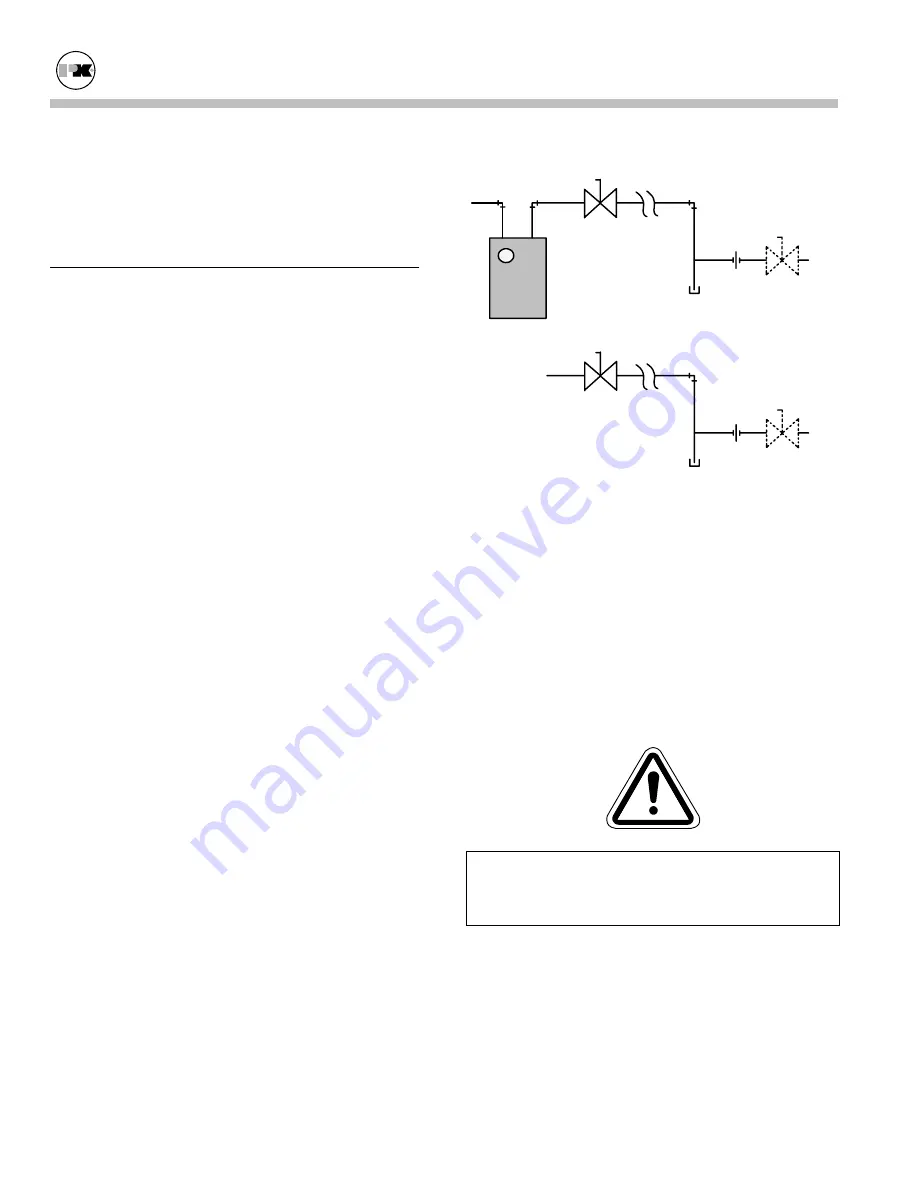
Gemini™ Twin-Fuel Gas-Fired Boiler
Gas Pressure Adjustment
Test of Motorized Gas Valves
4.2 G
AS
P
IPING
Before making the gas hook-up, make sure the boiler
is being supplied
only
with the fuels shown on the
boiler nameplate. The boiler is designed to operate on
vaporized
natural gas and propane only.
Do not
use
any type of liquid fuel.
Do not
attempt to fuel the
boiler with MAPP gas, sewage gas, coal gas, or other
fuels.
Gas train connection sizes are shown in the Gas Train
Connection table on the previous page for the different
models available.
The boiler shall be installed such that the gas ignition
system components are protected from water (drip-
ping, spraying, rain, etc.) during appliance operation
and service (circulator replacement, control replace-
ment, etc.).
The two gas pressure regulators supplied with the
boiler are set during a factory fire-test to provide the
proper pressure to the main burner: 6 inches W.C. in-
let pressure to the regulators for both natural gas and
propane.
The gas train components are designed to handle a
maximum inlet pressure of 14 inches W.C.(1/2 psig).
If the available gas pressure exceeds 14 inches W.C.
on either the natural gas or propane supply a suitable
intermediate gas pressure regulator of the "lock up"
type must be provided to reduce the pressure to less
than 14 inches W.C. All boilers are designed to oper-
ate at rated input with a minimum inlet pressure of 6
inches W.C. with natural gas, 6 inches W.C. with LP
gas.
shutoff
(on boiler)
union
drip leg
remote gas shutoff
(not supplied)
meter
natural gas
supply
propane
supply
shutoff
(on boiler)
union
drip leg
remote gas shutoff
(not supplied)
Figure 4-2 Gas Supply Piping
(Refer to table above for connection sizes.)
Install a sediment trap (drip leg) and a union connec-
tion ahead of the primary manual shutoff valves on the
boiler as shown in the figure above.
All gas piping must be installed in accordance with
National Fuel Gas Code, ANSI Z223.1, latest edition,
and any other local codes which may apply; in Canada
gas piping must be installed in accordance with CAN-
B 149.
General Warning
Warning! All threaded connections must be made us-
ing a pipe compound that is resistant to the action of
liquefied petroleum gases. Do not use Teflon
ä
tape
on gas line threads.
The boiler and all gas piping connections must be
pressure tested and must be checked for leaks before
being placed into service. Test with compressed air or
gas if possible.
The boiler must be disconnected at both boiler manual
- 6 -
Summary of Contents for TBIG-03
Page 20: ...Gemini Twin Fuel Gas Fired Boiler 8 1 1 Wiring Diagram Lo Hi Lo 18...
Page 21: ...Parts and Technical Support 8 1 2 Control Logic Diagram Lo Hi Lo 19...
Page 22: ...Gemini Twin Fuel Gas Fired Boiler 8 1 3 Wiring Diagram On Off 20...
Page 23: ...Parts and Technical Support 8 1 4 Control Logic Diagram On Off 21...
Page 24: ......