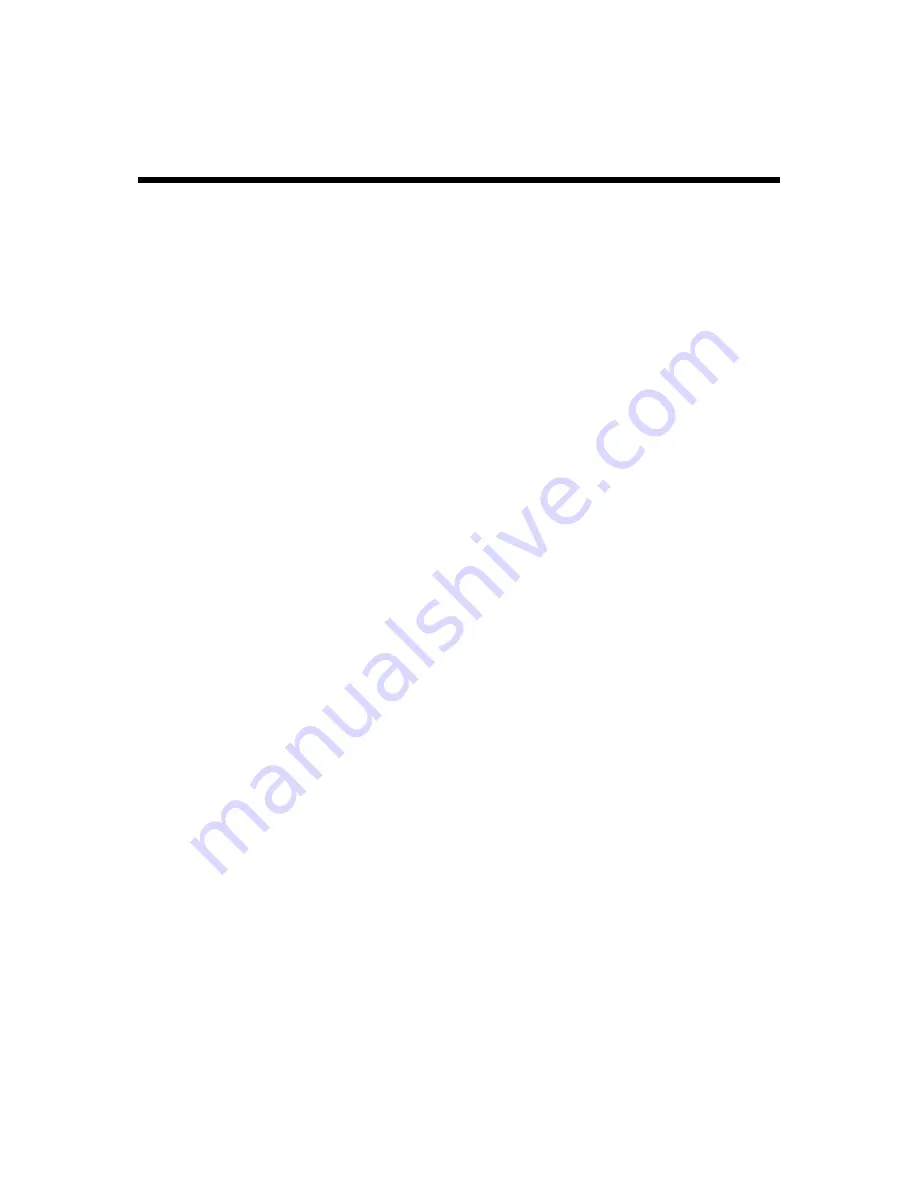
21
TSM DS 50-003/REV.C/031-300-190-003/04-20-07
DS50 TROUBLE SHOOTING MANUAL LEVEL 3
4. ADJUSTING CALIBRATION DATA
Use the flowcharts in the continuation of this manual to locate the section appropriate
for your adjusting needs.
Remember you must be fully familiarized with section 2 and 3 in order to proceed
with section 4.
Test the hardware, using trouble shooting manual 2 & 3, before you consider adjusting
the calibration data.
Always consider that the system left the crane manufacturer fully calibrated and
passed the quality tests. Always consider calibration and crane specification during
the adjusting procedure.
Ensure a safe environment. Secure the crane and the surrounding area. Do not
overload the crane and truck during the adjusting process. Always consider and refer
to the crane load chart. Always measure actual geometrical values. Use only tested,
inspected and known test weights for load testing. The load must be freely suspended
and lifted in a vertical straight line. Always initially hoist the load of the ground.The use
of a “dead eye” (hook in the ground) is not permitted for any adjusting methods.
Use a tested inclinometer (level indicator) with a minimum resolution of 0.25 degree
to measure the boom angle.
Ensure that your measuring tape is in good condition. When testing the radius mount
the beginning of the tape exactly on the center line of rotation. Note the display
indicates the radius or boom length in resolution of 1/10 ft. - not in inches.