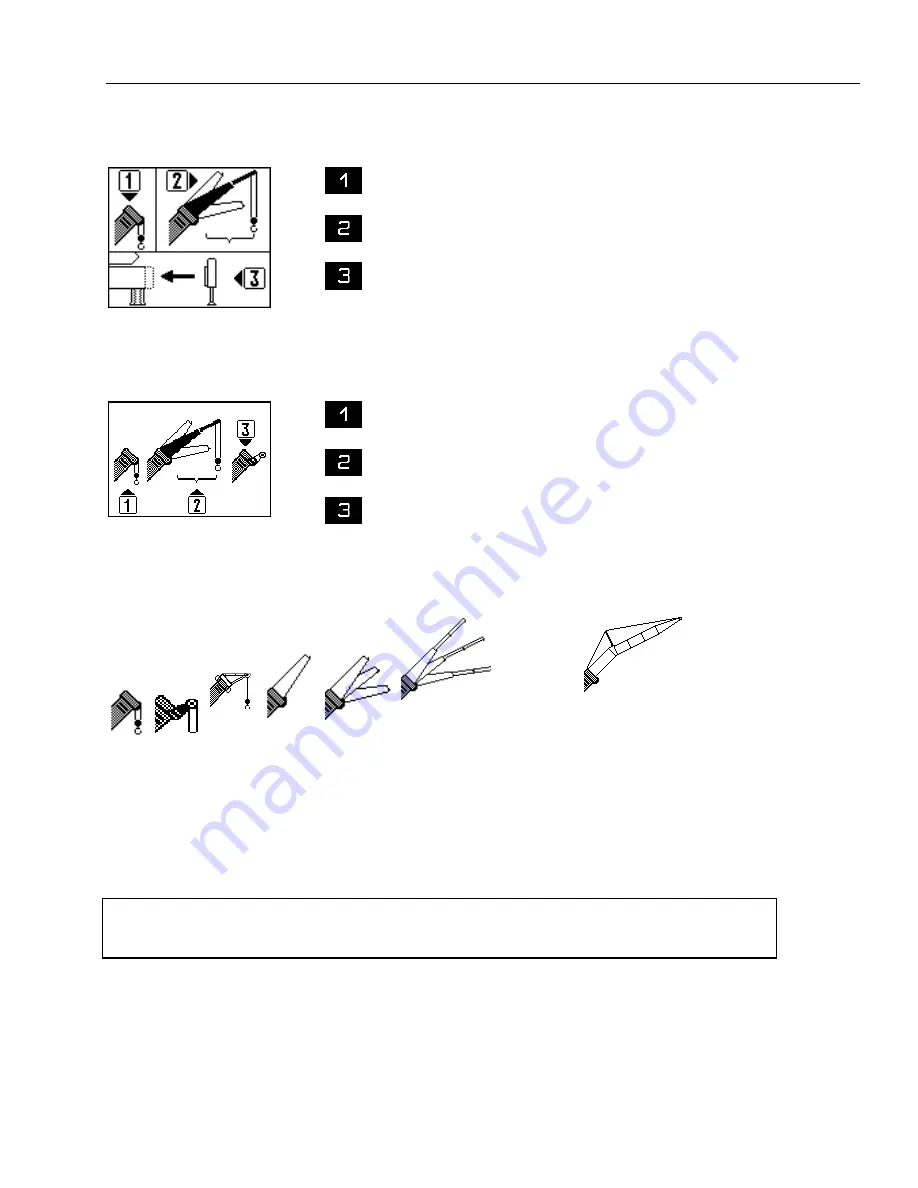
Configuration Setup
15
© PAT Rev. 7 03/27/01 // MO
191318_7.DOC
•
Setting the boom configuration
Main boom / aux. Boom nose operation
Operation with boom extensions
Rigging mode operation*
*
for cranes with rigging mode for
outrigger box
installation only
or
Main boom
Operation with boom extensions
Aux. boom nose operation
main
boom
aux.
boom
nose
A-
frame
boom
ext.
fixed
ext.
fixed,
offsettabl
e
extension
tele-
offsettable
extension
fixed jib
For detailed symbol explanation of extensions, please refer to Appendix A in this
manual.
Summary of Contents for DS 350/1318 Graphic
Page 2: ......
Page 4: ......
Page 6: ......
Page 55: ...Troubleshooting PAT Rev 7 03 27 01 MO 191318_7 DOC 49 ...