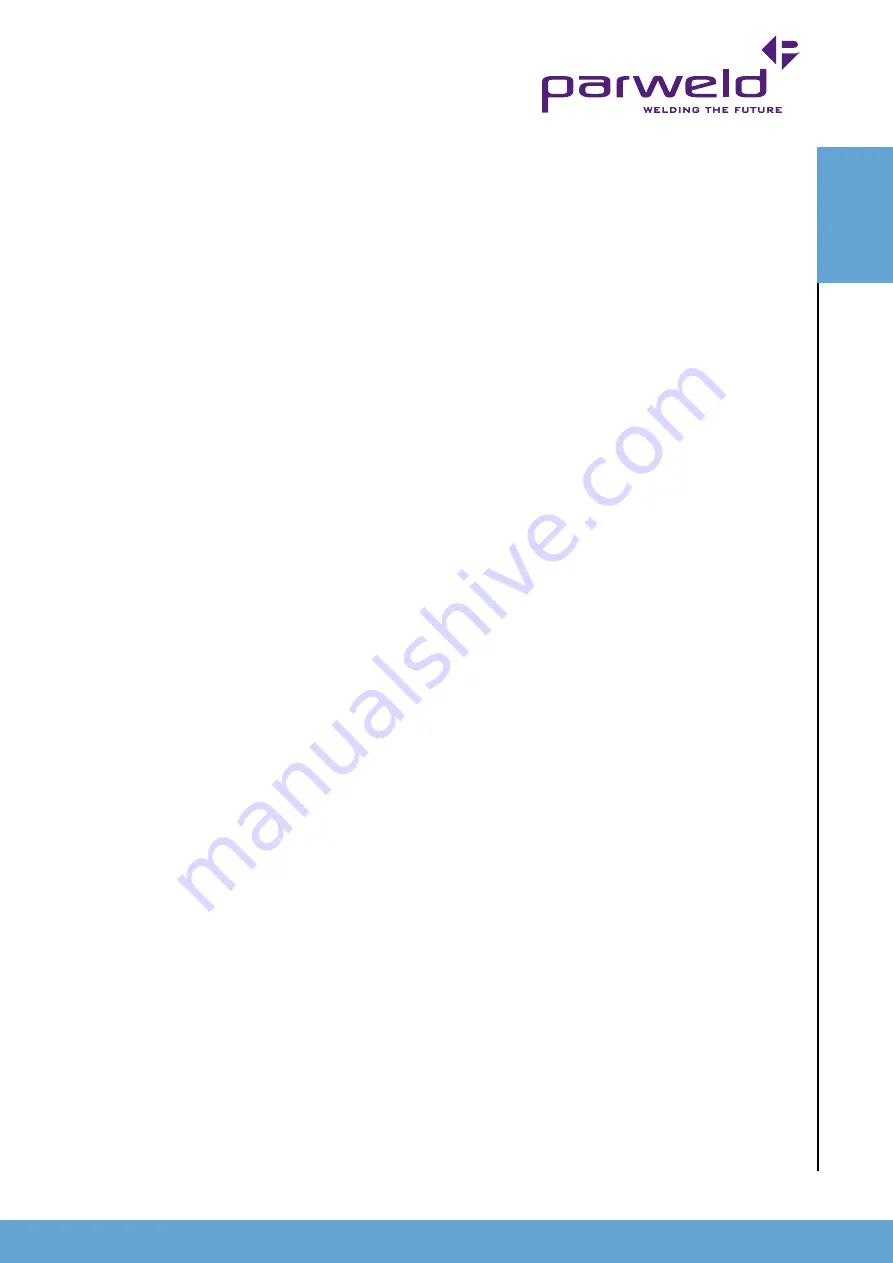
www.parweld.co.uk
7
14) power pulsing.
When illuminated the output power will be
pulsed in accordance with the variables selected on the main control
15) amperage Display.
Displays the preselected or actual welding
amperage.
16) Multifunction Display.
Displays other parameter as indicated
by the illuminated LED at the side of the display V=Voltage, S=
Seconds, Hz= Hertz (frequency), %=Percentage value.
17) MMa selector
. This button selects MMA welding and will latch
on the power output when the LED is illuminated.
18) parameter adjustment Dial.
This knob is used to adjust
multiple parameters dependant upon the parameter selected on the
pictogram above the knob.
18) parameter toggle buttons.
These buttons toggle the selected
parameter and can be used to select the require parameter as
indicated by the LED on the Pictogram.
5.0 Installation
read entire installation section before starting installation.
SaFetY preCautIOnS
• ELECTRIC SHOCK can kill.
• Only qualified personnel should perform this installation.
• Only personnel that have read and understood the Operating
Manual should install and operate this equipment.
• Machine must be grounded per any national, local or other
applicable electrical regulations.
• The power switch is to be in the OFF position when installing
work cable and electrode cable and when connecting other
equipment.
5.1 unpacking the Machine
Carefully remove the machine from the packaging, we recommend
you retain the packaging until the machine has been fully installed
and tested incase it has been damaged in transit and has to be
returned to the re-seller.
5.2 location
Be sure to locate the welder according to the following guidelines:
In areas free from moisture and dust.
Ambient temperature between 0-40
0
C.
In areas free from oil, steam and corrosive gases.
In areas not subjected to abnormal vibration or shock.
In areas not exposed to direct sunlight or rain.
Place at a distance of 12” (300 mm) or more from walls or similar
that could restrict natural airflow for cooling.
5.3 Input and grounding connection
WarnInG
Before starting the installation, check that your power supply
is adequate for the voltage, amperage, phase, and frequency
specified on the Machine nameplate.
Operate the welding power source from a single-phase 50/60 Hz,
AC power supply. The input voltage must match one of the electrical
input voltages shown on the input data label on the unit nameplate.
The XTT-202P AC/DC machine should only be used on 230V supply.
Refer to the specifications table for voltage tolerances.
Have a qualified electrician connect the input plug. For long runs
over 30m, larger copper wires should be used. The green/yellow
wire in the input cable connects to the frame of the machine. This
ensures proper grounding of the machine when the machine plug is
inserted into the receptacle.
5.4 Output polarity Connections
Electrode polarity
MMA electrodes are generally connected to the ‘+’ terminal and the
work return lead to the ‘-’ terminal
But if in doubt consult the electrode manufacturer’s literature.
IF TIG welding the torch should always be connected to the
‘-’ terminal.
5.5 torch installation
MMA cable connections
Connect electrode lead to positive terminal
TIG welding cable connection
Connect the TIG torch to the - terminal
5.6 Work return lead connection
MMA cable connections
Connect work return lead to negative terminal
TIG welding
Connect the work return lead to the + terminal
5.7 Liquid Cooling
The Liquid Cooled system on your Welding Machine
It is critical to correctly maintain the Cooling unit if fitted to your
system. If your machine does not have a liquid cooling system for
the torch this can be retro fitted to most models should you wish to
enhance your package in the future.
The correct coolant (Parweld Ultracool, Stock Code XTSUC) must
be used in the unit to the required level indicated on the unit. In
addition to cooling the torch, the Coolant lubricates the workings of
the pump, contains antibacterial agents and Anti-Freeze to stop the
liquid freezing in low temperatures.
It is also important to regularly inspect all connecting hoses between
the cooling unit & the machine & the machine to the welding torch.
This will identify any potential leaks that will affect the coolant level &
potentially damaging the cooling unit, welding machine and torch.
Should damage be caused by a failure to maintain the correct level
of the correct Coolant within the system it will void any warranty
claims.
O
pera
t
IO
n
12) Gas test (tIG)
, Pressing this button switches on the shielding
gas for 15s to allow purging of the torch and checking of the gas
flow. Pressing the button before 15s has expired will stop the gas
flow.
13) HF ignition.
When illuminated the TIG torch will start with High
frequency ignition not requiring contact of the Tungsten electrode
with the work (TIG Mode).