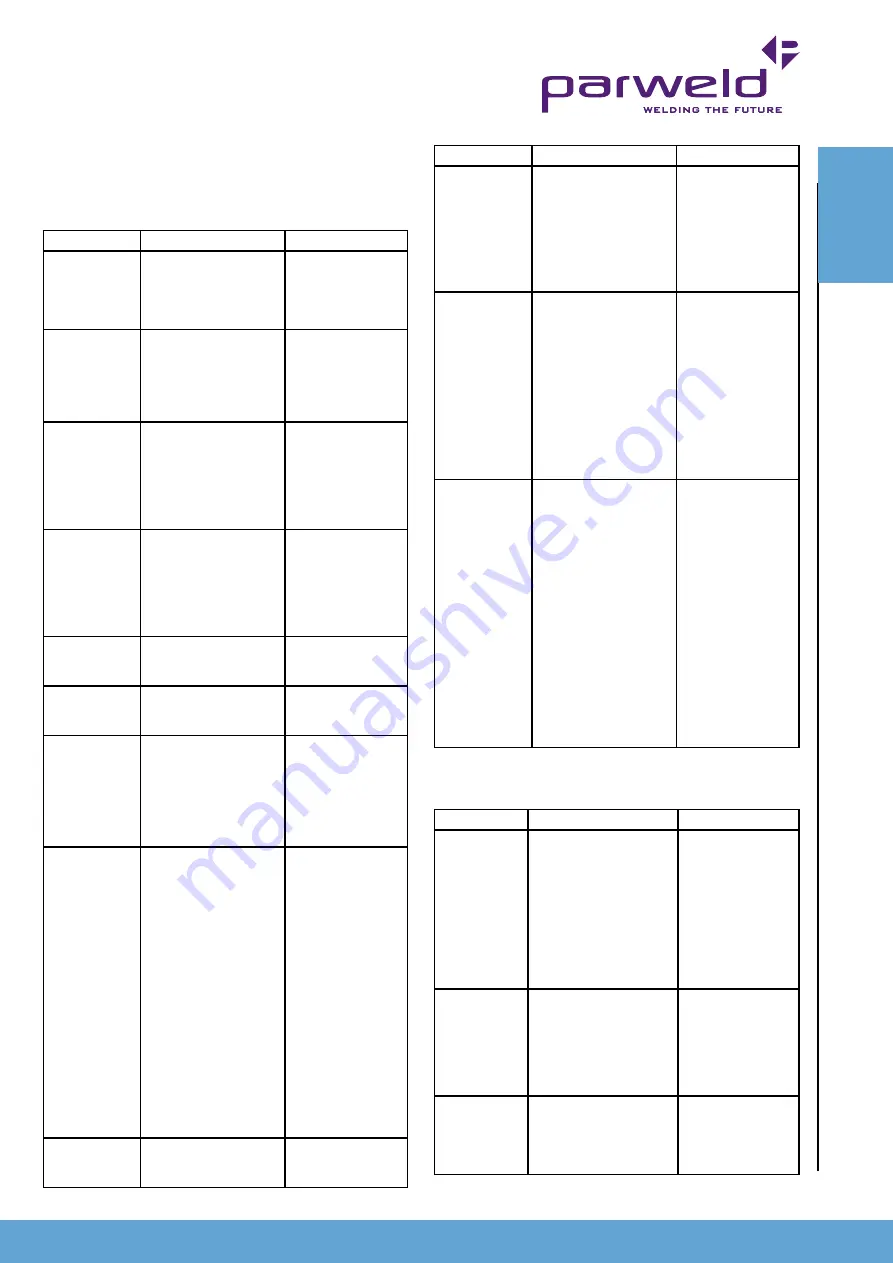
www.parweld.co.uk
tIG welding problems
Weld quality is dependent on the selection of the correct
consumables, maintenance of equipment and proper welding
technique.
Description
possible Cause
Remedy
Excessive bead
build up or poor
penetration or
poor fusion at
edges of weld
Welding current is too
low
Increase weld
current and/or faulty
joint preparation
Weld bead too
wide and flat
or undercut at
edges of weld
or excessive
burn through
Welding current is too
high
Decrease weld
current
Weld bead
too small or
insufficient
penetration or
ripples in bead
are widely
spaced apart
Travel speed too fast
Reduce travel speed
Weld bead
too wide or
excessive
bead build up
or excessive
penetration in
butt joint
Travel speed too slow
Increase travel
speed
Uneven leg
length in fillet
joint
Wrong placement of
filler rod
Re-position filler rod
Electrode melts
when arc is
struck
Electrode is connected
to the ‘+’ terminal
Connect the
electrode to the ‘-‘
terminal
Dirty weld pool
(a) Electrode
contaminated through
contact with work piece
or filler rod material
(b) Gas contaminated
with air
(a) Clean the elec-
trode by grinding off
the contaminates
(b) Check gas lines
for cuts and loose
fitting or change gas
cylinder
Electrode melts
or oxidizes
when an arc is
struck
(a) No gas flowing to
welding region
(b) Torch is clogged with
dust
(c) Gas hose is cut
(d) Gas passage
contains impurities
(e) Gas regulator is
turned off
(f) Torch valve is turned
off
(g) The electrode is too
small for the welding
current
(a) Check the gas
lines for kinks or
breaks and gas
cylinder contents
(b) Clean torch
(c) Replace gas
hose
(d) Disconnect gas
hose from torch
then raise gas
pressure to blow
out impurities.
(e) Turn on
(f) Turn on
(g) Increase
electrode diameter
or reduce the
welding current
Poor weld finish
Inadequate shielding
gas
Increase gas flow or
check gas line for
gas flow problems
Description
possible Cause
Remedy
Arc flutters
during TIG
welding
(a) Tungsten electrode is
too large for the welding
current
(b) Absence of oxides in
the Weld pool.
(a) Select the right
size electrode. Refer
to basic TIG welding
guide.
(b) Refer basic TIG
welding guide for
ways to reduce arc
flutter
Welding arc
cannot be
established
(a) Work clamp is not
connected to the work
piece or the work/torch
leads are not connected
to the machine
(b) Torch lead is discon-
nected
(c) Gas flow incorrectly
set, cylinder empty or
the torch valve is off
a) Connect the work
clamp to the work
piece or connect
the work/torch leads
to the right welding
terminals.
(b) Connect it to the
‘.’ terminal.
(c) Select the right
flow rate, change
cylinders or turn
torch valve on.
Arc start is not
smooth
(a) Tungsten electrode is
too large for the welding
current .
(b) The wrong electrode
is being used for the
welding job.
(c) Gas flow rate is too
high.
(d) Incorrect shielding
gas is being used.
(e) Poor work clamp
connection to work piece
(a) Select the right
size electrode
(b) Select the right
electrode type.
Refer to basic TIG
welding guide
(c) Select the correct
rate for the welding
job. Refer to basic
TIG welding guide
(d) Select the right
shielding gas. Refer
to basic TIG welding
guide
(e) Improve
connection to work
piece
power source problems
Description
Possible cause
Remedy
The welding
arc cannot be
established
(a) The primary supply
voltage has not been
switched on
(b) The welding power
source switch is switched
off
(c) Loose connections
internally
(a) Switch on the
primary supply
voltage
(b) Switch on the
welding power
source.
(c) Have a
qualified service
engineer repair the
connection
Maximum
output welding
current cannot
be achieved
with nominal
mains supply
voltage
Defective control circuit
Have a qualified
service engineer
inspect then repair
the welder
Welding
current
reduces when
welding
Poor work lead
connection to the work
piece
Ensure that the
work lead has a
reliable electrical
connection to the
work piece
F
aul
t
FI
n
DIn
G
13