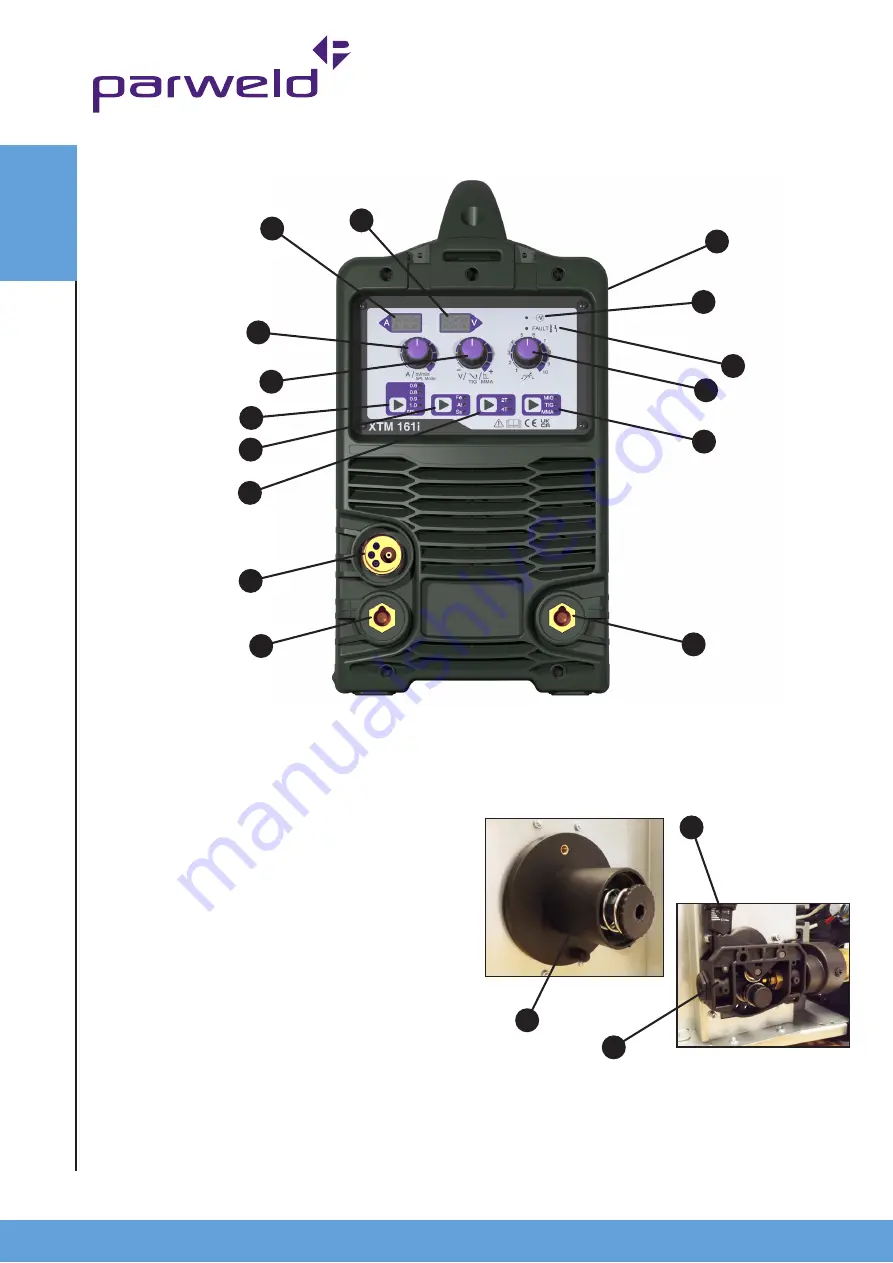
www.parweld.co.uk
6
1. Amperage Display. Displays the welding amperage when the
wire size is selected, or wire speed during welding when SPL
(manual mode) is selected.
2. Voltage Display. Displays the welding voltage during welding.
3. Amperage control for adjusting the Amperage (wire feed speed).
4. Voltage control. This function controls the MIG welding voltage.
It can be adjusted infinitely within the working voltage range. It
also controls TIG Downslope and MMA Arc Force.
5. Wire Diameter / SPL (Manual MIG).
6. Material Type Selector (MIG).
7. Latching trigger selector. 2T denotes momentary trigger,
4T denotes latching trigger.
8. MIG Torch euro connector, for connection of the MIG or TIG
torch.
9. Positive output for MMA electrode holder or TIG torch work
return lead.
10. Negative output connection used to connect the work return
lead for MIG or MMA welding. This is the 50mm Twist lock
connection socket.
11. Process Selector MIG, TIG, or MMA.
12. Inductance control, this hardens or softens the arc in MIG
welding.
13. Fault Light.
14. Power Indicator shows when the machine is turned on.
15. ON/OFF Switch for switching the mains supply to the machine
on or off (mounted on the rear of the machine).
16. MIG wire spool holder accepts 5KG (200mm ) or 1KG spools.
17. Wire feed box.
18. Wire tension adjuster.
CONTROLS
4.0 Description of Controls
1
18
2
3
4
5
6
7
8
9
17
16
10
11
12
14
13
15