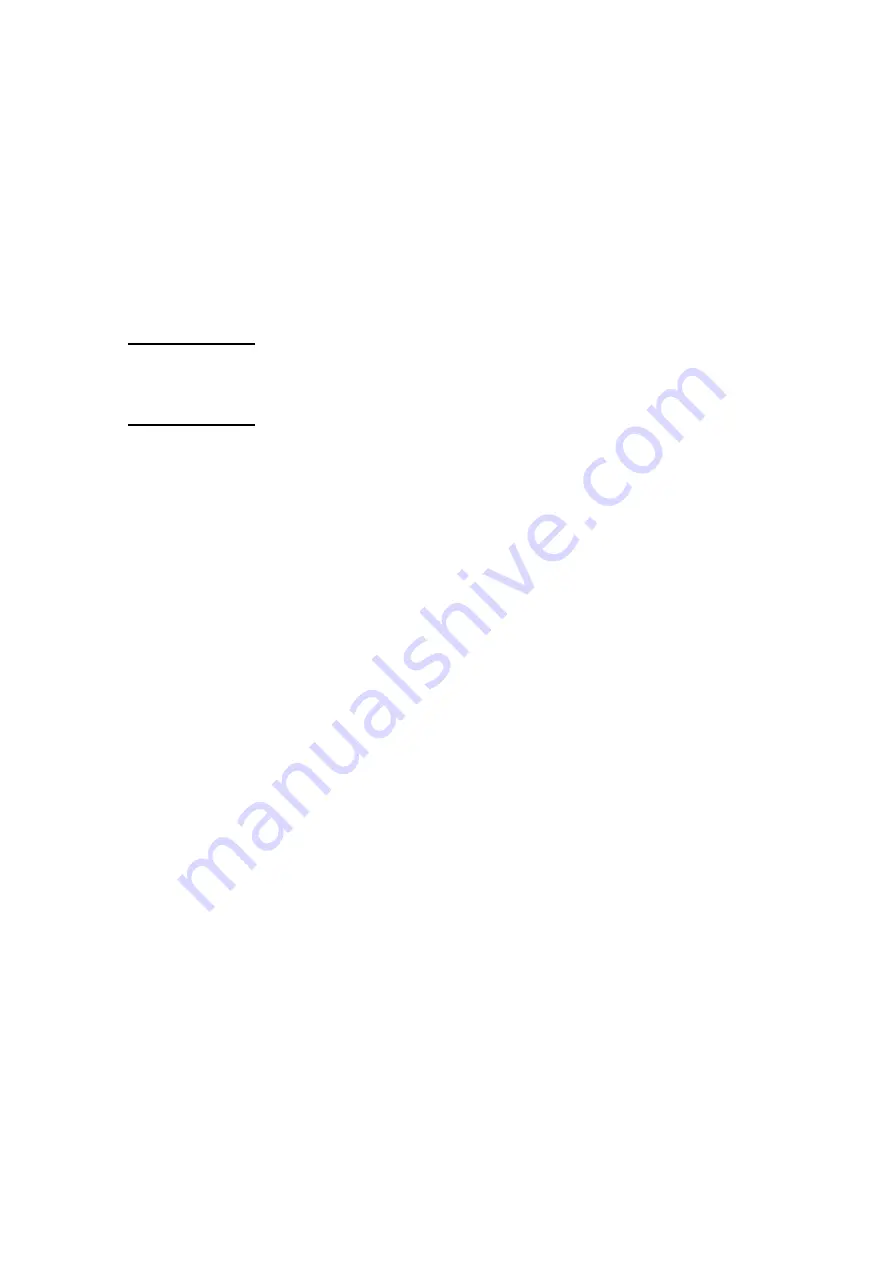
Operating Instructions
Before operation:
1. Make sure all parts of the product are clean and free from debris , check for any
loose parts.
2. Check that no leakages are evident while the tool is in resting position or while the
tool is tested without terminal connector.
ATTENTION
Do not operate crimp tool when dies are not in place.
ATTENTION
Be sure to select correct dies to suit the connector you are crimping.
Improper selection can result in danger to the operator, damage to the unit or an
inferior joint.
During operation:
1. Keep tool clean and free from debris. Excessive dirt & debris can contribute to the
breakdown of the hydraulic system. Regular checks during operation cycle should be
made for foreign matter or debris and removed immediately.
3. Stop operating immediately if abnormalities occur and refer to the
Trouble-Shooting
section of this manual, if:
• Compression of lugs cannot be completed
• Dies cannot be inserted or removed
• Piston is stuck or unable to retract after operation
After operation:
1. Clean the product and check that all pieces are in fine working condition.
2. Apply rust preventive oil to the product and dies before returning it to the
carrying case.
ISSUE 10/13 ORIGINAL
PAGE 5