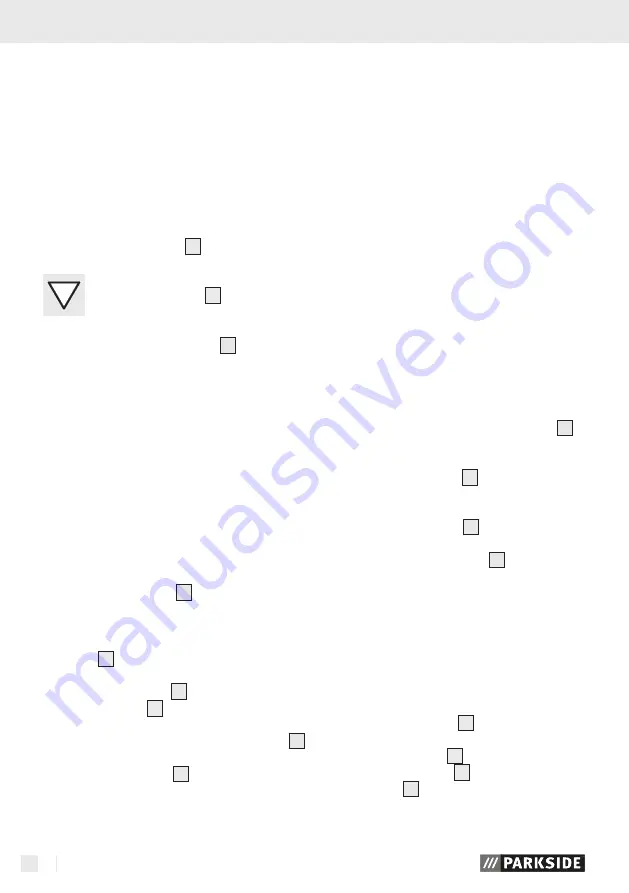
GB/CY
12
□
Ensure that the permissible operating pressure of
8 bar at the device is never exceeded. Opera-
ting pressure that is too high does not provide
any performance increase, but only increases
compressed air consumption and accelerates
wear on the device.
□
Switch on the compressor.
□
Allow the compressor to run once long enough
until maximum tank pressure is reached and the
device is switched off.
□
Place the compressed air tacker on the workpie-
ce and press the trigger
2
.
NOTE:
The compressed air tacker is equip-
ped with a trigger lock
10
. The fastener will
only leave the device when the mouth of the
compressed air tacker is pressed against the
workpiece and the trigger
2
is actuated.
Handling the tool
Note the section with special safety references of
these operating instructions. Having checked that the
fastener driving tool is functioning correctly, apply the
tool to a workpiece and actuate the trigger.
□
Check that the fastener has been driven in corre-
sponding to the work requirements.
– If the fastener is protruding, increase the air
pressure in 0.5 bar increments.
– If the fastener is too deep, decrease the air
pressure in 0.5 bar increments.
□
As an alternative, you can accelerate the work
by keeping the trigger
2
depressed.
□
Set the compressed air tacker against the wor
piece.
□
Press the device against the workpiece until the
mouth
11
touches it. The fastener will leave the
device.
□
As long as the trigger
2
is kept depressed, each
time the muzzle
11
touches the workpiece one
fastener will leave the device.
□
Another alternative is to keep the muzzle
11
pressed against the workpiece.
□
Each time the trigger
2
is actuated, a fastener
will leave the device.
You should endeavour in any event to work with the
lowest possible air pressure. This will give you three
significant advantages:
1) energy will be saved,
2) less noise will be produced,
3) a reduction in fastener driving tool wear will be
achieved.
Avoid triggering the fastener driving tool if the maga-
zine is empty. Any defective or improperly functioning
fastener driving tool must immediately be disconnec-
ted from the compressed air supply and passed to a
specialist for inspection. In the event of longer breaks
in work or at the end of the working shift, disconnect
the tool from the compressed air supply and empty
the magazine. The compressed air connectors of the
fastener driving tool and the hoses should be protec-
ted against contamination. The ingression of coarse
dust, chips, sand etc. will result in leaks and damage
to the fastener driving tooland the couplings.
NOTE:
Fine adjustment with the knurled screw
9
is possible.
□
Turn the knurled screw
9
downwards in order
to drive the fastener more deeply into the work-
piece.
□
Turn the knurled screw
9
upwards in order to
drive the fastener less deeply into the workpiece.
□
Turn the exhaust air aperture
1
to guide the ex-
haust airflow in the desired direction.
□
After finishing work, disconnect the device from
the compressor.
Removing jammed fasteners
□
If a staple or nail gets jammed in the magazine
slot, immediately disconnect the compressed air
supply.
□
Open the magazine
7
as described in the
chapter “Loading the magazine“.
□
Open the face plate
12
by pulling the face plate
quick clamping lever
13
in the direction of the
trigger lock
10
.
□
Remove the jammed fastener.
Summary of Contents for PDT 40 E4
Page 3: ...A 1 2 3 4 5 6 7 8 9 10 11 12 13...
Page 4: ...B C...
Page 41: ...BG 44 10 CEN CENELEC...
Page 42: ...BG 45 8 bar 6 mm 45 m s...
Page 43: ...BG 46 GUOTAI 166 EN 1 F CE ANSI ISEA Z 87 1 2010 ANSI eh o o o o 10 10...
Page 44: ...BG 47 10 8 bar 1 2 4 3...
Page 45: ...BG 48 48 10 m 9 mm 1 6 2 7 7 3 7 8 bar 2 10 2 0 5bar 0 5 bar 2 11...
Page 46: ...BG 49 2 11 11 2 1 2 3 9 9 9 1 7 12 13 10 12 13 1 7...
Page 47: ...BG 50 5000 1 2 4 2 3 112 115...
Page 48: ...BG 51 s IAN 315477 800 7694 7694 Ld services rowi electronics com IAN 315477...
Page 54: ...GR CY 58 EN 792 13 2000 13 10 CEN CENELEC...
Page 55: ...GR CY 59 8 bar...
Page 56: ...GR CY 60 6 mm 45 m s GUOTAI 166 EN 1 F CE CE ANSI ISEA Z 87 1 2010 ANSI e kentpo 10...
Page 57: ...GR CY 61 10 10 8 bar 1...
Page 58: ...GR CY 62 2 4 3 10 m 9 mm 1 6 2 B C 7 7 3 7 8 bar 2...
Page 59: ...GR CY 63 10 2 0 5 bar 0 5 bar 2 11 2 11 11 2 1 2 3 9 9 9 1 7 12 13 10 12 13 1...
Page 60: ...GR CY 64 7 5000 1 2 4 2 ROWI Electronics GmbH 3...
Page 61: ...GR CY 65 O 2251 1994 IAN 315477 email www lidl service com...