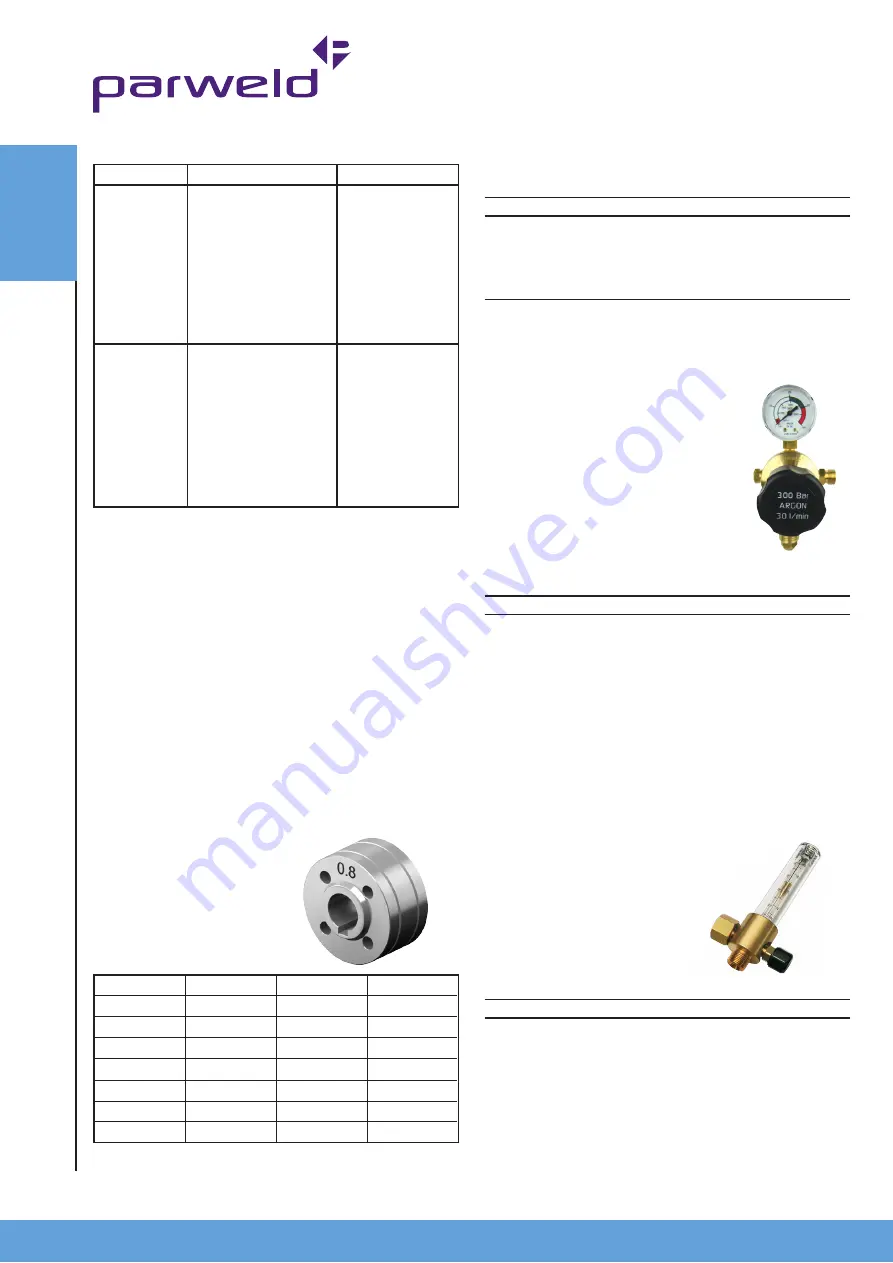
www.parweld.co.uk
12
POWER SOURCE PROBLEMS
Description
Possible cause
Remedy
A total loss of
power, pilot
lamp is off,
no output,
the fan is not
operating
(a) Failure of input
voltage
(b) Possible over voltage
(c) Internal fault with the
machine
(a) Re-establish
mains supply
(b) Check voltage
and if necessary
move machine to
alternative supply
(c) Have a qualified
service engineer
inspect then repair
the welder
Fault lamp is
on, no power
output
(a) Machine overheated
(b) Over current state
(c) Internal fault with
machine
(a) Allow to cool
with fan running
(b) Switch off
mains power to the
machine and re start
(c) Have a qualified
service engineer
inspect
then repair the
welder
ROUTINE MAINTENANCE
The only routine maintenance required for the power supply is a
thorough cleaning and inspection, with the frequency depending on
the usage and the operating environment.
Warning
Disconnect primary power at the source before removing the cover.
Wait at least two minutes before opening the cover to allow the
primary capacitors to discharge.
To clean the unit, remove the screws securing the outer cover,
lift off the outer cover and use a vacuum cleaner to remove any
accumulated dirt and dust. The unit should also be wiped clean,
if necessary; with solvents that are recommended for cleaning
electrical apparatus.
8.0 Accessories
8.1 Feed Rolls
Part No.
Groove
Wire Sizes
Wires
DR2V0608
Plain V
0.6 - 0.8
Fe, Ss
DR2V0609
Plain V
0.6 - 0.9
Fe, Ss
DR2V1012
Plain V
1.0 - 1.2
Fe, Ss
DR2K0809
Knurled V
0.8 - 0.9
FC
DR2K1012
Knurled V
1.0 - 1.2
FC
DR2U0809
Plain U
0.8 - 0.9
Al
DR2U1012
Plain U
1.0 - 1.2
Al
8.2 Torch Spares
Stock Code
Description
CKE403
Electrode Holder with 3m Lead
CKC403
Earth Lead 3m with Clamp
PRO17-12S1MPG
Pro-Grip TIG Torch
WP17AK
Tig Spares Kit in Plastic Case
8.3 Gas Equipment
Everyday Gas Regulators – 300 BAR
Single Stage
Features
Flow rate up to 96m
3
/h (3389 ft
3
/h)
• Full 300 bar capability
• Outlet pressure indicated on the bonnet
• Bottom entry design suited for top outlet
cylinder valves
Fittings
• Fitted with standard
3
/
8
” BSP outlet
• Fitted with
5
/
8
” BSP inlet connections
Stock Code Description
Maximum Outlet Pressure
E700140
Argon Preset Regulator
3.0 Bar
E700141
Argon Indicator Regulator
3.0 Bar
E700113
1 Gauge Argon
30 lpm flow
E700123
2 Gauge Argon
30 lpm flow
8.4 Flow Meters
Features
• Designed from brass bar whilst the tube and cover are moulded
from high quality polycarbonate to ensure high impact resistance
and clarity
• Calibrated to operate at an inlet pressure
of 30PSI
• Sensitive needle valve provides easy adjustment
and the downward facing outlet connection
eliminates hose kinking.
Fittings
• Fitted with standard
3
/
8
" BSP inlet and
outlet connections
Stock Code
Description
706100
Flow Meter Mixed Gas 15 lpm
ACCESSORIES