerometer
back to PCB for recalibration. In this case, a complete back-
to-back frequency response test will be performed and the
“zero-g” offset voltage will be checked with NIST traceable
equipment.
10.0
Maintenance and Repair
Because of the sophisticated nature of PCB instrumentation,
field repair of the equipment is not recommended. Most PCB
sensors are of modular construction and are factory repairable.
A repair or replacement quotation is available at no charge.
Before returning equipment for repair, it is recommended that
the user confer with a factory application engineer (or inter-
national representative) to first troubleshoot the problem.
11.0
Return Procedure
To expedite the repair process, contact a factory Application
Engineer to obtain a Return Material Authorization (RMA)
number prior to sending equipment to the factory. Please have
information, such as model number, serial number and de-
scription of the problem, available.
Customers outside the U.S. should consult their local PCB
distributor for information on returning equipment. For excep-
tions to this guideline, please contact the International Sales
department to request shipping instructions and an RMA.
For further assistance, please call (716) 684-0001 or fax us at
(716) 684-0987. You may also receive assistance via e-mail at
or visit our web site at
www.pcb.com
.
12.0
Customer Service / Warranty
The employees of PCB strive to provide superior, unmatched
customer service. Should you at any time find yourself dissat-
isfied with any PCB product for any reason, consult a factory
Application Engineer or local representative/distributor to
discuss repair, refund, or exchange procedures.
When unexpected measurement problems arise, call our 24-
hour SensorLine
TM
at (716) 684-0001 to discuss your immedi-
ate dynamic instrumentation needs with a PCB Application
Engineer.