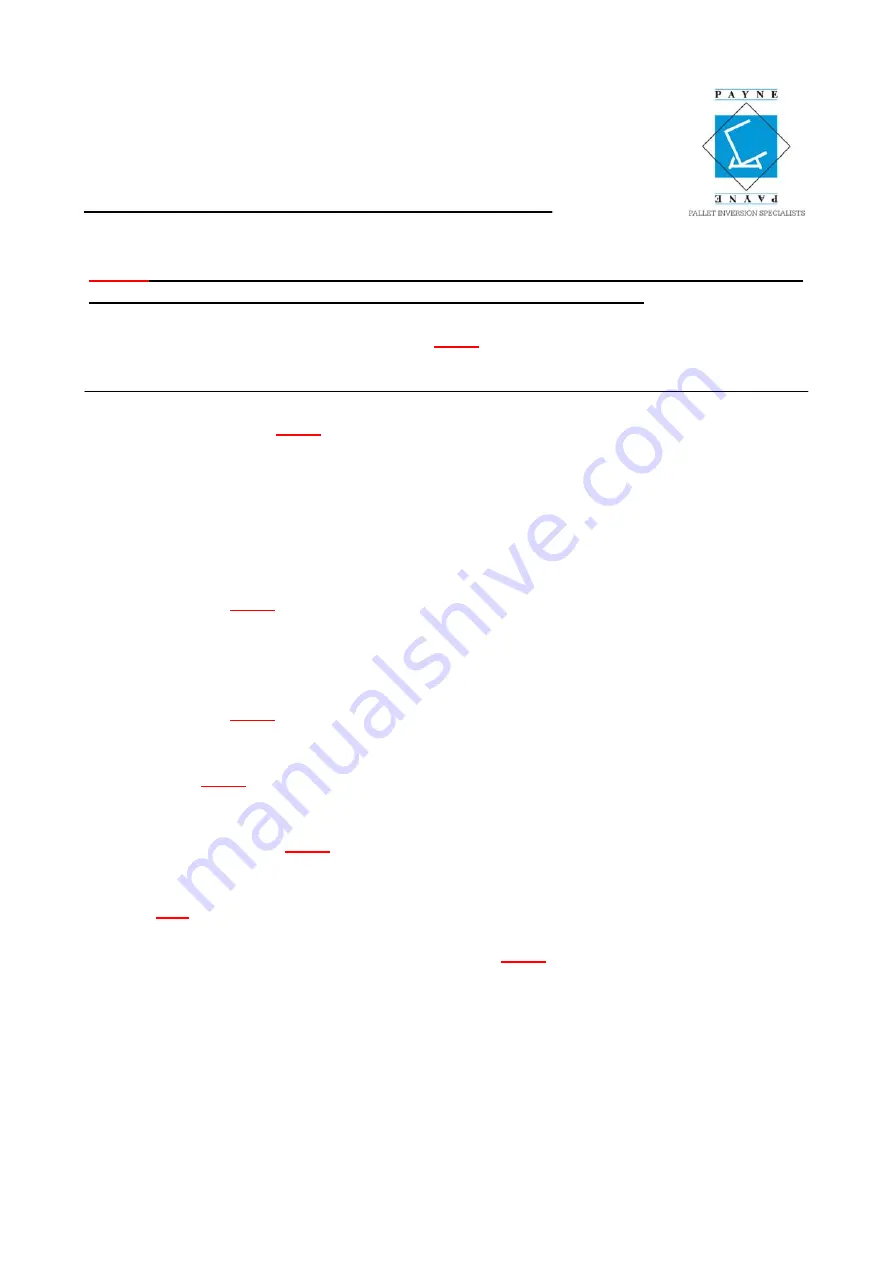
09/2012
RAR
VERSION
5
4
SAFETY
PRECAUTIONS
SAFETY:
THE
MACHINE
IS
TO
BE
USED
ONLY
IN
ACCORDANCE
WITH
SAFTEY
GUIDELINES
AND
IS
NOT
TO
BE
USED
FOR
ANY
OTHER
PURPOSE
THAN
ORIGINALLY
INTENDED.
The
machine
is
fitted
with
a
run
button,
which
MUST
be
released
in
all
possible
emergency
situa
‐
tions,
disabling
the
machine.
The
following
guidelines
MUST
be
obeyed
and
the
machine
operated
in
strict
accordance
with
the
operators
manual:
•
Only
fully
authorised
personnel
may
operate
this
machine.
•
Only
fully
authorised,
suitably
qualified
personnel
may
carry
out
maintenance
operations
on
this
machine.
•
The
machine
MUST
only
be
operated
when
the
area
within
the
fixed
guards
is
clear.
Nobody
may
enter
this
area
with
the
machine
in
operation.
•
At
no
point
may
any
person/persons
enter
the
area
under
the
machine
body.
•
The
machine
MUST
only
be
operated
within
the
maximum
load
capacity
for
which
it
was
designed.
•
All
loads
MUST
be
located
securely
in
the
machine,
with
the
leading
edge
placed
against
the
fixed
rear
wall.
•
The
electrical
supply
MUST
be
isolated
and
suitably
locked
off,
when
carrying
out
any
maintenance
tasks.
•
Do
NOT
tamper
with
or
alter
the
machine
in
any
way.
•
Correct
personal
protective
and
safety
equipment
MUST
be
used
at
all
times
and
in
accordance
with
government
health
and
safety
and
site
specific
guidelines.